Manufacturing Material Traceability
In the complex manufacturing landscape, ensuring material traceability is not just a regulatory requirement but also a crucial aspect for operational efficiency and product quality assurance. For Operations Directors in Chemical manufacturing facilities, maintaining a seamless flow of materials while adhering to stringent regulations is essential.
In this blog, we look into the significance of material traceability in chemical manufacturing and explore how integration between PlanetTogether and leading ERP, SCM, and MES systems can streamline processes and enhance traceability.
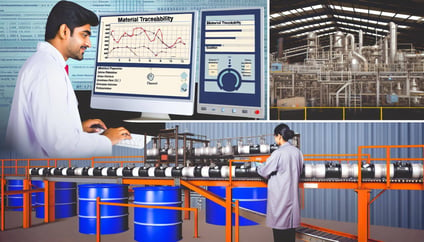
Material Traceability in Chemical Manufacturing
Material traceability refers to the ability to track and trace raw materials, components, and products throughout the manufacturing process and supply chain. In the chemical industry, where the handling of hazardous substances is common, ensuring traceability is particularly critical for regulatory compliance, risk mitigation, and maintaining customer trust.
Challenges in Material Traceability
Chemical manufacturing operations face several challenges when it comes to material traceability:
Complex Supply Chains: Chemical manufacturing often involves intricate supply chains with multiple suppliers, intermediaries, and distributors, making it challenging to track materials from source to end product.
Regulatory Compliance: Regulatory bodies impose strict guidelines regarding the handling, labeling, and traceability of chemical substances to ensure safety and environmental protection.
Quality Assurance: Maintaining high product quality and consistency requires accurate tracking of materials and processes throughout the production cycle.
Data Silos: Information fragmentation across different systems and departments can hinder real-time visibility and traceability, leading to inefficiencies and errors.
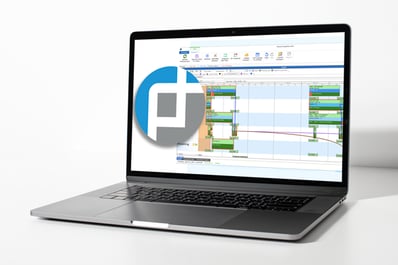
Integrating PlanetTogether with ERP, SCM, and MES Systems
To address these challenges and enhance material traceability, Operations Directors can leverage integration between advanced planning and scheduling (APS) solutions like PlanetTogether and leading ERP, SCM, and MES systems. Let's explore how such integration can optimize material traceability in chemical manufacturing:
Real-Time Data Synchronization: Integrating PlanetTogether with ERP systems such as SAP, Oracle, or Microsoft Dynamics enables seamless exchange of data, including inventory levels, production schedules, and material specifications. This real-time synchronization enhances visibility across the supply chain, allowing for better decision-making and traceability.
Enhanced Production Planning: By integrating APS with ERP and SCM systems, Operations Directors can optimize production planning and scheduling based on real-time demand forecasts, inventory levels, and resource availability. This ensures efficient utilization of materials and minimizes the risk of shortages or excess inventory, improving traceability and cost-effectiveness.
Automated Workflows: Integration with MES systems automates workflows and data capture on the shop floor, including batch tracking, material movements, and quality control processes. This automation reduces manual errors, accelerates data collection, and enhances traceability throughout the manufacturing process.
Compliance Management: Integrated systems facilitate adherence to regulatory requirements by enabling accurate documentation, labeling, and reporting of chemical materials and processes. Operations Directors can implement traceability protocols that align with industry standards such as REACH, GHS, and ISO certifications, ensuring compliance and mitigating risk.
Continuous Improvement: Data analytics capabilities provided by integrated systems allow Operations Directors to analyze historical performance data, identify trends, and optimize processes for greater efficiency and traceability. This iterative approach to improvement fosters a culture of continuous enhancement in material traceability and overall operational excellence.
In the realm of chemical manufacturing, material traceability is a fundamental aspect that impacts regulatory compliance, product quality, and operational efficiency. By leveraging integration between advanced planning and scheduling systems like PlanetTogether and leading ERP, SCM, and MES platforms, Operations Directors can overcome challenges associated with material traceability and unlock opportunities for optimization and innovation.
Investing in integrated solutions not only ensures compliance with regulatory standards but also drives competitive advantage through enhanced visibility, efficiency, and customer satisfaction.
Embrace the power of integration to elevate material traceability in your chemical manufacturing facility and pave the way for sustainable growth and success. Are you ready to take your manufacturing operations to the next level? Contact us today to learn more about how PlanetTogether can help you achieve your goals and drive success in your industry.