Enhancing Inventory Visibility
In the intricate landscape of pharmaceutical manufacturing, maintaining optimal inventory visibility across the supply chain is paramount. As a Supply Chain Manager, you understand the critical role inventory management plays in ensuring timely production, minimizing costs, and meeting regulatory requirements. However, achieving seamless visibility can be challenging, especially in a complex environment with diverse stakeholders, stringent regulations, and fluctuating market demands.
In this blog, we look into the importance of inventory visibility in pharmaceutical supply chains and explore strategies to enhance it. Furthermore, we'll discuss the integration between PlanetTogether, a leading advanced planning and scheduling (APS) solution, and prominent ERP, SCM, and MES systems such as SAP, Oracle, Microsoft, Kinaxis, and Aveva, to streamline operations and optimize inventory management.
Inventory Visibility
Inventory visibility refers to the ability to track and monitor inventory levels, movements, and transactions across the supply chain in real-time. It involves gaining insights into the location, quantity, and status of inventory at various stages, from raw materials procurement to manufacturing, distribution, and ultimately, customer delivery. Effective inventory visibility enables Supply Chain Managers to make informed decisions, mitigate risks, and enhance operational efficiency.
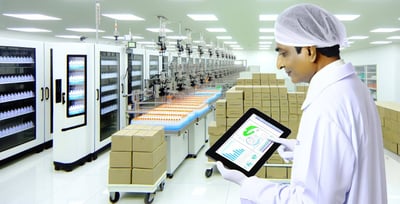
Achieving Inventory Visibility
Fragmented Data Sources: Pharmaceutical supply chains often operate across multiple locations, with various departments and stakeholders involved. As a result, data is dispersed across different systems, making it challenging to consolidate and analyze.
Lack of Interoperability: Incompatibility between systems, such as ERP, SCM, and MES, can hinder data sharing and integration, leading to siloed information and inefficiencies.
Regulatory Compliance: Stringent regulations, such as Good Manufacturing Practices (GMP) and Drug Supply Chain Security Act (DSCSA), require accurate tracking and traceability of pharmaceutical products, adding complexity to inventory management.
Demand Volatility: Fluctuating market demands, seasonal variations, and unforeseen events, such as pandemics or natural disasters, can disrupt supply chain operations and impact inventory visibility.
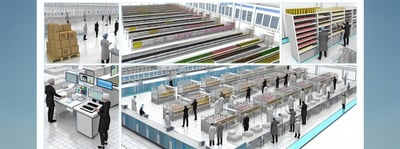
Strategies for Enhancing Inventory Visibility
Centralized Data Management: Implementing a centralized data repository that integrates data from various sources facilitates real-time visibility into inventory levels, transactions, and performance metrics. Advanced planning and scheduling (APS) solutions like PlanetTogether offer robust data aggregation capabilities, allowing Supply Chain Managers to access comprehensive insights across the supply chain.
Integration with ERP, SCM, and MES Systems: Seamless integration between APS and other enterprise systems, including SAP, Oracle, Microsoft, Kinaxis, and Aveva, is crucial for synchronizing data and processes. By integrating PlanetTogether with these systems, Supply Chain Managers can streamline inventory management, improve collaboration, and enhance decision-making capabilities.
Real-time Monitoring and Analytics: Leveraging advanced analytics and reporting tools enables Supply Chain Managers to monitor inventory movements, identify trends, and forecast demand accurately. With real-time visibility into key performance indicators (KPIs) such as stock levels, lead times, and fill rates, they can proactively address issues and optimize inventory levels.
Track and Trace Technologies: Implementing track and trace technologies, such as barcoding, RFID, and serialization, enhances product traceability and ensures compliance with regulatory requirements. By capturing detailed information about each product's journey through the supply chain, Supply Chain Managers can trace the origin of any issues and take prompt corrective actions.
Collaborative Partnerships: Establishing collaborative partnerships with suppliers, contract manufacturers, distributors, and logistics providers fosters transparency and communication across the supply chain. By sharing relevant information and aligning processes, stakeholders can work together to optimize inventory visibility and improve supply chain resilience.

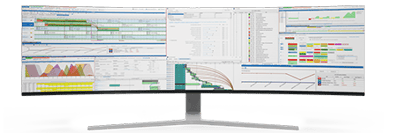
Integration between PlanetTogether and ERP, SCM, and MES Systems
PlanetTogether offers seamless integration capabilities with leading ERP, SCM, and MES systems, including SAP, Oracle, Microsoft Dynamics, Kinaxis RapidResponse, and Aveva MES. By connecting these systems, Supply Chain Managers can achieve end-to-end visibility and orchestrate synchronized planning and execution processes.
SAP Integration: Integration between PlanetTogether and SAP enables real-time synchronization of production schedules, inventory levels, and material requirements. Supply Chain Managers can leverage SAP's robust functionalities for order management, procurement, and financials, while utilizing PlanetTogether's advanced planning capabilities to optimize production efficiency and inventory utilization.
Oracle Integration: By integrating PlanetTogether with Oracle ERP and SCM Cloud, Supply Chain Managers can streamline planning, procurement, and manufacturing operations. Seamless data exchange between the two systems enables accurate demand forecasting, inventory optimization, and agile response to market dynamics, enhancing overall supply chain performance.
Microsoft Dynamics Integration: Integration between PlanetTogether and Microsoft Dynamics 365 provides Supply Chain Managers with a unified platform for planning, production, and inventory management. Leveraging Microsoft's cloud-based infrastructure and intuitive user interface, alongside PlanetTogether's advanced planning capabilities, enables seamless collaboration and decision-making across the organization.
Kinaxis RapidResponse Integration: Integration between PlanetTogether and Kinaxis RapidResponse enables Supply Chain Managers to synchronize planning activities and achieve real-time visibility into supply chain dynamics. By connecting production scheduling with demand forecasting, inventory optimization, and supply chain planning, organizations can respond rapidly to changes and improve overall operational efficiency.
Aveva MES Integration: Integration between PlanetTogether and Aveva MES facilitates seamless coordination between production scheduling and shop floor execution. By synchronizing production plans with manufacturing operations, organizations can optimize resource utilization, minimize downtime, and improve overall production efficiency.
Achieving enhanced inventory visibility across the pharmaceutical supply chain is essential for optimizing operations, ensuring compliance, and meeting customer demands. By implementing strategies such as centralized data management, real-time monitoring, and integration with ERP, SCM, and MES systems, Supply Chain Managers can overcome challenges and drive sustainable growth.
Moreover, leveraging advanced planning and scheduling solutions like PlanetTogether, integrated with leading enterprise systems, empowers organizations to adapt to changing market dynamics and stay competitive in the dynamic pharmaceutical industry.
Are you ready to take your manufacturing operations to the next level? Contact us today to learn more about how PlanetTogether can help you achieve your goals and drive success in your industry.