In every manufacturing facility, there seems to be one problem that seems to be universal, regardless of size, product, or process. That problem is Data Gaps.
The planning and scheduling processes require the coordination of many factors, such as the production orders in the backlog, new orders coming in, the availability of materials, the availability of the machines and labor who will do the work, and the capabilities of the machines able to perform the work.
In manufacturing, data gaps are an ever-present nuisance that just never seems to be resolved. These can be as small as a job that was never marked as completed, or a missing step in a product routing.
In a scheduling system, data gaps can make it difficult to identify why these jobs failed to schedule. With an eye towards identification and prevention of these gaps, PlanetTogether’s Advanced Planning and Scheduling system provides powerful "data forensic" tools that aid in rooting them out.
Why are my jobs not scheduling?
Previously, some jobs would be marked as "Failed to Schedule" in PlanetTogether due to lack of active capable Resources, or constraints that make otherwise capable resources ineligible.
In order to determine why a Job failed to schedule, users would need to access information dispersed over multiple windows, dialogs and grids which could be time consuming, and difficult. This is why we have developed the Eligibility Dialog tool within PlanetTogether, which simplifies this process by gathering all relevant information in one place.
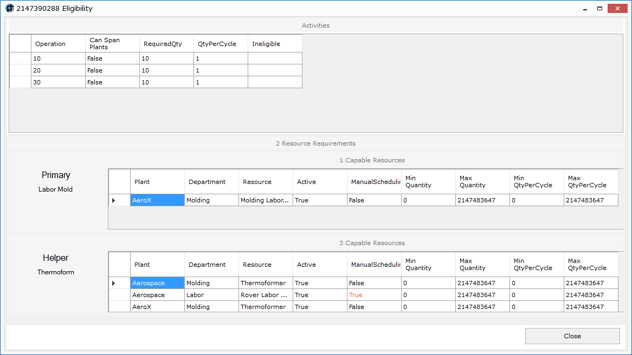
Eligibility Dialog
The Eligibility Dialog displays the resource requirements for each Job Operation with a list of all resources capable of fulfilling those requirements.
All activities within the selected job are listed along with their attributes. When an activity is selected, all resource requirements for the activity will be listed, including a list of capable resources that can satisfy the requirement. The Eligibility Dialog gathers all relevant information for each resource and links to attribute number ranges, allowed helpers, and resource connectors, if applicable.
If a job fails to schedule, the Eligibility Dialog contains a field that indicates which specific activity is causing the issue.
This powerful feature plays a crucial role in identifying gaps in a plant’s routing data. It also decreases the time that would be required to identify the cause of jobs not appearing in the schedule. Now, this information is readily available in one place and accessible with the click of a button.
The great thing about PlanetTogether APS is that all machines can be grouped together on one screen. You know immediately how each machine impacts the other and their basic correlation to the whole schedule, not just for the current week, but for days, weeks, or months out. PlanetTogether keeps us very organized and coordinated.
JAIME OZUNA, PRODUCTION SCHEDULER, ATLANTIC COFFEE
PlanetTogether’s Advanced Planning and Scheduling software is well-suited to handle a variety of complex production environments where resource capacity is constrained or limited and where frequent schedule changes are required.
PlanetTogether Advanced Planning and Scheduling (APS) Software
Advanced Planning and Scheduling Softwares have become a must for modern-day manufacturing operations as customer demand for increased product assortment, fast delivery, and downward cost pressures become prevalent. These systems help planners save time while providing greater agility in updating ever-changing priorities, production schedules, and inventory plans. APS Systems can be quickly integrated with an ERP/MRP software to fill the gaps where these systems lack planning and scheduling flexibility, accuracy, and efficiency.
With PlanetTogether APS you can:
- Create optimized schedules that balance production efficiency and delivery performance
- Maximize throughput on bottleneck resources to increase revenue
- Synchronize supply with demand to reduce inventories
- Provide company-wide visibility to resource capacity
- Enable scenario data-driven decision making
The implementation of an Advanced Planning and Scheduling (APS) Software will take your manufacturing operations to the next level of production efficiency by taking advantage of the operational data you already possess in your ERP system. APS is a step in the right direction of efficiency and lean manufacturing production enhancement. Try out a free trial or demo!
Related Integration Video
APS Resources