Picture this: You've just landed a pivotal order, a true catalyst for growth. Your team is energized, ready to deliver. But then, the inevitable happens. A critical supplier delay throws your raw material delivery into chaos. Your meticulously crafted production schedule unravels, and suddenly, "just in time" transforms into "just too late."
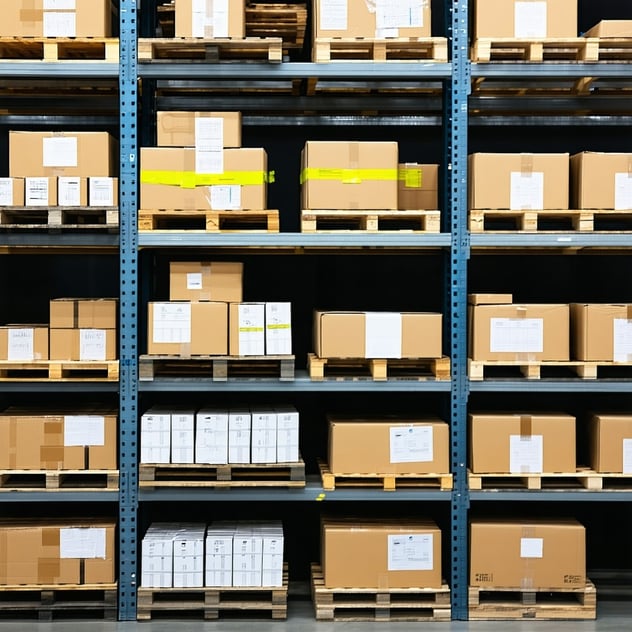
This isn't a hypothetical scenario; it's the stark reality faced by countless manufacturers daily. According to a recent report by Resilinc, 75% of companies experienced supply chain disruptions in the past 12 months, with the average disruption lasting 23 days. This isn't just a minor setback; it's a significant financial blow that can cripple your operations.
Let's break down some specific, real-world examples:
- A food manufacturer relying on a single source for a specialized ingredient faced massive waste when a sudden weather event disrupted the harvest. Compounding the issue, the USDA estimates that food waste in manufacturing can account for up to 10% of total production costs, directly impacting profitability.
- An aerospace parts supplier experienced catastrophic delays due to unexpected machine downtime. Industry data reveals that unplanned downtime can cost manufacturers as much as $50,000 per hour, not to mention the potential for lost contracts and reputational damage.
- A packaging company lost a key client because they couldn't rapidly adapt to a last-minute design change. According to a Salesforce study, 80% of customers say the experience a company provides is as important as its products or services.
The ripple effect is devastating: missed deadlines, escalating costs, and irreparable damage to your reputation. The core problem? Often, it's a lack of end-to-end visibility and the inability to dynamically reschedule. Relying on outdated spreadsheets and gut instinct simply cannot compete with the speed and complexity of modern manufacturing.
Here's a strategic approach to mitigate these risks:
- Implement Multi-Tiered Supplier Relationships: Cultivate relationships with multiple suppliers at various tiers to reduce reliance on single points of failure.
- Invest in IoT-Enabled Predictive Maintenance: Utilize sensor data and advanced analytics to anticipate equipment failures, optimize maintenance schedules, and minimize downtime.
- Enhance Cross-Functional Communication: Foster seamless communication between procurement, production, and logistics teams to ensure real-time information sharing and collaborative decision-making.
- Embrace Advanced Planning and Scheduling (APS) Systems: Deploy an APS system that provides real-time visibility into your operations, enables rapid scenario planning, and optimizes resource allocation.
- Create Digital Twins of your production line: This allows for simulation of changes, and allows you to test changes before they are implemented.
- Focus on data collection: The more data you have on your process, the easier it is to see bottlenecks, and to predict future problems.
Imagine having the ability to:
- Receive proactive alerts about potential supplier delays and equipment failures.
- Instantly reschedule production based on real-time data and dynamic constraints.
- Provide accurate and transparent delivery timelines to your customers, enhancing trust and loyalty.
Are you ready to break free from the late order nightmare and transform your manufacturing operations?
Discover how advanced planning and scheduling solutions can empower you to navigate these real-world challenges with confidence. Book a personalized demo today, and let's explore how you can move from reactive firefighting to proactive, data-driven optimization.
[Call to Action Button: Book Your Demo Now!]
Let's discuss how to stop reacting to problems, predict future challenges, and significantly improve your company's bottom line."
IMTEK, in collaboration with PlanetTogether APS, exemplifies how partnerships drive supply chain transformation. By leveraging APS technology, companies can fine-tune their operations, ensuring every “Buy Now” click results in a smooth and cost-effective fulfillment process.
Every purchase tells a story of logistics, planning, and innovation. If you’re curious about how advanced planning can transform your operations, let’s talk. Request a demo to see the ripple effect of smarter scheduling in action.