Inventory stock can include anything from raw materials, work-in-progress items, and finished goods. Having high levels of inventory has its advantages and disadvantages. On one hand, high inventory means that you have a product ready to ship out at all times. On the other hand, high inventory means that you will have increasingly high carrying and holding costs.
Proper inventory management is crucial to be able to promptly meet customer demands without having high costs related to holding too much inventory.
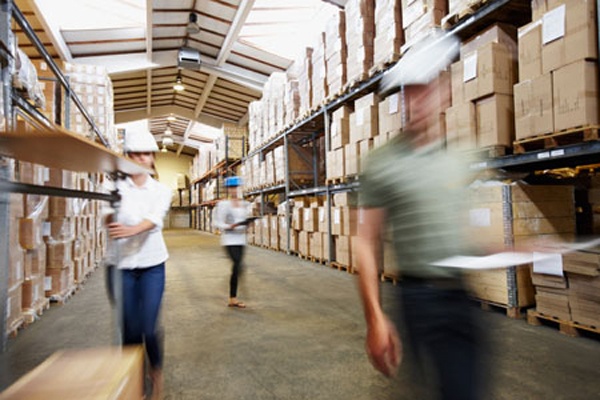
There are a few things to consider when planning to reduce your inventory levels for certain items. For example, it may be worth keeping more items from suppliers that are far away or have long lead times.
As these challenges are presented, operations managers are all asking the same questions - how do we effectively reduce inventory without hindering production? This is where locating the correct inventory reduction method comes into play. When executed properly, inventory reduction will reduce storage costs, production costs, and will prevent items sitting in inventory to become obsolete before they are sold.
7 Methods of Inventory Reduction
Finding the correct strategy can be vital to reducing inventory, and there are various methods to be considered. Thoroughly analyzing each strategy and finding the one that best suits your production facility will allow for an optimized manufacturing operation and an increase in revenue. These 7 methods of inventory reduction include the following:
- Inventory Auditing - Before reducing inventory, it is important to thoroughly examine the products that are offered and determine whether some items should be discontinued. These items will typically have high demand variability, high production and holding costs, and long lead times. Eliminating those items will reduce your overall inventory levels and reduce your costs.
- Demand Forecasting - Accurate demand forecasting is a must when trying to manage your inventory levels. This is a challenging component as demand frequently changes. Having an integrated system that allows for demand forecasting is vital for companies looking to reduce their inventory levels as they will be able to only buy the quantity of materials they need to make the right amount of products.
- Shorten Supply Chain - The reduction of supply chain lead times such as manufacturing and supplying will help with inventory reduction. Choosing suppliers with shorter lead times will reduce your materials holding costs. In addition, reducing the overall manufacturing lead times will require you to hold WIP items for shorter amounts of time.
- Supplier Relationships - Suppliers are extremely important to ensure the efficiency of manufacturing operations. After all, they control the materials that are required for production. It is important to choose suppliers that have fast, reliable, and accurate lead times to allows you to order smaller quantities without the risk of stock-outs. Therefore, establishing an excellent relationship with your supplier can optimize production and reduce inventory through an efficient supply chain.
- Order Size Reduction - Large, infrequent orders for items of varying demand can lead to high inventory holding costs. Keeping orders small and frequent benefits the company through inventory reduction and increasing cash flow. The more inventory on hand, the more the holding costs will be, and the higher the risks of product depreciation.
- Product Design - Using materials and product components that can be used for different products can reduce waste and inventory. If demands for items using that type of material suddenly decreases, the materials can still be used to make other products.
- Pull-Based Demand - Having a pull-based demand system allows you to reduce inventory levels by only producing items when there is a demand for them. This allows the company to only produce what has been ordered and eliminate the need to store excess inventory.
These strategies can not only optimize your manufacturing operation, but will also increase the amount of revenue the operation is generating by reducing overall inventory cost.
Advanced Planning and Scheduling for Inventory Reduction in the Manufacturing Industry
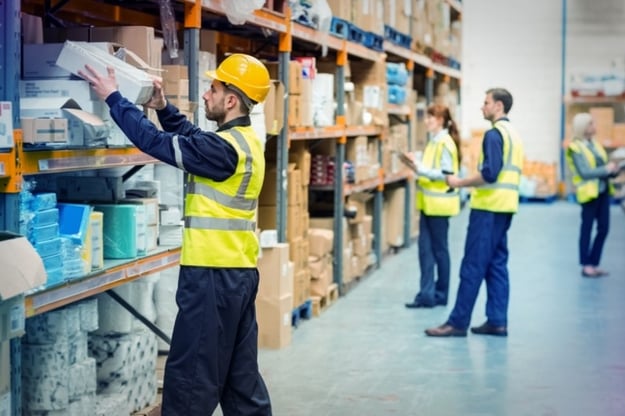
An essential component of advanced planning and scheduling (APS) systems involves inventory planning. Capabilities such as simultaneous capacity and inventory planning, cross-plant optimization, and in-memory planning can benefit your manufacturing operation tremendously.
An advanced planning and scheduling system can help with inventory reduction through:
- Optimized Capacity Plans - Know forecast load-versus-capacity including equipment, tooling, and labor constraints. Optimize automatically to maximize the KPIs of interest for your organization.
- What-If Scenarios - These types of scenarios allow you to evaluate your abilities to meet variable forecasts. You can simulate evolving or adding equipment and employee skill extensions to determine whether you will be able to meet increases in demands.
- Enterprise Capacity Visibility - See workload and capacity at any level: company-wide, plant-by-plant, departmental, or even down to the resource. Various reports can identify which items are taking most of the critical resources times.
- Just-In-Time Scheduling - One of the most well-known strategies for reducing inventory is to use a Just-In-Time strategy for production. An APS system allows you to easily schedule operations so that jobs will be completed just when they should to ship out. This reduces the number of WIP items and finished goods that need to be stored.
The shift to PlanetTogether is saving us about 15 percent in inventory overhead and about 20 percent in overtime labor expenses. We’re not building equipment to stock any longer—we’re building to ship.
BRUCE HAYS, DIRECTOR OF MANUFACTURING, J&J SYNTHES
Integration of an advanced planning and scheduling system such as PlanetTogether to your ERP system allows your production facility to be able to meet its full potential by optimizing your production schedule, increasing scheduling efficiency, and improving data accuracy. You will be able to carry lower levels of inventory and avoid carrying obsolete stock while being able to meet your customer demands.
Advanced Planning and Scheduling (APS) Software
Advanced Planning and Scheduling Softwares have become a must for modern-day manufacturing operations as customer demand for increased product assortment, fast delivery, and downward cost pressures become prevalent. These systems help planners save time while providing greater agility in updating ever-changing priorities, production schedules, and inventory plans. APS Systems can be quickly integrated with an ERP/MRP software to fill the gaps where these systems lack planning and scheduling flexibility, accuracy, and efficiency.
With PlanetTogether you can:
- Create optimized schedules that balance production efficiency and delivery performance
- Maximize throughput on bottleneck resources to increase revenue
- Synchronize supply with demand to reduce inventories
- Provide company-wide visibility to resource capacity
- Enable scenario data-driven decision making
The implementation of an Advanced Planning and Scheduling (APS) Software will take your manufacturing operations to the next level of production efficiency by taking advantage of the operational data you already possess in your ERP system. APS is a step in the right direction of efficiency and lean manufacturing production enhancement. Try out a free trial or demo!
Related Lead-time Reduction Video
APS Resources