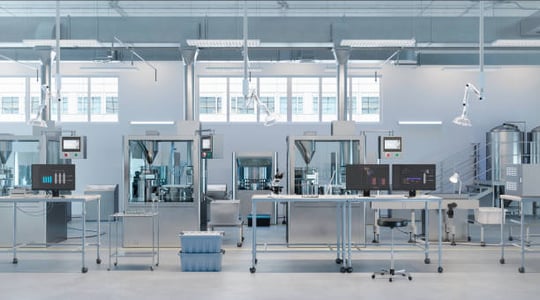
Automating Complex Manufacturing Workflows through APS and ERP Synergy
In today’s competitive and regulation-heavy medical manufacturing landscape, Manufacturing IT leaders face immense pressure to optimize production workflows, ensure compliance, and increase responsiveness — all without compromising on quality. The growing complexity of manufacturing processes, fueled by product personalization, intricate supply chains, and stringent regulatory oversight, makes it clear: manual coordination and outdated scheduling methods no longer suffice.
Enter the powerful combination of Advanced Planning and Scheduling (APS) systems like PlanetTogether and enterprise resource planning (ERP) platforms such as SAP, Oracle, Microsoft Dynamics, Kinaxis, or Aveva. Together, these systems enable a transformative synergy that automates complex manufacturing workflows, streamlines operations, and improves both agility and profitability.
Let’s explore how this integration works, what it means for medical manufacturers, and why Manufacturing IT leaders should be leading the charge.
The Challenges of Complex Medical Manufacturing
Medical manufacturing is unlike most other industrial sectors. Not only does it involve precision-driven, high-stakes products (from surgical devices to implantable components), but it also requires strict adherence to regulatory bodies such as the FDA, EMA, and ISO standards. On top of that, companies must navigate:
Short product life cycles due to fast-evolving medical technology.
Highly customized production runs for niche therapies or patient-specific devices.
Multistage processes that combine automated machinery, manual intervention, and outsourced suppliers.
Stringent documentation and traceability demands for every lot, batch, and unit.
Global supply chains increasingly subject to volatility, delays, or geopolitical risk.
For Manufacturing IT teams, managing these complexities through standalone systems creates silos, manual handoffs, and gaps in real-time visibility. It also increases the likelihood of errors, delays, or compliance risks.
This is where APS and ERP integration comes in.
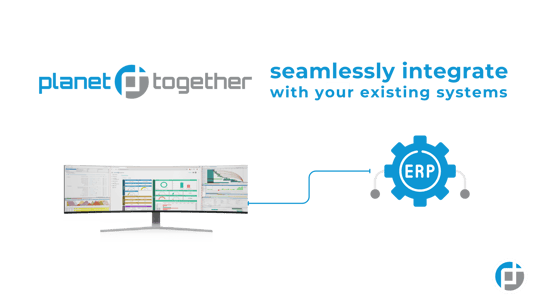
What Happens When APS and ERP Work Together?
An ERP system (like SAP, Oracle, Microsoft, Kinaxis, or Aveva) acts as the central nervous system of a manufacturing organization, handling master data, procurement, inventory, finance, and order management. But ERP systems often lack the specialized scheduling and optimization capabilities needed on the shop floor.
That’s where an APS solution like PlanetTogether fits in. APS platforms:
Analyze real-time production constraints (machines, labor, materials).
Optimize production schedules dynamically.
Rebalance priorities automatically when disruptions hit.
Simulate “what-if” scenarios to guide better decision-making.
Synchronize multiple production lines, plants, and outsourced operations.
When ERP and APS are integrated, they create a feedback loop where:
The ERP feeds the APS real-time data about orders, inventory, procurement, and resource availability.
The APS returns optimized production plans, capacity forecasts, and execution schedules back to the ERP.
Both systems update in parallel, reducing manual data entry, aligning operations with business goals, and accelerating response to changes.
This is the difference between reactive, siloed management and proactive, fully automated workflows.
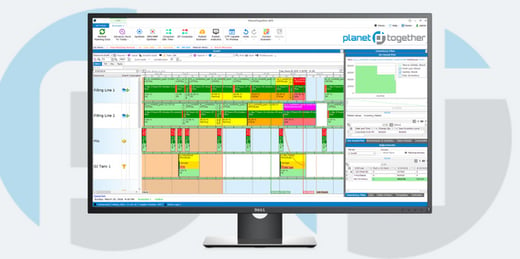
How Integration Automates Complex Workflows
For Manufacturing IT teams, the value of integrating PlanetTogether APS with an ERP platform is not just about plugging two systems together — it’s about orchestrating the end-to-end workflow. Here’s how automation plays out across key stages:
Automated Order-to-Production Flow
When a customer or internal order enters the ERP system, it instantly flows into the APS environment. There’s no need for manual handoffs or offline schedule creation — the APS system can automatically analyze:
Required materials and whether they’re in stock.
