Agile Scheduling Environments
Supply Chain Managers face the continuous challenge of optimizing production processes to meet the dynamic demands of the Pharmaceutical industry. The key to overcoming these challenges lies in adopting agile scheduling environments that enhance efficiency, reduce costs, and ensure the seamless integration of critical systems.
This blog will explore the concept of agile scheduling and its vital role in pharmaceutical manufacturing facilities, with a specific focus on the integration between PlanetTogether and leading ERP, SCM, and MES systems such as SAP, Oracle, Microsoft, Kinaxis, Aveva, and others.

What is Agile Scheduling?
Agile scheduling is a proactive approach that allows pharmaceutical manufacturing facilities to adapt quickly to changes in demand, supply, and production constraints. Unlike traditional scheduling methods, agile scheduling embraces flexibility, real-time data analysis, and collaboration across various departments.
Supply Chain Managers need to recognize the importance of agile scheduling in the context of pharmaceutical manufacturing, where precision and responsiveness are critical.

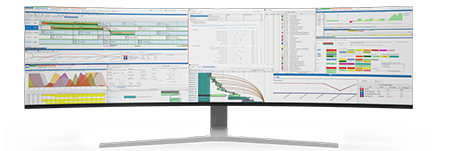
Integration with PlanetTogether
PlanetTogether, a leading advanced planning and scheduling (APS) software, plays a pivotal role in achieving agile scheduling environments. Its powerful features include capacity planning, scenario modeling, and real-time visibility into production processes.
To maximize the benefits of PlanetTogether, seamless integration with ERP, SCM, and MES systems is essential. Let's delve into how integration with key systems enhances agility in pharmaceutical manufacturing.
SAP Integration
SAP, a widely used ERP system, can be seamlessly integrated with PlanetTogether to create a unified platform for data exchange. This integration ensures that information flows seamlessly between production scheduling and resource planning, allowing Supply Chain Managers to make informed decisions based on real-time data. The result is a more agile and responsive production environment.
Oracle Integration
Integrating PlanetTogether with Oracle brings together robust planning capabilities and comprehensive supply chain management. This integration streamlines the flow of information from demand forecasting to production scheduling, enabling Supply Chain Managers to optimize resources efficiently. Real-time synchronization between Oracle and PlanetTogether ensures that changes are instantly reflected throughout the system.
Microsoft Integration
The integration of PlanetTogether with Microsoft's ecosystem enhances collaboration and communication within the organization. Microsoft Dynamics integration, for example, facilitates the exchange of data between production schedules and financial planning, providing Supply Chain Managers with a holistic view of the impact of scheduling decisions on the bottom line.
Kinaxis Integration
Kinaxis, a leader in concurrent planning solutions, can be integrated with PlanetTogether to achieve end-to-end visibility across the supply chain. This integration enables Supply Chain Managers to identify potential disruptions early on and simulate various scenarios to devise agile responses. The synergy between Kinaxis and PlanetTogether ensures adaptability in the face of uncertainties.
Aveva Integration
For pharmaceutical manufacturing facilities relying on Aveva MES (Manufacturing Execution System), integration with PlanetTogether ensures a seamless connection between production scheduling and execution. This integration optimizes the utilization of resources, minimizes downtime, and enhances overall operational efficiency.
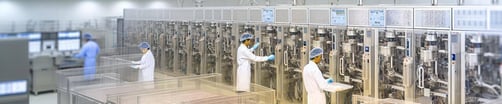
Unlocking the Full Potential
The integration of PlanetTogether with ERP, SCM, and MES systems is just the beginning of creating an agile scheduling environment. To unlock the full potential of agile scheduling, Supply Chain Managers must focus on the following key aspects:
Real-time Collaboration: Foster collaboration among different departments by ensuring real-time access to scheduling data. This collaboration is crucial for adapting quickly to changes and optimizing production processes.
Continuous Monitoring: Implement tools and dashboards that provide continuous monitoring of key performance indicators (KPIs). This allows Supply Chain Managers to identify bottlenecks, inefficiencies, and opportunities for improvement.
Scenario Planning: Leverage the scenario modeling capabilities of integrated systems to simulate various production scenarios. This proactive approach helps in devising contingency plans and responding swiftly to unforeseen events.
Data-driven Decision Making: Encourage a culture of data-driven decision-making by providing teams with accurate and up-to-date information. Integrated systems ensure that decisions are based on real-time data, enhancing overall operational effectiveness.
The adoption of agile scheduling environments in pharmaceutical manufacturing is a strategic imperative for Supply Chain Managers. The integration of advanced planning and scheduling solutions like PlanetTogether with leading ERP, SCM, and MES systems amplifies the benefits of agility.
By embracing flexibility, real-time collaboration, and data-driven decision-making, pharmaceutical manufacturing facilities can navigate the complexities of the industry and ensure sustained success in an ever-changing landscape.