Production Planning for Carbon-Neutral Manufacturing
In an era marked by growing environmental consciousness and the urgency to combat climate change, the manufacturing industry has been under increasing pressure to reduce its carbon footprint. For chemical manufacturing facilities, which are notorious for their energy-intensive processes and emissions, achieving carbon neutrality is a formidable challenge. However, it's also a compelling necessity.
In this blog, we will explore how Manufacturing IT plays a pivotal role in achieving carbon-neutral manufacturing, with a particular focus on the integration between PlanetTogether and leading ERP, SCM, and MES systems such as SAP, Oracle, Microsoft, Kinaxis, and Aveva.
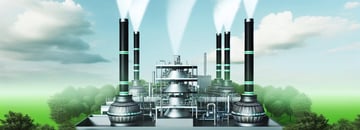
The Imperative of Carbon-Neutral Manufacturing
Carbon neutrality, also known as net-zero emissions, refers to the state in which a manufacturing facility or organization balances the amount of greenhouse gases (GHGs) it emits with an equivalent amount of GHGs removed from the atmosphere or offset through various means. Achieving carbon neutrality is a critical step towards mitigating the effects of climate change and reducing the environmental impact of industrial operations. For chemical manufacturers, it entails reimagining their production processes and embracing sustainable practices.

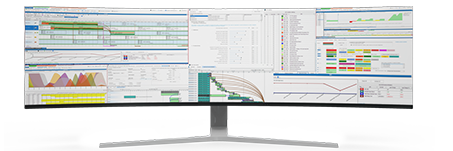
The Role of Production Planning
Effective production planning is the cornerstone of any manufacturing operation, and it becomes even more crucial when transitioning towards carbon-neutral manufacturing. It involves optimizing the allocation of resources, scheduling production runs, and managing inventory to meet customer demand while minimizing waste and emissions. Here's how Manufacturing IT, along with advanced planning and scheduling (APS) solutions like PlanetTogether, can contribute to carbon-neutral manufacturing:
Data Integration and Visibility
To make informed decisions about reducing emissions, manufacturers need real-time visibility into their operations. This is where ERP systems like SAP, Oracle, and Microsoft Dynamics come into play. These systems provide a centralized platform for collecting and managing data related to production, inventory, and supply chain. When integrated with PlanetTogether, this data can be utilized for more accurate production planning.
By syncing with ERP systems, PlanetTogether can access critical information, including raw material availability, production schedules, and customer orders. This integration ensures that production plans align with the overall business strategy, taking into account sustainability goals and carbon reduction targets.
Demand Forecasting and Lean Operations
Carbon-neutral manufacturing often involves adopting lean principles, which aim to minimize waste, including energy waste, in all aspects of production. MES systems like Aveva help monitor and control manufacturing operations in real-time. They enable manufacturers to react swiftly to changing conditions, reducing energy consumption and emissions in the process.
PlanetTogether's advanced forecasting capabilities, when integrated with MES systems, allow chemical manufacturers to accurately predict customer demand and adjust production schedules accordingly. This minimizes overproduction, reduces energy usage, and contributes to a lower carbon footprint.
Supply Chain Optimization
A sustainable supply chain is a key component of carbon-neutral manufacturing. SCM systems like Kinaxis facilitate end-to-end supply chain visibility and optimization. When integrated with PlanetTogether, these systems enable manufacturers to make environmentally conscious decisions when sourcing raw materials and selecting suppliers.
Moreover, the integration ensures that production plans consider the environmental impact of transportation and logistics. It can optimize routes, minimize transportation emissions, and reduce the overall carbon footprint of the supply chain.
Resource Allocation and Energy Efficiency
Carbon-neutral manufacturing requires a careful allocation of resources, including energy. ERP systems are instrumental in tracking energy consumption and costs. By integrating with PlanetTogether, manufacturers can optimize production schedules to make the most efficient use of energy resources.
Additionally, Manufacturing IT can implement IoT (Internet of Things) sensors and smart devices on the shop floor to monitor equipment performance and energy usage. This real-time data can be fed into APS systems like PlanetTogether, allowing for dynamic adjustments in production to minimize energy waste and emissions.
Overcoming Challenges
While the integration of PlanetTogether with ERP, SCM, and MES systems offers tremendous potential for carbon-neutral manufacturing in chemical facilities, there are challenges to overcome:
Data Quality and Compatibility
Ensuring that data from various systems is accurate, up-to-date, and compatible can be a significant hurdle. Manufacturers must invest in data governance practices and standardization efforts to make integration seamless.
Change Management
Implementing new IT solutions and processes can face resistance from employees. Proper change management strategies are essential to ensure that the workforce embraces sustainability initiatives and new technologies.
Cost Considerations
Integrating and upgrading IT systems can be costly. However, the long-term benefits, including reduced operational costs and a positive environmental impact, often outweigh the initial investment.
Production planning for carbon-neutral manufacturing in chemical facilities is no longer an option but a necessity in today's environmentally conscious world. Manufacturing IT, when coupled with advanced planning and scheduling solutions like PlanetTogether and integrated with ERP, SCM, and MES systems, plays a pivotal role in achieving this ambitious goal.
By optimizing data integration, demand forecasting, supply chain operations, and resource allocation, chemical manufacturers can reduce their carbon footprint, minimize waste, and contribute to a sustainable future. While challenges exist, the benefits of carbon-neutral manufacturing extend beyond environmental stewardship to include operational efficiency and competitiveness in an increasingly eco-conscious market.
As chemical facilities continue to evolve towards sustainability, the synergy between Manufacturing IT and advanced planning tools will be instrumental in realizing the vision of carbon-neutral manufacturing. The journey may be challenging, but the destination is worth every effort, as it leads towards a cleaner, greener, and more sustainable future for all.