In the manufacturing industry, peak season brings about challenges that can be costly for companies if they are not able to overcome them. In 2020, the coronavirus global pandemic has brought additional challenges to the peak production season.
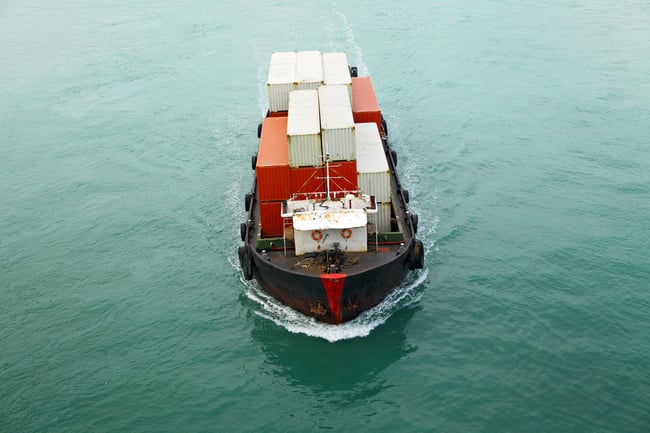
During peak season, the demand for goods is at a yearly high. This means that production facilities must increase their productivity to meet customer demands and deliver products on time. This season can be particularly stressful for manufacturers as they are trying to meet the increasingly high expectations of customers that require a wide variety of products, extremely rapidly, for the lowest cost.
Peak Season Challenges
1. Physical Distancing
With new rules and regulations surrounding the COVID-19 pandemic, many manufacturers have had to reduce the number of staff present on the shop floor to comply with new physical distancing rules. However, as peak season approaches, production facilities need to find a way to increase productivity while keeping their workers safe. This can mean adding more shifts on weekends or evenings to increase capacity. Alternatively, the use of shields between employees could allow for more people to be present on the shop floor for production while keeping everyone safe.
2. Unexpected Outages
2020 has proven time and time again that things don't always go according to plan. This is why having a contingency plan to handle unexpected outages can be extremely helpful for your company. An advanced planning and scheduling software that supports 'what-if' scenario analysis will allow you to prepare for the unexpected. You will be able to model machines breaking down for hours or even days to figure out ahead of time what the best possible solution is. This could mean adding extra capacity on weekends or transferring jobs to other departments. Knowing what the best solution is will save you time and money in the event of an unexpected outage. Even if they are never implemented, contingency plans are a wise investment as it will reduce stress levels and prevent large losses in the event of an outage.
3. Increased Shipping Demands
The demand for freight capacity is at a high during peak season. The global pandemic has shifted the way people buy and prepare for the holiday season. Now more than ever before, consumers are turning to online shopping to buy gifts for the holidays. This means that there will be an even greater strain on shipping demands to get everything delivered on time. It is imperative that companies deliver their products on time as late deliveries can negatively impact the customer's perception of the company, leading to lost sales in the future. Collaborating with multiple companies to increase visibility and take advantage of all available shipping capacity will increase profitability and ensure prompt delivery of your products.
4. Limited Warehouse Space
As available production capacity decreases during peak season, so it the available warehouse capacity. This means that your facility is not able to start producing high amounts of products before they start shipping out as you will quickly run out of space within your warehouse. In addition, you may also not have the required capacity to store the required materials for all customer orders. Having an integrated planning and scheduling software can help mitigate this problem by automatically planning and scheduling materials and capacity as orders come in. This will allow you to know how much material will be used o supply jobs as well as when to purchase more.
An Advanced Planning and Scheduling software can be tremendously helpful for your company to rise above the challenges of peak season. These softwares will allow you to have the visibility you need to quickly identify possible bottlenecks before they occur and plan for various scenarios and plan for possible disruptions before they occur.
Advanced Planning and Scheduling (APS) Software
Advanced Planning and Scheduling Softwares have become a must for modern-day manufacturing operations as customer demand for increased product assortment, fast delivery, and downward cost pressures become prevalent. These systems help planners save time while providing greater agility in updating ever-changing priorities, production schedules, and inventory plans. APS Systems can be quickly integrated with an ERP/MRP software to fill the gaps where these systems lack planning and scheduling flexibility, accuracy, and efficiency.
With APS you can:
- Create optimized schedules that balance production efficiency and delivery performance
- Maximize throughput on bottleneck resources to increase revenue
- Synchronize supply with demand to reduce inventories
- Provide company-wide visibility to resource capacity
- Enable scenario data-driven decision making
The implementation of an Advanced Planning and Scheduling (APS) Software will take your manufacturing operations to the next level of production efficiency by taking advantage of the operational data you already possess in your ERP system. APS is a step in the right direction of efficiency and lean manufacturing production enhancement. Try out a free trial or demo!
Related Capacity Planning Video
APS Resources