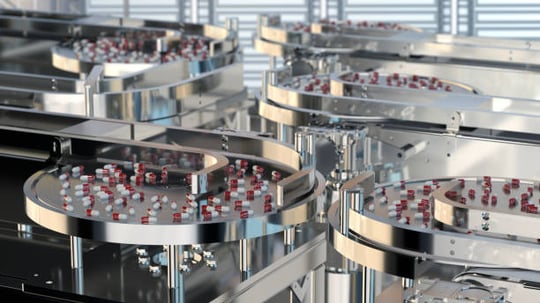
Demand Forecast Volatility: Using APS to Stabilize Production Pipelines in Pharmaceutical Manufacturing
In the pharmaceutical manufacturing world, unpredictability is the norm. Sudden regulatory changes, supply chain disruptions, evolving patient needs, and global health emergencies like pandemics or geopolitical events can swing demand forecasts overnight. For a Production Planner, this volatility isn’t just inconvenient — it’s a constant balancing act between ensuring product availability and avoiding costly overproduction or waste.
Enter Advanced Planning and Scheduling (APS) systems. APS tools, particularly when integrated with enterprise platforms like PlanetTogether alongside ERP systems such as SAP, Oracle, Microsoft Dynamics, Kinaxis, or Aveva, offer pharmaceutical manufacturers a way to navigate this storm. These integrated systems bring agility, precision, and data-driven intelligence to production planning, helping stabilize production pipelines even when demand forecasts are in flux.
The Challenge: Volatile Demand in Pharma
Unlike many other manufacturing sectors, pharmaceutical demand is shaped by forces that can shift without warning.
Regulatory changes: A drug approval, withdrawal, or change in labeling can swing demand dramatically.
Public health trends: Disease outbreaks, seasonal illness patterns, and vaccination campaigns create sudden surges.
Patient and healthcare provider behavior: Prescribing trends, insurance policy changes, and patient adherence rates all shift demand.
Global supply chain fragility: Ingredient shortages, transportation delays, or political events can choke the availability of critical raw materials, forcing last-minute adjustments.
Without robust planning tools, production planners can end up scrambling to reshuffle production lines, secure alternative materials, or delay shipments — all while ensuring strict compliance with regulatory and quality standards.
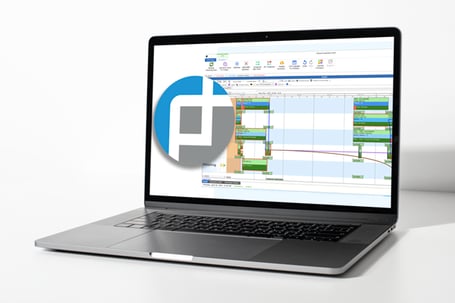
APS: Turning Chaos Into Clarity
Advanced Planning and Scheduling systems shine in this environment. APS platforms are designed to process vast amounts of data, model complex production constraints, and create optimized schedules that reflect real-world conditions.
For pharmaceutical manufacturing, this means:
Dynamic scenario planning: APS systems can run “what-if” simulations to help planners anticipate the impact of a sudden demand spike or material shortage.
Constraint-based scheduling: They factor in equipment availability, batch sizes, cleaning cycles, and regulatory requirements when creating plans.
Real-time visibility: APS tools integrate with ERP systems, pulling in data from sales forecasts, inventory levels, supplier statuses, and shop floor operations to create a live view of the production pipeline.
Automated rescheduling: When forecasts change, APS can rapidly generate updated production schedules, minimizing manual intervention and reducing the risk of human error.
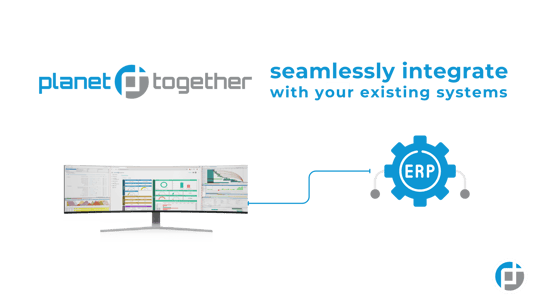
PlanetTogether APS + ERP Integration: A Game Changer
While APS systems are powerful on their own, their real strength comes when they are integrated seamlessly with a company’s ERP backbone — such as SAP, Oracle, Microsoft Dynamics, Kinaxis, or Aveva.
PlanetTogether APS specializes in delivering this kind of integration. Here’s why it matters for pharmaceutical production planners:
Unified data environment: Instead of working with disconnected spreadsheets or isolated software tools, production planners can access a single source of truth that connects demand forecasts, material availability, production capacity, and supplier commitments.
Automated updates: Changes in sales orders or procurement delays captured in the ERP system automatically update the APS schedules, eliminating the time lag between decision-making layers.
Advanced analytics and dashboards: PlanetTogether’s visual dashboards provide production planners with intuitive insights into bottlenecks, risks, and opportunities, enabling faster, more informed decisions.
Compliance support: Integration ensures that critical compliance data — such as lot traceability, batch records, and validated equipment statuses — flow into the planning process, reducing regulatory risks.
Stabilizing the Pipeline: Key APS Strategies
Let’s break down how APS stabilizes production in the face of demand forecast volatility:
Prioritized Scheduling
APS tools help planners prioritize high-value or at-risk orders when capacity is strained. For example, if two products compete for the same reactor, but one has a critical delivery window for a clinical trial, the system can automatically allocate resources accordingly.
Safety Stock Optimization
Rather than blanket overproduction, APS systems calculate optimal safety stock levels based on lead times, variability, and service levels. This balances the need for availability without incurring excess inventory carrying costs.
Supplier Risk Modeling
Integrated APS + ERP setups let planners factor in supplier reliability data. If a key active pharmaceutical ingredient (API) supplier shows a rising risk profile, planners can proactively adjust schedules or explore alternative sourcing.
Capacity Buffering and Flexible Production
APS enables the creation of capacity buffers — small pockets of reserved production time that can absorb last-minute changes. It also supports flexible manufacturing, allowing planners to quickly switch between products or lines without massive retooling.
Collaborative Planning Across Sites
For multi-site pharmaceutical manufacturers, PlanetTogether APS can align schedules across multiple facilities, ensuring that production is balanced across the network rather than siloed. This reduces the risk that one site becomes a bottleneck while another has unused capacity.
Harnessing APS to Turn Uncertainty Into Competitive Advantage
For pharmaceutical Production Planners, demand volatility will always be part of the job. But how they respond to it can make the difference between smooth operations and costly disruptions.
By leveraging PlanetTogether APS integrated with leading ERP systems like SAP, Oracle, Microsoft, Kinaxis, or Aveva, planners can transform their production pipelines into resilient, flexible, and optimized systems.
The result?
Reduced waste and overproduction
Faster, smarter responses to market shifts
Greater alignment across procurement, production, and logistics
Improved regulatory compliance
In a world where every dose counts, stabilizing the production pipeline isn’t just good business — it’s essential to ensuring that critical medicines reach the patients who need them most.
Are you ready to take your manufacturing operations to the next level? Contact us today to learn more about how PlanetTogether can help you achieve your goals and drive success in your industry.