Available capacity across multiple lines or facilities.
Regulatory requirements tied to the product, batch, or market.
The result? Instant, optimized production schedules that align with delivery dates, quality checks, and cost goals.
Dynamic Rescheduling Based on Real-Time Disruptions
Medical manufacturing is vulnerable to unexpected disruptions — machine breakdowns, late supplier deliveries, sudden shifts in demand, or quality issues.
In an integrated APS-ERP environment, PlanetTogether’s dynamic rescheduling tools can automatically adjust production schedules in response to real-time data fed from the ERP. For example, if a key raw material shipment is delayed, the APS system can reprioritize other orders, shift resources, or trigger contingency plans — all without manual intervention.
Streamlined Multi-Stage and Multi-Plant Coordination
Many medical manufacturers operate across multiple sites or outsource critical stages to contract manufacturers (CMOs). Coordinating production across these ecosystems requires seamless visibility.
An integrated APS-ERP setup enables Manufacturing IT teams to synchronize:
Master production schedules across plants.
Shared resources like tooling or specialized personnel.
Transportation and logistics planning aligned with production outputs.
This multi-site coordination reduces bottlenecks, balances workloads, and improves on-time delivery.
Automated Compliance and Traceability
Medical manufacturers must track every material, process step, and final product for regulatory compliance.
With APS-ERP integration, traceability is automated:
Lot and batch tracking data from the ERP is aligned with production events in the APS.
Quality control checkpoints are embedded in the schedule, not added afterward.
Audit-ready documentation is automatically generated, reducing the IT burden of compliance reporting.
This automation significantly reduces the risk of non-compliance or costly manual tracking.
Why Manufacturing IT Leaders Should Lead Integration Efforts
Manufacturing IT leaders sit at the intersection of operations, business strategy, and technology. They are uniquely positioned to drive the digital transformation that APS and ERP integration enables. Here’s why IT leadership matters:
Integration expertise — IT understands the data models, APIs, and workflows needed to connect systems without creating new silos.
Change management — IT teams can coordinate cross-departmental efforts to ensure adoption, training, and continuous improvement.
Data governance — IT leaders ensure that the data flowing between systems remains clean, consistent, and secure.
Innovation roadmap — By championing APS-ERP synergy, IT can open the door to future innovations such as AI-driven optimization, predictive analytics, and digital twin simulations.
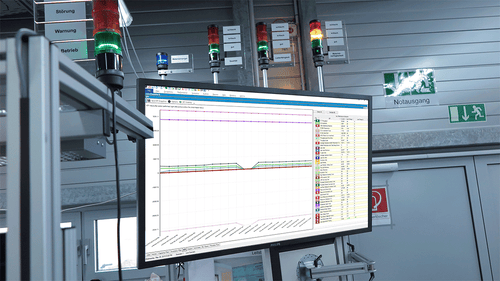
Integration in Action: PlanetTogether with SAP, Oracle, Microsoft, Kinaxis, or Aveva
PlanetTogether has built proven integrations with leading ERP platforms, enabling medical manufacturers to:
Leverage SAP’s robust business data for precise scheduling decisions.
Enhance Oracle’s financial and supply chain management with real-time production optimization.
Integrate Microsoft Dynamics’ flexible ERP framework with advanced production scenarios.
Connect Kinaxis’ supply chain planning directly to factory-level scheduling and execution.
Align Aveva’s industrial automation systems with holistic planning models.
For Manufacturing IT teams, these integrations don’t just deliver incremental improvements — they lay the foundation for a fully automated, agile manufacturing environment.
Key Benefits: What Medical Manufacturers Can Expect
With APS and ERP integration, medical manufacturing organizations can achieve:
20–30% reduction in production lead times through smarter, real-time scheduling.
Improved on-time delivery rates, even in high-mix, low-volume environments.
Lower inventory and carrying costs by aligning procurement with optimized schedules.
Faster response to demand changes or disruptions, keeping customers satisfied.
Stronger compliance posture through automated traceability and documentation.
Greater cross-functional alignment between operations, finance, procurement, and quality teams.
Moving from Siloed to Synergized
Automating complex manufacturing workflows is no longer a luxury — it’s essential for survival and growth in the medical manufacturing sector. As products become more sophisticated, regulations tighten, and market demands accelerate, the old ways of managing production simply can’t keep up.
For Manufacturing IT leaders, integrating PlanetTogether APS with ERP platforms like SAP, Oracle, Microsoft, Kinaxis, or Aveva is a strategic move that unlocks real automation, real optimization, and real business value.
By driving this synergy, IT teams can help their organizations move from siloed operations to a fully orchestrated, future-ready manufacturing enterprise.
Are you ready to take your manufacturing operations to the next level? Contact us today to learn more about how PlanetTogether can help you achieve your goals and drive success in your industry.