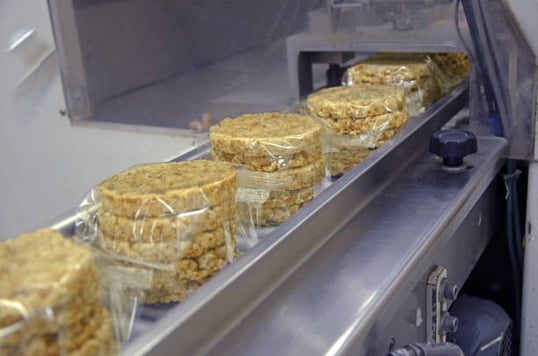
Circular Packaging in Food Manufacturing: APS for Sustainable Operations
In food and beverage manufacturing, sustainability is no longer a “nice to have” — it’s a business imperative. Consumers, regulators, and retail partners are all demanding greener products, reduced waste, and transparent sustainability practices. One area under increasing scrutiny is packaging: single-use plastics, non-recyclable materials, and excessive packaging are being replaced with circular, sustainable alternatives.
For a Plant Manager navigating the complexities of production, this shift isn’t just a material change — it’s a process transformation. Integrating circular packaging models into existing operations while maintaining efficiency, cost control, and regulatory compliance is a challenge. This is where Advanced Planning and Scheduling (APS) tools like PlanetTogether, especially when integrated with major enterprise systems like SAP, Oracle, Microsoft Dynamics, Kinaxis, or Aveva, can make all the difference.
This blog explores how APS enables food manufacturers to drive sustainable operations by aligning circular packaging strategies with optimized production planning.
Understanding Circular Packaging
Circular packaging is part of the broader circular economy concept: a system where materials are reused, recycled, or composted, creating closed-loop processes that reduce waste and environmental impact. In the food industry, this can involve:
Using recyclable or biodegradable materials
Incorporating post-consumer recycled (PCR) content
Designing reusable packaging (e.g., refillable containers)
Implementing take-back or recovery programs
However, adopting these solutions often introduces operational complexities:
Variability in supplier availability or material quality
Need for precise lot tracking and traceability
Adjustments in line setup or equipment
Coordination across multiple production sites and partners
Without the right planning systems, these complexities can result in delays, inefficiencies, and cost overruns.
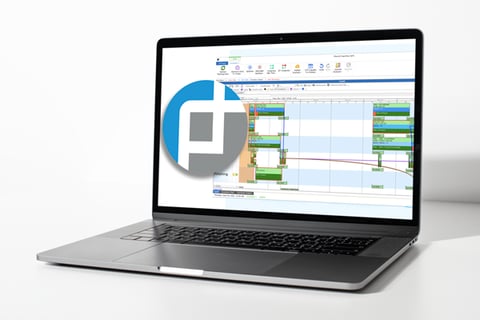
The Role of APS in Circular Packaging Integration
Advanced Planning and Scheduling software like PlanetTogether APS offers a solution by giving plant managers the tools to model, simulate, and optimize production schedules in alignment with sustainability goals.
Here’s how APS supports circular packaging initiatives:
Material Substitution Modeling
APS can incorporate alternative materials into its planning logic. For example, if certain recycled materials have longer lead times or limited availability, PlanetTogether can schedule production runs accordingly, reducing the risk of line stoppages or missed deliveries.
Optimized Equipment Utilization
Switching to new packaging materials often requires equipment adjustments (e.g., slower machine speeds or different temperature settings). APS systems simulate these operational impacts and adjust schedules to minimize downtime and maximize throughput.
Multi-Plant Coordination
For manufacturers operating across multiple sites, integrating circular packaging may involve shared resources or staggered implementation. PlanetTogether APS, when integrated with SAP, Oracle, Microsoft, Kinaxis, or Aveva platforms, enables cross-plant visibility, allowing plant managers to balance loads, share best practices, and align rollout timelines.
Sustainability KPI Tracking
Many food manufacturers track metrics like carbon footprint, waste reduction, and water usage. APS platforms can integrate these KPIs directly into the scheduling process, helping plant managers make decisions that optimize both operational and environmental performance.
