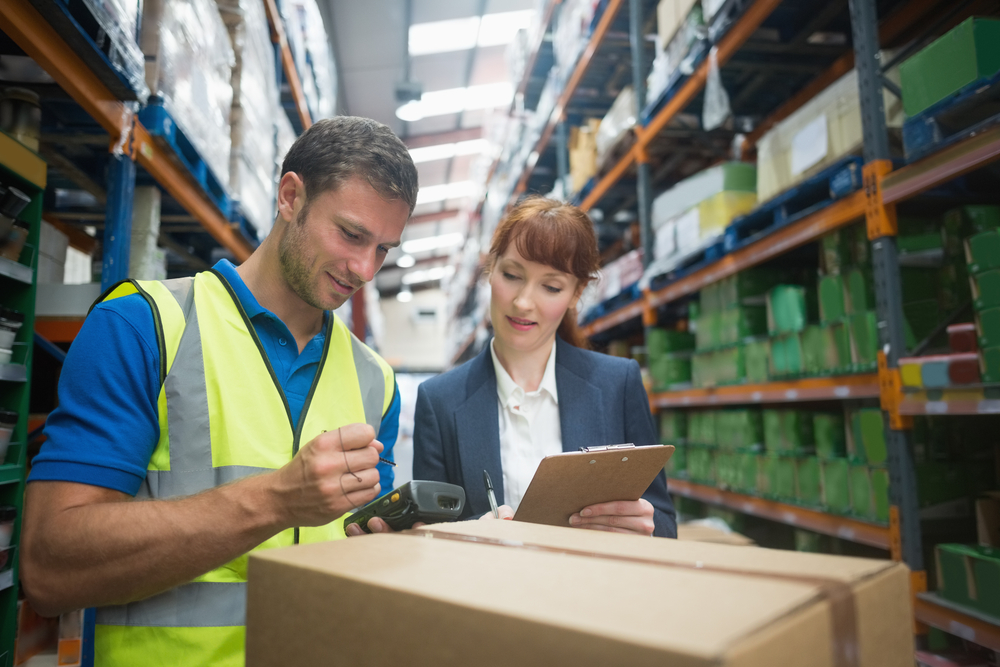
As a supply chain manager in a packaging manufacturing facility, one of the most critical aspects of your job is capacity planning. Capacity planning is the process of determining the production capacity needed by an organization to meet its future demand. It is a critical process that ensures that your organization can meet the demands of your customers without overtaxing your resources or causing delays. This blog will cover the importance of capacity planning, the factors that influence capacity planning, and the steps involved in the capacity planning process.
Why is Capacity Planning Important?
Capacity planning is essential for several reasons. First, it ensures that your organization can meet the demand for your products or services without causing delays or shortages. Capacity planning allows you to ensure that you have the necessary resources, including people, equipment, and materials, to meet your customers' needs.
Second, capacity planning helps you to optimize your resources. By determining the optimal capacity levels, you can avoid overtaxing your resources, which can lead to inefficiencies and higher costs. You can also avoid underutilizing your resources, which can lead to missed opportunities and lower profits.
Finally, capacity planning can help you to identify potential bottlenecks in your production process. By analyzing your capacity levels, you can identify areas where production may be slowed down or delayed, allowing you to take action to mitigate these risks.
Factors that Influence Capacity Planning
Several factors influence capacity planning, including the following:
Demand: The level of demand for your products or services is one of the most critical factors that influence capacity planning. If demand is high, you will need to increase your production capacity to meet this demand.
Lead Time: The lead time required to produce your products or services is another critical factor that influences capacity planning. If the lead time is long, you will need to have a higher capacity to ensure that you can meet demand.
Equipment: The type and amount of equipment needed to produce your products or services are also essential factors that influence capacity planning. If you have more equipment, you can produce more products or services in less time, increasing your capacity.
Labor: The number of employees needed to produce your products or services is another critical factor that influences capacity planning. If you have more employees, you can produce more products or services in less time, increasing your capacity.
Steps in the Capacity Planning Process
The capacity planning process involves several steps, including the following:
Forecast Demand: The first step in the capacity planning process is to forecast demand. You will need to determine the level of demand for your products or services over the planning horizon.
Determine Capacity Requirements: Once you have forecasted demand, the next step is to determine your capacity requirements. You will need to determine the production capacity needed to meet the forecasted demand.
Identify Constraints: After determining your capacity requirements, you will need to identify any constraints that may limit your ability to meet these requirements. Constraints may include equipment, labor, materials, or other resources.
Develop a Plan: Based on your capacity requirements and constraints, you can develop a capacity plan. This plan should include the optimal levels of production capacity needed to meet demand while avoiding overtaxing or underutilizing your resources.
Monitor and Adjust: The final step in the capacity planning process is to monitor your capacity levels and adjust your plan as necessary. You should regularly review your capacity levels and adjust your plan to ensure that you are meeting your production targets and optimizing your resources.
Capacity planning is a critical process for any organization, and it is especially important for packaging manufacturing facilities. By effectively planning your production capacity, you can ensure that you are meeting the demand for your products or services while optimizing your resources and avoiding delays or shortages. To effectively plan your capacity, you need to consider several factors.