Lean Manufacturing Transformation
Staying competitive requires more than just delivering quality products—it demands efficiency, agility, and sustainability. In food and beverage manufacturing, lean manufacturing principles offer a pathway to achieving these objectives, enabling organizations to optimize processes, reduce waste, and enhance overall productivity. However, implementing lean practices in the complex environment of food and beverage manufacturing can pose significant challenges.
For Supply Chain Managers navigating this terrain, the integration of advanced planning and scheduling tools like PlanetTogether with Enterprise Resource Planning (ERP), Supply Chain Management (SCM), and Manufacturing Execution Systems (MES) presents a powerful solution. In this blog, we'll explore the journey toward lean manufacturing transformation in the food and beverage industry and the pivotal role of integrated technologies in driving success.

Lean Manufacturing Transformation
At its core, lean manufacturing is about continuous improvement, striving for perfection, and delivering value to customers while minimizing waste. In the context of food and beverage manufacturing, this translates into optimizing production processes, reducing lead times, and enhancing product quality—all while maintaining compliance with stringent regulations.
Key principles of lean manufacturing include:
- Value Stream Mapping: Identifying and eliminating non-value-added activities along the production journey.
- Just-in-Time (JIT) Production: Minimizing inventory levels by synchronizing production with customer demand.
- Total Quality Management (TQM): Fostering a culture of quality consciousness and continuous improvement.
- Continuous Flow: Streamlining production processes to enable smooth, uninterrupted flow of materials and information.
- Pull Systems: Allowing customer demand to drive production schedules and replenishment activities.
Challenges in Lean Implementation in Food and Beverage Manufacturing
While the benefits of lean manufacturing are compelling, the journey toward implementation can be fraught with obstacles. In the food and beverage industry, factors such as perishable raw materials, stringent regulatory requirements, and fluctuating demand patterns add layers of complexity to the manufacturing process.
Common challenges faced by Supply Chain Managers include:
- Variability in Demand: Fluctuating consumer preferences and seasonal demand patterns can disrupt production planning and scheduling.
- Short Shelf Life: Perishable ingredients and finished products necessitate precise inventory management and efficient production scheduling to minimize waste.
- Regulatory Compliance: Stringent food safety regulations require meticulous tracking and documentation throughout the manufacturing process.
- Batch Processing: Batch-based production processes can lead to inefficiencies and excess inventory if not managed effectively.
- Supply Chain Disruptions: External factors such as ingredient shortages, transportation delays, and geopolitical instability can impact supply chain continuity.

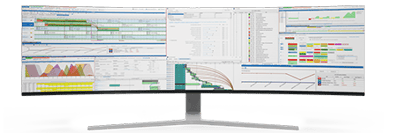
Integrating PlanetTogether with ERP, SCM, and MES Systems
To address these challenges and embark on a successful lean manufacturing transformation journey, Supply Chain Managers can leverage the integration of advanced planning and scheduling software like PlanetTogether with their existing ERP, SCM, and MES systems.
PlanetTogether offers robust capabilities for:
- Advanced Planning and Scheduling: Optimizing production schedules based on real-time demand signals, resource availability, and production constraints.
- Finite Capacity Planning: Balancing production loads across equipment and work centers to maximize throughput and minimize bottlenecks.
- What-If Analysis: Simulating different production scenarios to assess the impact of changes in demand, capacity, or resource allocation.
- Production Visibility: Providing real-time visibility into production progress, allowing for proactive decision-making and rapid response to disruptions.
- Collaboration and Communication: Facilitating cross-functional collaboration among production, planning, and logistics teams to ensure alignment and agility.
Integration with ERP, SCM, and MES systems further enhances the value proposition by:
- Seamless Data Exchange: Enabling the flow of critical information between planning, execution, and control systems, ensuring data integrity and accuracy.
- Closed-Loop Planning: Integrating production plans with inventory management, procurement, and order fulfillment processes to achieve end-to-end visibility and synchronization.
- Real-Time Monitoring and Control: Leveraging MES integration to capture production data in real-time, enabling proactive monitoring of key performance indicators and rapid response to deviations.
- Continuous Improvement: Harnessing ERP's analytical capabilities to identify opportunities for process optimization, cost reduction, and quality enhancement based on historical performance data.
- Scalability and Flexibility: Adapting to evolving business requirements and market dynamics by leveraging the scalability and flexibility of integrated systems architecture.
Embracing lean manufacturing principles is essential for driving operational excellence, maximizing efficiency, and delivering value to customers in food and beverage manufacturing. By integrating advanced planning and scheduling tools like PlanetTogether with ERP, SCM, and MES systems, Supply Chain Managers can overcome the challenges inherent in lean implementation and achieve sustainable success.
Through seamless data exchange, real-time visibility, and collaborative decision-making, organizations can optimize production processes, enhance resource utilization, and respond swiftly to changing market dynamics.
As Supply Chain Managers embark on their lean journey, leveraging the power of integrated systems will be instrumental in unlocking the full potential of lean manufacturing and driving continuous improvement across the food and beverage value chain.
Are you ready to take your manufacturing operations to the next level? Contact us today to learn more about how PlanetTogether can help you achieve your goals and drive success in your industry.