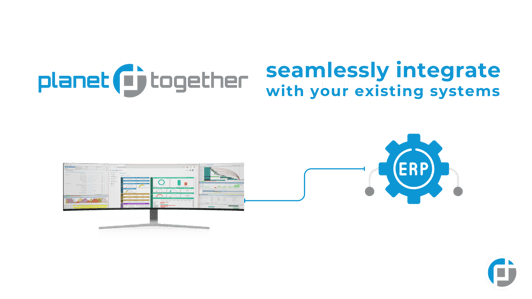
Integrating APS with Enterprise Systems for Full Visibility
While APS systems are powerful on their own, they reach full potential when integrated with enterprise resource planning (ERP), supply chain management (SCM), and manufacturing execution systems (MES).
For example:
SAP or Oracle ERP Integration ensures that material master data, purchase orders, and inventory levels are aligned with APS, preventing planning errors when switching between conventional and sustainable packaging.
Microsoft Dynamics or Kinaxis Integration enhances demand planning, so circular packaging supply constraints are reflected in sales forecasts and customer commitments.
Aveva MES Integration provides real-time shop floor data back to the APS system, helping fine-tune schedules based on actual production performance.
Through these integrations, PlanetTogether APS becomes the intelligent hub that connects strategic sustainability goals with day-to-day manufacturing execution.
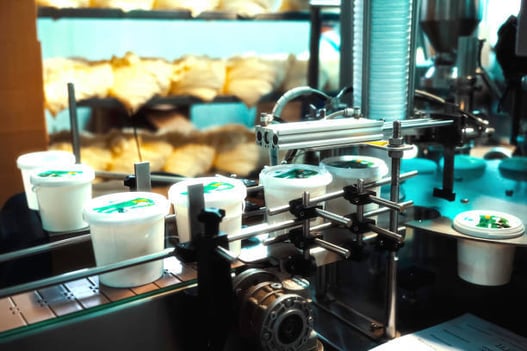
Key Benefits for Plant Managers
For a Plant Manager overseeing food production, adopting circular packaging through APS integration delivers multiple advantages:
Increased Scheduling Agility
With circular packaging, variability is the norm — material supply, equipment adjustments, and compliance checks can disrupt standard processes. APS enables rapid rescheduling and scenario analysis, so the plant can pivot quickly without sacrificing output.
Waste and Scrap Reduction
APS helps reduce overproduction, improve batch sizes, and fine-tune production runs, minimizing material waste — a critical goal when working with premium-priced sustainable materials.
Regulatory and Quality Compliance
Circular packaging materials often come with unique compliance requirements, from food safety certifications to environmental impact documentation. APS systems ensure that all production steps align with these requirements, reducing the risk of non-compliance.
Improved Supplier Collaboration
With integration to ERP and SCM systems, APS tools allow better communication with suppliers, ensuring that packaging materials arrive just in time, reducing storage costs and improving freshness.
Enhanced ESG Performance Reporting
Sustainability is not just about doing better — it’s about proving it. APS data, when integrated with corporate ESG reporting systems, provides evidence of waste reduction, energy savings, and other sustainability gains achieved through circular packaging adoption.
Implementation Considerations
For Plant Managers looking to deploy APS to support circular packaging, there are a few critical steps to consider:
Align Cross-Functional Teams
Sustainability efforts touch multiple departments — procurement, R&D, operations, and marketing. Ensure that APS configurations account for cross-functional priorities, from material specifications to customer delivery expectations.
Start with Pilot Lines
Rather than overhaul the entire plant at once, use APS to test circular packaging changes on select lines or SKUs. Analyze the results, refine the schedules, and scale up gradually.
Integrate Data Sources Early
Ensure that PlanetTogether APS is properly integrated with your ERP, MES, and SCM platforms. Without clean, real-time data, the best planning tools cannot deliver optimal results.
Train the Scheduling Team
Equip schedulers and planners with the skills to use APS features like scenario analysis, sustainability KPI tracking, and multi-site coordination. Well-trained teams will extract the most value from the system.
Circular packaging is more than a packaging team project — it’s a plant-wide transformation that requires precise planning, cross-functional alignment, and advanced scheduling capabilities. For Plant Managers, tools like PlanetTogether APS offer the visibility, flexibility, and intelligence needed to navigate this shift successfully.
By leveraging PlanetTogether APS alongside integrated enterprise platforms, food manufacturers can embed sustainability into every production decision, turning circular packaging from a compliance challenge into a competitive advantage.
In a world where consumers care about what’s inside and outside the box, it’s time to put sustainable operations at the heart of manufacturing — with PlanetTogether APS leading the way.
Are you ready to take your manufacturing operations to the next level? Contact us today to learn more about how PlanetTogether can help you achieve your goals and drive success in your industry.