Digitalization of Scheduling Processes in Manufacturing
In the landscape of industrial manufacturing, the pursuit of operational excellence has become paramount. As a Supply Chain Manager, you are well aware of the intricate dance involved in orchestrating production schedules, managing resources, and optimizing efficiency. The advent of digital technologies has ushered in a new era, offering innovative solutions to enhance scheduling processes.
In this blog, we explore the digitalization of scheduling processes in manufacturing, with a focus on the integration between PlanetTogether and leading ERP, SCM, and MES systems such as SAP, Oracle, Microsoft, Kinaxis, Aveva, and others.
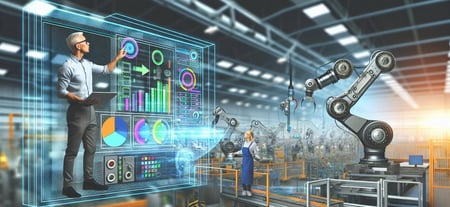
Traditional scheduling processes in manufacturing have often been manual, time-consuming, and prone to errors. Excel spreadsheets and rudimentary software tools have been the go-to solutions, but they fall short in addressing the complexities of modern supply chain dynamics. The need for real-time visibility, adaptive planning, and efficient resource allocation has led to the exploration of digital alternatives.

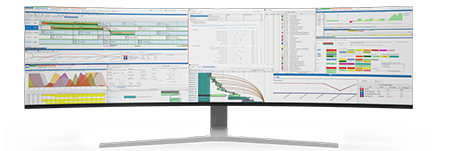
Enter PlanetTogether
PlanetTogether, a cutting-edge Advanced Planning and Scheduling (APS) solution, has emerged as a game-changer in the manufacturing realm. Its ability to create optimized production schedules, consider multiple constraints, and adapt to dynamic changes sets it apart. Now, let's look into the key benefits of integrating PlanetTogether with prominent ERP, SCM, and MES systems.
Integration with SAP
SAP, a global leader in enterprise software, seamlessly integrates with PlanetTogether to provide a comprehensive solution. The real-time data synchronization between SAP and PlanetTogether ensures that production schedules are always aligned with the latest demand forecasts and inventory levels. This integration streamlines the entire supply chain, from order creation to delivery.
Integration with Oracle
Oracle, another heavyweight in the ERP domain, complements PlanetTogether's capabilities by providing a robust platform for data management. The integration facilitates the exchange of information between Oracle's ERP system and PlanetTogether, enabling manufacturers to make data-driven decisions, enhance visibility, and optimize production schedules.
Integration with Microsoft
Microsoft's suite of tools, including Dynamics 365, integrates seamlessly with PlanetTogether, creating a powerful synergy. This integration leverages the capabilities of Microsoft's ERP and CRM solutions to enhance collaboration, streamline communication, and ensure that scheduling decisions align with broader business objectives.
Integration with Kinaxis
Kinaxis, a leader in supply chain planning solutions, collaborates effectively with PlanetTogether to provide end-to-end visibility. The integration enables real-time data exchange, allowing manufacturers to respond swiftly to changes in demand, supply chain disruptions, and production constraints. The result is a more agile and responsive scheduling process.
Integration with Aveva
Aveva, known for its Manufacturing Execution System (MES), integrates with PlanetTogether to bridge the gap between planning and execution. The seamless flow of information between Aveva and PlanetTogether ensures that the production schedule aligns with shop floor realities, minimizing discrepancies and maximizing efficiency.
Other ERP, SCM, and MES Integrations
Beyond the mentioned integrations, PlanetTogether offers compatibility with a wide array of ERP, SCM, and MES systems. This flexibility allows manufacturing facilities to choose the solutions that best suit their unique requirements, fostering a tailored approach to digitalizing scheduling processes.
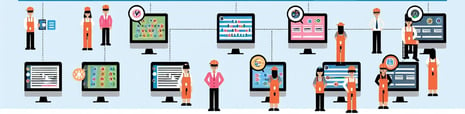
Key Advantages of Digitalized Scheduling Processes
Real-time Visibility: Digitalization provides real-time visibility into production schedules, allowing Supply Chain Managers to make informed decisions based on the latest data.
Optimized Resource Allocation: With the ability to consider multiple constraints and variables, digital scheduling ensures optimal resource allocation, reducing bottlenecks and improving efficiency.
Adaptive Planning: Digital scheduling processes are adaptive, capable of adjusting to changes in demand, supply chain disruptions, and unforeseen events, ensuring resilience in the face of uncertainty.
Enhanced Collaboration: Integration with ERP, SCM, and MES systems fosters seamless collaboration across departments, breaking down silos and improving communication.
Improved Decision-making: Data-driven insights provided by digital scheduling empower Supply Chain Managers to make better-informed decisions, aligning production schedules with overall business objectives.
The digitalization of scheduling processes in manufacturing, coupled with the integration of advanced planning tools like PlanetTogether with leading ERP, SCM, and MES systems, marks a paradigm shift in how industrial facilities approach production planning. As a Supply Chain Manager, embracing this transformation promises increased efficiency, improved agility, and a competitive edge in an ever-evolving industry.
The era of manual scheduling is fading, making way for a future where digitalization reigns supreme, optimizing every facet of the manufacturing process.
Are you ready to take your manufacturing operations to the next level? Contact us today to learn more about how PlanetTogether and integrated scheduling solutions can help you achieve your sustainability goals and drive success in the industrial industry.