Data-Driven Demand Forecasting with AI Techniques for Intermittent Demand Patterns
Supply chain managers face an array of challenges in meeting demand while optimizing resources in chemical manufacturing. One of the most pressing issues is forecasting demand accurately, especially when dealing with intermittent demand patterns. Traditional forecasting methods often fall short in capturing the nuances of such patterns, leading to inefficiencies and missed opportunities.
However, the advent of artificial intelligence (AI) has revolutionized demand forecasting by leveraging vast amounts of data to uncover hidden patterns and trends.
In this blog, we will look into the importance of data-driven demand forecasting for intermittent demand patterns in chemical manufacturing facilities. Furthermore, we will explore how integration between advanced planning and scheduling (APS) solutions like PlanetTogether and enterprise resource planning (ERP) systems such as SAP, Oracle, Microsoft, Kinaxis, and Aveva can enhance forecasting accuracy and streamline operations.
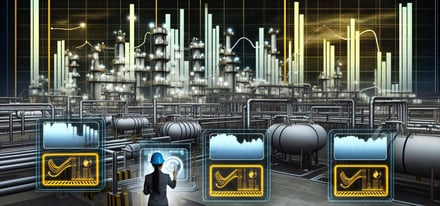
Intermittent Demand Patterns
Intermittent demand refers to sporadic or irregular patterns in customer orders, characterized by periods of both high and low demand variability. This poses a significant challenge for supply chain managers, as traditional forecasting methods designed for steady demand patterns often yield inaccurate results when applied to intermittent demand.
Chemical manufacturing facilities typically encounter intermittent demand for specialized products, seasonal variations, or customer-specific requirements. Without a reliable forecasting mechanism in place, companies risk overstocking or understocking inventory, leading to increased carrying costs, stockouts, or lost sales opportunities.
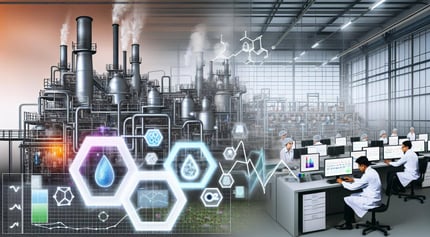
The Role of Data-Driven Forecasting
Data-driven forecasting leverages historical sales data, market trends, and other relevant variables to generate more accurate predictions of future demand. By harnessing the power of AI and machine learning algorithms, supply chain managers can analyze complex datasets and identify underlying patterns that traditional methods may overlook.
One of the key advantages of AI-based forecasting is its ability to adapt to changing market conditions and demand dynamics in real-time. This agility enables supply chain managers to make informed decisions quickly, optimize inventory levels, and improve customer service levels.
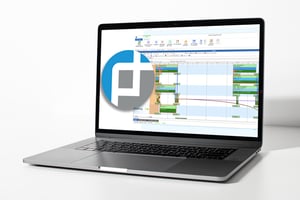
Integration between PlanetTogether and ERP Systems
Effective demand forecasting relies on seamless integration between APS solutions like PlanetTogether and ERP systems such as SAP, Oracle, Microsoft, Kinaxis, and Aveva. This integration facilitates the exchange of critical data between planning and execution stages, enabling a synchronized approach to supply chain management.
By integrating PlanetTogether with ERP systems, supply chain managers can achieve the following benefits:
Enhanced Data Visibility: Integration enables real-time access to inventory levels, production schedules, and sales data, providing a comprehensive view of the supply chain ecosystem.
Improved Forecast Accuracy: By incorporating data from ERP systems into the forecasting process, AI algorithms can generate more precise demand forecasts, taking into account factors such as production capacity, lead times, and material availability.
Streamlined Planning Processes: Integration streamlines planning processes by automating data exchange between different systems, reducing manual errors and minimizing lead times.
Optimized Inventory Management: Accurate demand forecasts enable proactive inventory management, ensuring that the right products are available at the right time and in the right quantities, thereby reducing excess inventory and stockouts.
Responsive Supply Chain: Integrated systems enable supply chain managers to respond quickly to changes in demand or market conditions, allowing for agile adjustments to production schedules and inventory levels.
Data-driven demand forecasting is essential for optimizing supply chain operations in chemical manufacturing facilities, especially when dealing with intermittent demand patterns. By leveraging AI techniques and integrating advanced planning and scheduling solutions like PlanetTogether with ERP systems, supply chain managers can improve forecast accuracy, optimize inventory management, and enhance overall operational efficiency.
The seamless exchange of data between planning and execution stages enables companies to respond quickly to changes in demand, minimize risks, and capitalize on emerging opportunities. As the industry continues to evolve, embracing innovative technologies and integrated solutions will be crucial for staying ahead of the competition and delivering superior customer value.
Are you ready to take your manufacturing operations to the next level? Contact us today to learn more about how PlanetTogether can help you achieve your goals and drive success in your industry.