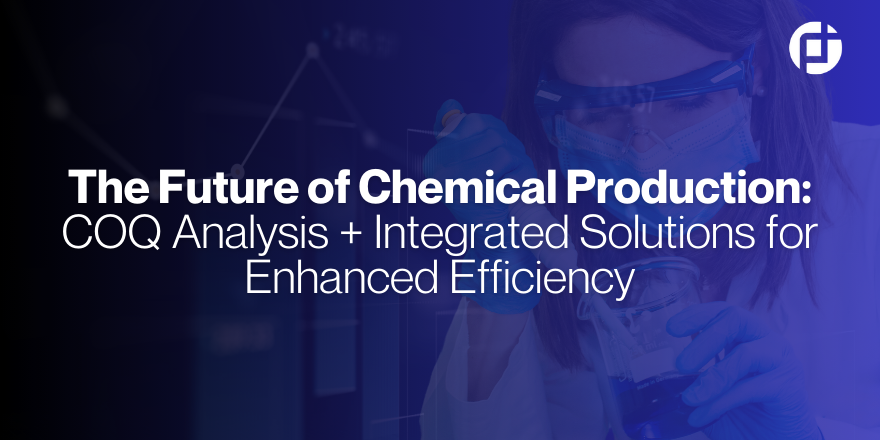
Production Schedulers play a pivotal role in ensuring operational efficiency and productivity. Amidst the myriad challenges they face, understanding the Cost of Quality (COQ) becomes vital. COQ analysis offers invaluable insights into the financial implications of quality-related issues and the potential for optimization.
In this blog, we look into the significance of COQ analysis for Production Schedulers in chemical manufacturing facilities and explore the integration of leading solutions like PlanetTogether with ERP, SCM, and MES systems to streamline operations and enhance profitability.
Understanding the Cost of Quality (COQ)
COQ encompasses the total costs incurred by an organization due to poor quality products or processes. It comprises both the tangible costs, such as rework, scrap, and warranty claims, as well as intangible costs, including customer dissatisfaction and damage to brand reputation. By conducting COQ analysis, manufacturing facilities can identify areas for improvement, prioritize quality initiatives, and ultimately reduce overall costs.
Challenges Faced by Production Schedulers
Production Schedulers encounter numerous challenges in optimizing manufacturing processes while maintaining quality standards. These challenges include:
Balancing Production Efficiency with Quality Assurance: Schedulers must strike a delicate balance between meeting production targets and ensuring adherence to quality standards, often facing conflicting priorities.
Reactive Problem Solving: In many instances, quality issues are addressed reactively, leading to increased costs and production delays.
Lack of Visibility: Limited visibility into the root causes of quality issues makes it difficult for Schedulers to implement effective corrective actions.
Integration Issues: Disparate systems and manual processes hinder seamless communication and data exchange between production scheduling and quality management functions.
The Role of COQ Analysis in Chemical Manufacturing
COQ analysis offers a structured approach to understanding the financial impact of quality-related issues. By categorizing costs into prevention, appraisal, internal failure, and external failure costs, manufacturing facilities can:
Identify Cost Drivers: Pinpointing the primary sources of quality-related costs enables Schedulers to allocate resources more effectively and prioritize improvement initiatives.
Quantify the Financial Impact: By quantifying both tangible and intangible costs, COQ analysis provides a comprehensive view of the true cost of poor quality, empowering decision-makers to justify investments in quality improvement initiatives.
Drive Continuous Improvement: Armed with data-driven insights, organizations can implement proactive measures to prevent quality issues from occurring, thereby reducing overall COQ and enhancing competitiveness.
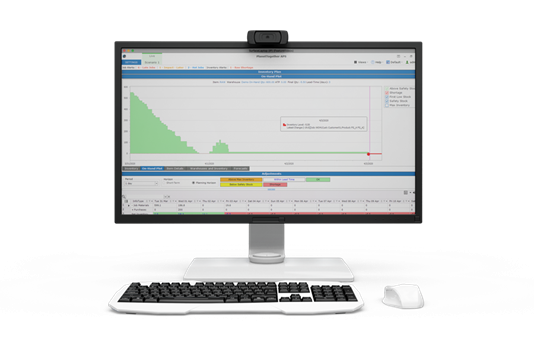
Integration of PlanetTogether with ERP, SCM, and MES Systems
To effectively leverage COQ analysis and optimize manufacturing operations, seamless integration between production scheduling and other enterprise systems is essential. PlanetTogether, a leading production planning and scheduling software, offers robust integration capabilities with various ERP, SCM, and MES systems, including SAP, Oracle, Microsoft Dynamics, Kinaxis, and Aveva.
Benefits of Integration
Real-Time Data Exchange: Integration enables real-time data exchange between production scheduling, inventory management, and quality control systems, facilitating timely decision-making and proactive problem-solving.
Enhanced Visibility: By consolidating data from multiple systems into a unified platform, Schedulers gain holistic visibility into production processes, quality metrics, and resource utilization.
Streamlined Workflows: Automated workflows and seamless communication between systems streamline operations, reduce manual errors, and improve overall efficiency.
Data-Driven Decision Making: Access to accurate, up-to-date information empowers Schedulers to make data-driven decisions, optimize production schedules, and minimize the risk of quality-related issues.
Improved Collaboration: Integration fosters collaboration between cross-functional teams, enabling smoother coordination and alignment of quality objectives with production goals.
In the competitive landscape of chemical manufacturing, understanding and optimizing the Cost of Quality (COQ) is imperative for sustainable growth and profitability. Production Schedulers play a crucial role in driving COQ analysis and leveraging integrated solutions like PlanetTogether with ERP, SCM, and MES systems to streamline operations, enhance quality, and reduce costs.
By embracing a proactive approach to quality management and harnessing the power of data-driven decision-making, chemical manufacturing facilities can achieve operational excellence and maintain a competitive edge in the market.