Mass Customization in Production
The concept of mass customization has emerged as a game-changer, especially in the realm of packaging manufacturing. Traditional mass production methods have long been the cornerstone of manufacturing processes, offering efficiency and cost-effectiveness.
However, with evolving consumer preferences and technological advancements, the demand for customized products is on the rise. This shift has paved the way for the integration of innovative technologies and software solutions to enable mass customization while maintaining the efficiency and scalability of production lines.
In this blog post, we will look into the concept of mass customization in the context of packaging manufacturing, exploring its benefits, challenges, and the role of IT solutions such as PlanetTogether in facilitating seamless integration with ERP, SCM, and MES systems like SAP, Oracle, Microsoft, Kinaxis, and Aveva.
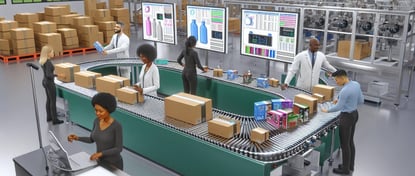
Mass Customization
Mass customization can be defined as the ability to produce personalized products on a large scale, catering to the unique preferences and requirements of individual customers. Unlike traditional mass production, which focuses on producing standardized goods in bulk, mass customization allows manufacturers to tailor products to meet the specific needs of consumers while still maintaining the efficiency and cost-effectiveness of mass production methods.
In the context of packaging manufacturing, mass customization opens up a world of possibilities. From personalized labels and designs to packaging materials tailored to different products, the ability to offer customization not only enhances the customer experience but also provides a competitive edge in the market.
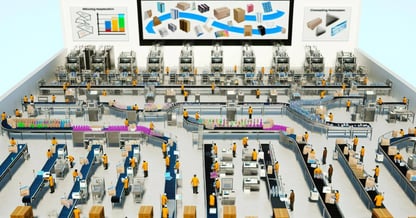
Benefits of Mass Customization in Packaging Manufacturing
Enhanced Customer Experience: By offering personalized packaging solutions, manufacturers can forge stronger connections with customers, fostering loyalty and brand advocacy.
Increased Flexibility: Mass customization enables manufacturers to quickly adapt to changing market demands and trends, allowing for greater flexibility in production processes.
Reduced Inventory Costs: With mass customization, manufacturers can produce goods on-demand, minimizing the need for excess inventory and reducing storage costs.
Improved Supply Chain Efficiency: By integrating IT solutions like PlanetTogether with ERP, SCM, and MES systems, manufacturers can streamline production scheduling, optimize inventory management, and enhance overall supply chain efficiency.
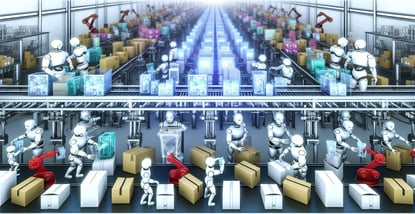
Challenges of Implementing Mass Customization
While the benefits of mass customization are undeniable, implementing this approach in packaging manufacturing comes with its own set of challenges:
Complexity in Production Planning: Customizing products requires intricate production planning to ensure optimal use of resources and minimize downtime. This complexity can pose challenges for manufacturers, especially those accustomed to traditional mass production methods.
Data Management and Integration: Integrating IT solutions such as PlanetTogether with existing ERP, SCM, and MES systems requires robust data management capabilities to ensure seamless communication and coordination between different systems.
Scalability: As demand for customized products grows, manufacturers must ensure that their production processes are scalable to meet increasing production volumes without compromising quality or efficiency.
Cost Considerations: Implementing mass customization may require upfront investments in technology and infrastructure, which can be a barrier for some manufacturers, especially smaller players in the industry.
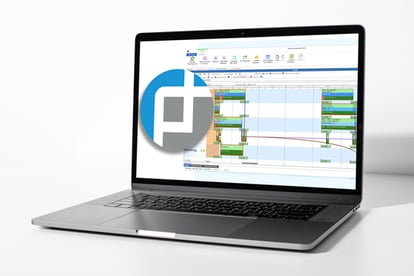
Integration of PlanetTogether with ERP, SCM, and MES Systems
To address these challenges and unlock the full potential of mass customization in packaging manufacturing, seamless integration between advanced planning and scheduling (APS) software like PlanetTogether and ERP, SCM, and MES systems is crucial.
PlanetTogether offers powerful planning and scheduling capabilities, allowing manufacturers to optimize production schedules, minimize lead times, and maximize resource utilization. By integrating PlanetTogether with ERP systems such as SAP, Oracle, Microsoft Dynamics, or MES systems like Aveva or Kinaxis, manufacturers can achieve greater visibility and control over their production processes, enabling efficient coordination across different departments and functions.
Key features of integrating PlanetTogether with ERP, SCM, and MES systems include:
Real-time Data Sync: Integration ensures that production data is automatically synchronized between PlanetTogether and ERP, SCM, and MES systems, providing accurate and up-to-date information for planning and scheduling.
Seamless Communication: Integrated systems enable seamless communication and collaboration between different departments, allowing for better coordination and decision-making.
Advanced Analytics: By harnessing the power of integrated data, manufacturers can gain valuable insights into production performance, identify bottlenecks, and make informed decisions to optimize processes and improve efficiency.
Scalability and Flexibility: Integrated solutions are scalable and flexible, allowing manufacturers to adapt to changing business needs and scale their operations to meet growing demand for customized products.
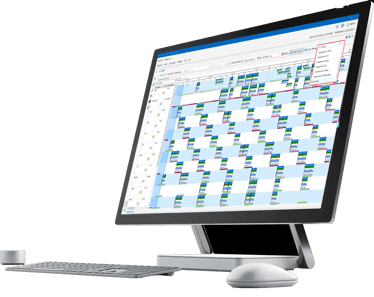
Implementing Mass Customization with PlanetTogether Integration
Let's consider a hypothetical scenario where a packaging manufacturer decides to implement mass customization in their production processes. By integrating PlanetTogether with their existing ERP system, the manufacturer can achieve the following outcomes:
Streamlined Production Planning: PlanetTogether's advanced planning and scheduling capabilities enable the manufacturer to create optimized production schedules based on customer orders, inventory levels, and resource constraints.
Just-in-Time Manufacturing: Integration with the ERP system allows the manufacturer to synchronize production schedules with inventory levels, enabling just-in-time manufacturing to minimize excess inventory and reduce storage costs.
Enhanced Visibility and Control: Integrated data provides real-time visibility into production processes, allowing the manufacturer to monitor performance metrics, identify potential issues, and take proactive measures to ensure smooth operations.
Improved Customer Satisfaction: By offering personalized packaging solutions with shorter lead times and consistent quality, the manufacturer can enhance customer satisfaction and build long-lasting relationships with clients.
Mass customization represents a paradigm shift in packaging manufacturing, offering new opportunities for differentiation and growth in an increasingly competitive market. By embracing innovative technologies and integrating advanced planning and scheduling solutions like PlanetTogether with ERP, SCM, and MES systems, manufacturers can unlock the full potential of mass customization while maintaining efficiency, scalability, and cost-effectiveness in their production processes.
As consumer preferences continue to evolve, the ability to offer personalized packaging solutions will become increasingly important for manufacturers looking to stay ahead of the curve. By investing in the right technology and embracing a customer-centric approach to production, packaging manufacturers can position themselves for success in the era of mass customization.
Are you ready to take your manufacturing operations to the next level? Contact us today to learn more about how PlanetTogether can help you achieve your goals and drive success in your industry.