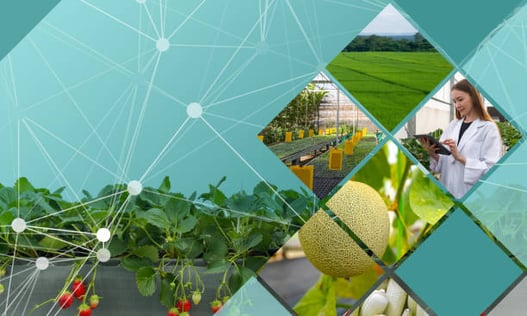
Bridging Health and Sustainability in Food & Beverage Manufacturing Through IT Innovation and APS Integration
As the food and beverage (F&B) industry evolves in response to growing consumer demand for healthier products and environmentally sustainable practices, Manufacturing IT Managers find themselves at the forefront of this transformation. Digitalization, data integration, and advanced planning systems (APS) are no longer optional — they’re essential to maintaining competitive advantage and compliance with evolving regulations.
This blog explores how IT leaders in F&B manufacturing can support health and sustainability initiatives by leveraging advanced technology solutions. Specifically, we’ll examine the benefits of integrating PlanetTogether APS with enterprise systems like SAP, Oracle, Microsoft, Kinaxis, and Aveva to achieve optimized operations, lower emissions, and safer food production environments.
The Dual Challenge: Consumer Health and Environmental Responsibility
Consumers today want it all: nutritious, clean-label food that is ethically sourced, sustainably packaged, and affordably priced. Meanwhile, governments and regulatory bodies are imposing stringent guidelines on food safety, energy use, and carbon emissions.
For IT managers, the implications are profound:
Data complexity: Managing sustainability-related data such as energy consumption, emissions, and traceability.
System interoperability: Ensuring seamless data flow between shop floor systems and ERP platforms.
Sustainability metrics: Enabling real-time reporting and analysis of sustainability KPIs across production processes.
Health compliance: Supporting food safety through digital process controls and predictive analytics.
This is where integrated planning and execution platforms like PlanetTogether APS, working in conjunction with ERP systems such as SAP or Microsoft Dynamics, play a pivotal role.
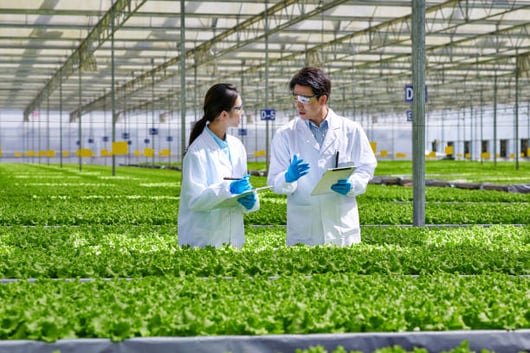
The Role of IT in Sustainable Manufacturing
Modern Manufacturing IT Managers act as the architects of digital transformation. In the context of health and sustainability, their responsibilities span:
Deploying technologies that reduce waste and energy consumption.
Enabling traceability across the supply chain to ensure food safety.
Facilitating real-time decision-making to minimize emissions and optimize resource usage.
Implementing automation and AI to boost efficiency and reduce human error in sensitive processes.
With these goals in mind, IT departments must design integrated digital ecosystems that bring together operational data, scheduling systems, and sustainability intelligence.
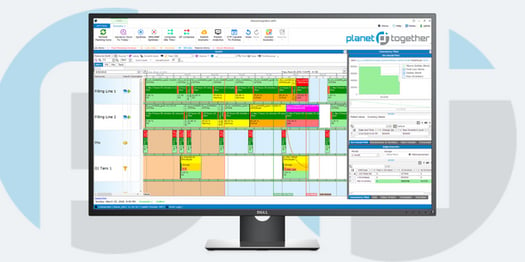
PlanetTogether APS: A Digital Bridge to Greener Outcomes
PlanetTogether’s Advanced Planning and Scheduling (APS) software is a game changer for F&B manufacturers looking to embed sustainability into their operations. When integrated with ERP systems like Oracle NetSuite, SAP S/4HANA, Kinaxis RapidResponse, or Microsoft Dynamics 365, PlanetTogether becomes a critical enabler of:
Optimized Production Scheduling for Lower Emissions
By minimizing machine changeovers, idle times, and overproduction, PlanetTogether reduces energy usage and resource waste. With integrated data from ERP systems, production schedules are automatically adjusted based on material availability, labor capacity, and environmental impact metrics.
Sustainable Resource Utilization
The integration of APS and ERP platforms enables planners to run scenarios that balance production output with environmental considerations. For example, manufacturers can prioritize runs that use renewable energy during peak solar hours or minimize water usage during drought-prone seasons.
Food Safety Compliance
PlanetTogether helps maintain batch traceability, schedule hygiene cycles efficiently, and align production plans with allergen management protocols. When connected to systems like Aveva’s manufacturing execution platform, IT teams can enforce strict controls on sanitation procedures and hazard analysis.
Real-Time Sustainability Reporting
With all systems synchronized, IT teams can generate dashboards tracking sustainability metrics like carbon footprint per batch, packaging material efficiency, and waste reduction — vital for ESG reporting and audits.
Strategic Integration: The IT Manager's Playbook
To implement a future-proof digital strategy for health and sustainability in F&B manufacturing, IT managers should consider the following:
Conduct a Digital Readiness Audit
Evaluate current systems for data availability, interoperability, and automation readiness. Identify gaps in capturing sustainability-related data like water usage, carbon emissions, and raw material sourcing.
Choose the Right Integration Framework
Ensure seamless data flow between PlanetTogether APS and core ERP/MES platforms such as Oracle, Kinaxis, or Aveva. Use APIs, connectors, and middleware solutions to enable scalable integration.
Prioritize Predictive and Prescriptive Analytics
Use AI models within ERP-APS integrations to predict maintenance needs, spoilage risk, or sustainability threshold breaches. Let these insights drive scheduling decisions in PlanetTogether.
Create Cross-Functional Dashboards
Build unified dashboards that include scheduling KPIs, health compliance data, and sustainability metrics for transparency and quick decision-making.
Involve Sustainability Officers and QA Teams
Ensure that planning and IT teams regularly collaborate with sustainability and quality assurance personnel. Their input ensures that schedules align with both ecological goals and health standards.
For the F&B industry, the intersection of health and sustainability represents a complex challenge — but also an immense opportunity. By adopting a strategic IT-led approach centered around integration, optimization, and real-time intelligence, manufacturers can align operations with the values of today’s consumers.
PlanetTogether APS, when integrated with robust ERP systems like SAP, Oracle, Microsoft, Kinaxis, and Aveva, empowers IT leaders to schedule smarter, operate cleaner, and produce safer — helping build a food system that’s as sustainable as it is successful.
Are you ready to take your manufacturing operations to the next level? Contact us today to learn more about how PlanetTogether can help you achieve your goals and drive success in your industry.