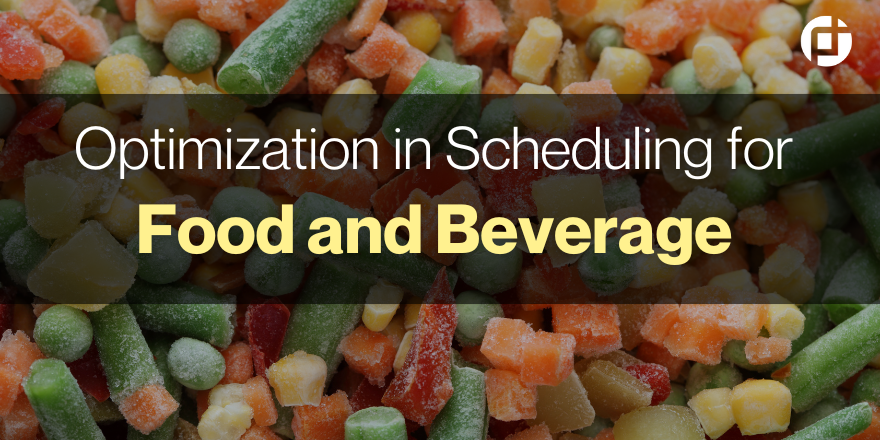
In the world of food and beverage manufacturing, operations directors face a myriad of challenges. From ensuring product quality and safety to meeting fluctuating consumer demands, the need for efficient and agile production processes has never been greater. At the heart of these processes lies scheduling – the art of orchestrating resources, tasks, and timelines to maximize efficiency while minimizing costs.
Scheduling in Food and Beverage
However, traditional scheduling approaches often fall short in addressing the complexities of modern manufacturing environments. This is where multi-objective optimization comes into play, offering a holistic approach to scheduling that considers various objectives simultaneously.
In this blog, we'll explore the concept of multi-objective optimization in scheduling and its integration with leading ERP, SCM, and MES systems such as SAP, Oracle, Microsoft, Kinaxis, and Aveva, with a particular focus on the integration with PlanetTogether.
Understanding Multi-Objective Optimization
Multi-objective optimization is a methodology aimed at finding the best solutions when there are multiple conflicting objectives to consider. In the context of scheduling, these objectives could include maximizing throughput, minimizing production lead times, reducing inventory levels, and optimizing resource utilization, among others.
Unlike traditional single-objective optimization, which focuses on optimizing one criterion at the expense of others, multi-objective optimization seeks to balance these competing objectives to achieve a set of Pareto-optimal solutions.
The Challenge of Traditional Scheduling
Traditional scheduling approaches often rely on heuristic algorithms or manual intervention, which can lead to suboptimal results and inefficiencies. For instance, fixed schedules may fail to adapt to unforeseen disruptions or changes in demand, resulting in underutilized resources or missed deadlines. Moreover, these approaches typically overlook the interdependencies between different production processes, leading to bottlenecks and inefficiencies across the supply chain.
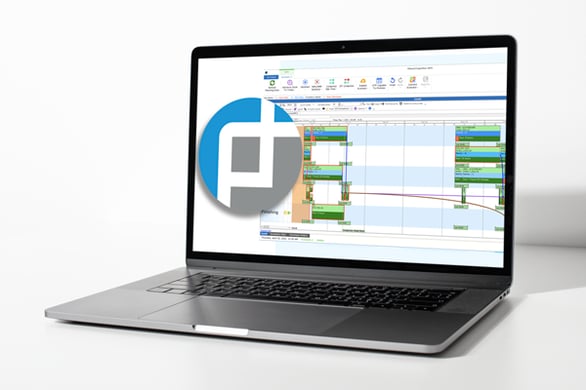
Integrating PlanetTogether with ERP, SCM, and MES Systems
To address these challenges, many food and beverage manufacturers are turning to advanced scheduling solutions like PlanetTogether, which offer powerful multi-objective optimization capabilities. By integrating with leading ERP, SCM, and MES systems such as SAP, Oracle, Microsoft, Kinaxis, and Aveva, PlanetTogether enables seamless data exchange and real-time synchronization across the entire manufacturing ecosystem.
Benefits of Multi-Objective Optimization
The adoption of multi-objective optimization in scheduling offers several key benefits for food and beverage manufacturers:
Improved Efficiency: By considering multiple objectives simultaneously, multi-objective optimization helps identify scheduling solutions that maximize overall efficiency and productivity. This may involve optimizing production sequences, balancing workloads across resources, and minimizing changeover times to reduce idle time and improve throughput.
Enhanced Agility: In today's dynamic marketplace, the ability to respond quickly to changes in demand or supply chain disruptions is crucial. Multi-objective optimization enables manufacturers to generate flexible schedules that can adapt to evolving conditions in real-time, allowing them to maintain high levels of responsiveness and agility.
Better Resource Utilization: By optimizing resource allocation based on multiple criteria, such as machine capacity, labor availability, and material constraints, multi-objective optimization helps maximize the utilization of valuable resources. This not only improves overall efficiency but also reduces operational costs and enhances profitability.
Increased Customer Satisfaction: Ultimately, the goal of efficient scheduling is to deliver high-quality products to customers on time and in full. By optimizing production schedules to meet customer demand while minimizing lead times and inventory levels, manufacturers can enhance customer satisfaction and loyalty, driving long-term business success.
Multi-objective optimization offers a powerful approach to scheduling that addresses the complexities and challenges faced by food and beverage manufacturers. By integrating advanced scheduling solutions like PlanetTogether with leading ERP, SCM, and MES systems, organizations can unlock new levels of efficiency, agility, and competitiveness in today's rapidly evolving marketplace.
As operations directors, embracing multi-objective optimization can empower you to drive innovation, improve decision-making, and achieve sustainable growth in your manufacturing operations.