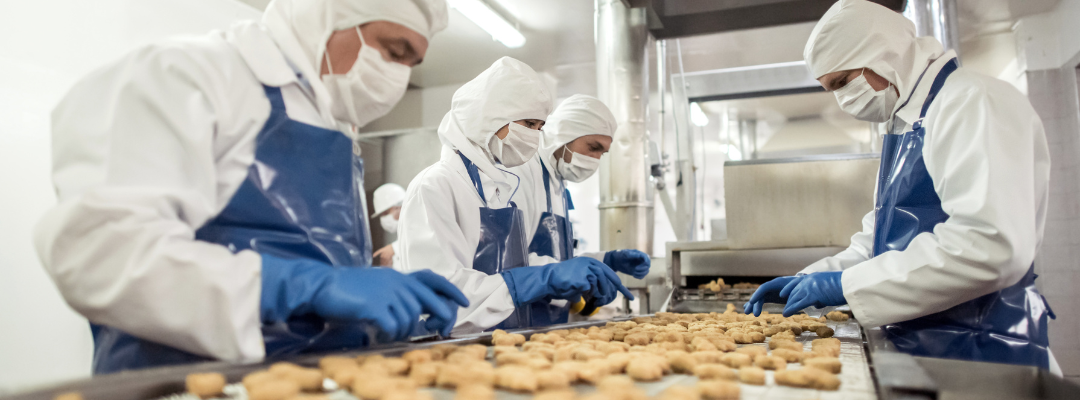
In Food and Beverage (F&B) manufacturing, staying competitive and meeting customer demands while maintaining operational efficiency is a challenging task. As an Operations Director, your responsibilities are paramount to ensuring smooth production processes, timely deliveries, and cost-effective operations. One crucial aspect that can significantly impact these factors is production scheduling.
Traditional production scheduling methods often fall short in today's dynamic manufacturing landscape. However, the integration of advanced technologies like Artificial Intelligence (AI) and Machine Learning (ML) with scheduling systems can revolutionize how F&B manufacturing facilities operate.
In this blog, we will explore the integration of PlanetTogether, an innovative production scheduling software, with leading ERP, SCM, and MES systems such as SAP, Oracle, Microsoft, Kinaxis, Aveva, and others. We will look into the potential benefits, challenges, and best practices for real-time production scheduling using AI and ML.
But First... What Is AI Production Scheduling?
AI-driven production scheduling involves leveraging artificial intelligence (AI) technologies to optimize and automate the process of creating production schedules. The goal is to enhance efficiency, minimize costs, and improve overall operational performance in manufacturing or service delivery.
Understanding the Power of Real-time Production Scheduling
Real-time production scheduling empowers F&B manufacturers to adapt to changes on the fly, optimize resources, minimize waste, and improve overall operational efficiency. By leveraging AI and ML algorithms, production schedules can be dynamically adjusted based on real-time data, market trends, and customer demands, thereby enhancing the decision-making process.
The Role of AI and ML in Production Scheduling
AI and ML technologies enable production scheduling systems to analyze vast amounts of data and historical performance to identify patterns, predict possible disruptions, and make intelligent decisions. The ability to learn from past experiences and adjust schedules accordingly helps avoid bottlenecks, production delays, and stockouts, leading to reduced costs and improved customer satisfaction.
PlanetTogether: A Game-Changer in Production Scheduling
PlanetTogether is a renowned production scheduling software that utilizes AI and ML algorithms to optimize scheduling processes. Its user-friendly interface, scenario simulations, and real-time data integration make it a valuable tool for F&B manufacturers. Now, imagine the added power of integrating PlanetTogether with your existing ERP, SCM, and MES systems.
Advantages of Integration
Seamless Data Exchange: Integrating PlanetTogether with ERP systems like SAP, Oracle, or Microsoft allows for smooth data exchange between production scheduling and other operational processes. This ensures that all departments are working with the same real-time data, leading to improved collaboration and decision-making.
Enhanced Visibility: By integrating PlanetTogether with MES systems, you gain real-time visibility into the shop floor, providing valuable insights into production progress, machine performance, and workforce efficiency. This transparency facilitates quicker responses to any deviations from the schedule.
Supply Chain Optimization: Integrating PlanetTogether with SCM systems like Kinaxis enables you to optimize inventory levels, reduce lead times, and enhance supplier collaboration. This ultimately leads to a more resilient and efficient supply chain.
%20in%20Inventory%20Management.png?width=534&height=356&name=Just-in-Time%20(JIT)%20in%20Inventory%20Management.png)
Addressing Challenges in Integration
Data Security and Privacy: As you integrate different systems, data security and privacy become crucial considerations. Ensure that proper encryption, access controls, and compliance measures are in place to protect sensitive information.
Customization and Adaptability: Each F&B manufacturing facility is unique, and the integration process should be customizable to fit specific needs and requirements. Flexibility and adaptability are key when integrating various systems.
Best Practices for Successful Integration
Define Clear Objectives: Clearly outline the goals and outcomes you want to achieve through integration. Having a well-defined plan will help keep the integration process on track.
Involve Key Stakeholders: Engage all relevant stakeholders, including IT teams, production managers, and department heads, to ensure their buy-in and support throughout the integration journey.
Pilot and Test: Before rolling out the integration on a larger scale, conduct pilot tests to identify potential issues and make necessary adjustments.
Real-time production scheduling using AI and machine learning, integrated with leading ERP, SCM, and MES systems, can be a game-changer for F&B manufacturing facilities. As an Operations Director, harnessing the power of technologies like PlanetTogether in conjunction with other systems can elevate your production scheduling to new heights, leading to increased efficiency, reduced costs, and improved customer satisfaction.
Embrace this digital transformation and position your facility for success in the ever-evolving world of F&B manufacturing.