PRODUCTION PLANNING FOR SUSTAINABLE CHEMICAL MANUFACTURING
In the landscape of the chemical manufacturing industry, the quest for sustainability has become a paramount goal. Manufacturers are not only focused on optimizing production processes but also on minimizing environmental impact. One crucial aspect of achieving sustainable chemical manufacturing is efficient production planning.
In this blog, we will explore the significance of production planning in the chemical manufacturing sector and how integrating advanced planning tools like PlanetTogether with leading ERP, SCM, and MES systems can pave the way for a more sustainable future.
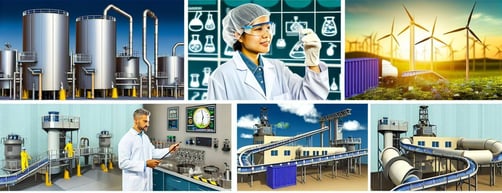
The Imperative of Sustainable Chemical Manufacturing
Chemical manufacturing processes are inherently complex, involving intricate supply chains, varied raw materials, and stringent regulatory requirements. Achieving sustainability in this sector requires a holistic approach that addresses resource efficiency, waste reduction, and energy conservation. Sustainable chemical manufacturing aims to strike a balance between economic viability, environmental responsibility, and social considerations.
Challenges in Production Planning for Chemical Manufacturing
Effective production planning is at the core of sustainable chemical manufacturing. However, the industry faces several challenges that hinder optimal planning and execution:
Batch Processing Complexity: Chemical production often involves batch processing, making planning intricate due to variable production times, material characteristics, and quality specifications.
Supply Chain Variability: Chemical manufacturers depend on a diverse network of suppliers, and fluctuations in the supply chain can lead to production disruptions.
Regulatory Compliance: Stringent environmental and safety regulations in the chemical industry add an extra layer of complexity to production planning.
Continuous Improvement: Staying competitive in the chemical manufacturing sector requires a commitment to continuous improvement, necessitating agile and adaptable production planning strategies.

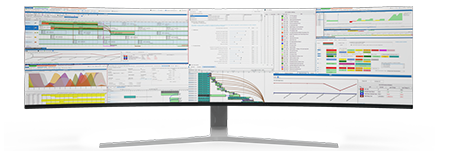
The Role of Advanced Planning Tools in Chemical Manufacturing
To address these challenges, manufacturers are increasingly turning to advanced planning tools. PlanetTogether, a leading advanced planning and scheduling (APS) software, has emerged as a powerful solution for optimizing production processes. It provides real-time visibility, scenario analysis, and the ability to make data-driven decisions. Integrating PlanetTogether with ERP, SCM, and MES systems enhances the overall efficiency of the production planning process.
Integration with ERP Systems
Enterprise Resource Planning (ERP) systems are the backbone of many manufacturing operations, providing a centralized platform for managing various business processes. Integrating PlanetTogether with ERP systems such as SAP, Oracle, and Microsoft Dynamics streamlines data exchange and ensures a seamless flow of information across the organization.
SAP Integration: By linking PlanetTogether with SAP, chemical manufacturers can synchronize production plans with financial data, procurement, and inventory management. This integration enhances decision-making by providing a comprehensive view of the entire manufacturing ecosystem.
Oracle Integration: The integration of PlanetTogether with Oracle ERP facilitates accurate demand forecasting, inventory optimization, and resource allocation. This collaboration ensures that production plans align with business goals and market demand.
Microsoft Dynamics Integration: Integrating PlanetTogether with Microsoft Dynamics enables real-time collaboration, allowing for quick adjustments to production plans based on changing market dynamics. This integration promotes agility in response to customer demands and market trends.
Integration with SCM Systems
Supply Chain Management (SCM) systems play a crucial role in ensuring the efficient flow of materials from suppliers to manufacturers and ultimately to customers. Integrating PlanetTogether with SCM systems enhances supply chain visibility, reduces lead times, and minimizes disruptions.
Kinaxis Integration: The integration of PlanetTogether with Kinaxis RapidResponse enables chemical manufacturers to create agile and responsive supply chains. By connecting production plans with supply chain data, organizations can proactively address potential issues and optimize inventory levels.
Aveva Integration: Combining PlanetTogether with Aveva's SCM solutions allows manufacturers to achieve end-to-end visibility across the supply chain. This integration empowers organizations to synchronize production plans with procurement and logistics, ensuring a smooth and efficient flow of materials.
Integration with MES Systems
Manufacturing Execution Systems (MES) bridge the gap between planning and execution on the shop floor. Integrating PlanetTogether with MES systems enhances real-time monitoring, data collection, and feedback loops, leading to improved production efficiency and quality.
Integration Benefits: By integrating with MES systems, chemical manufacturers can achieve a closed-loop approach to production planning. Real-time data from the shop floor informs the planning process, allowing for dynamic adjustments to schedules based on actual production performance.
Improved Visibility: The integration provides enhanced visibility into key performance indicators (KPIs) such as OEE (Overall Equipment Efficiency), production cycle times, and yield rates. This visibility enables continuous improvement initiatives and drives operational excellence.
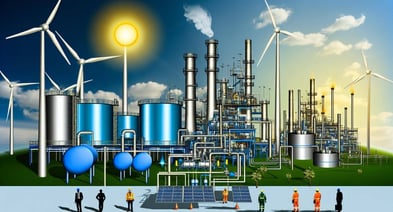
Achieving Sustainable Production with Integration
The integration of advanced planning tools like PlanetTogether with ERP, SCM, and MES systems is not just about improving efficiency; it's a critical step toward achieving sustainability in chemical manufacturing.
Resource Optimization: Integrated planning allows manufacturers to optimize the use of resources, minimizing waste and reducing the environmental impact of production processes.
Energy Efficiency: By synchronizing production plans with real-time data from the shop floor, manufacturers can implement energy-efficient practices, contributing to both cost savings and sustainability goals.
Compliance and Reporting: The seamless flow of data between planning and execution systems ensures accurate reporting and compliance with environmental regulations. This transparency is crucial for maintaining a socially responsible manufacturing operation.
Achieving sustainable chemical manufacturing necessitates a comprehensive approach to production planning. The integration of advanced planning tools like PlanetTogether with leading ERP, SCM, and MES systems is a strategic move towards optimizing processes, minimizing environmental impact, and ensuring long-term business success.
As the industry evolves, manufacturers who embrace these integrated solutions will not only thrive in the competitive landscape but also contribute to a more sustainable future.