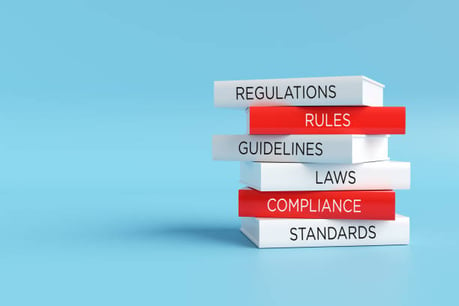
Ensuring Compliance with Industry Regulations: How APS Integration Empowers Packaging and Containers Manufacturing
Plant Managers in packaging and containers facilities face mounting pressure to uphold stringent industry regulations. Whether it’s compliance with environmental standards, food-contact material regulations, or workplace safety laws, staying aligned with both national and international rules is no longer optional—it’s essential. Yet, ensuring compliance while maintaining productivity and profitability can feel like walking a tightrope.
This is where Advanced Planning and Scheduling (APS) systems, such as PlanetTogether, integrated with leading enterprise systems like SAP, Oracle, Microsoft, Kinaxis, or Aveva, can become game-changers. By embedding compliance into daily operations through intelligent scheduling, data management, and real-time monitoring, APS solutions transform regulatory demands from burdensome tasks into integrated, automated processes that safeguard both the business and its reputation.
Let’s explore how Plant Managers can leverage this integration to navigate the complex web of regulations while optimizing their packaging operations.
The Growing Regulatory Landscape in Packaging
Packaging and containers manufacturers operate under a broad range of regulations, including:
Food Safety Modernization Act (FSMA) for food-contact packaging.
REACH (Registration, Evaluation, Authorization, and Restriction of Chemicals) for chemical safety.
Extended Producer Responsibility (EPR) laws that push sustainability and recyclability.
ISO 9001 and ISO 14001 standards for quality and environmental management.
OSHA regulations for worker safety.
Noncompliance can lead to severe penalties, product recalls, reputational damage, and even the loss of key customer contracts. With global supply chains adding layers of complexity, Plant Managers need robust systems to ensure every batch, lot, or shift is traceable, auditable, and compliant.
Where Compliance Challenges Arise
Many Plant Managers struggle with:
Disconnected systems
Regulatory data often sits siloed in quality management or compliance departments, making it hard for production teams to act on time.
Manual processes
Relying on spreadsheets or manual record-keeping to demonstrate compliance is risky and prone to error.
Lack of real-time visibility
Without live monitoring, deviations in material specs, machine performance, or batch processes might go undetected until it’s too late.
Complex supplier chains
If your suppliers fail to meet regulatory requirements, your operation is exposed.
Changing regulations
Keeping up with evolving standards across different regions or customer segments adds another layer of complexity.
To tackle these challenges, modern plants are turning to integrated solutions that bridge the gap between planning, execution, and compliance.
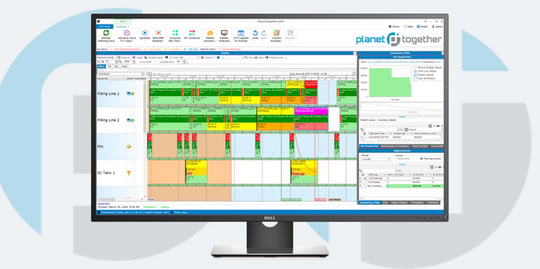
How PlanetTogether APS Supports Compliance
PlanetTogether APS, when integrated with ERP and MES systems like SAP, Oracle, Microsoft Dynamics, Kinaxis, or Aveva, creates a unified operational ecosystem where compliance is baked into every layer of the manufacturing process.
Here’s how:
Automated Scheduling with Built-In Compliance Checks
PlanetTogether can embed regulatory rules directly into the production schedule. For example:
Material compatibility rules (e.g., food-grade vs. industrial plastics) can be pre-set, ensuring that incompatible materials are never scheduled together.
Line cleaning or sterilization intervals can be automatically planned between sensitive product runs to meet safety standards.
Restricted substances or hazardous materials can be flagged, with production routes adjusted to meet handling or disposal requirements.
Because the system communicates directly with ERP platforms like SAP or Oracle, these compliance parameters are reflected in both the production plan and the procurement schedule, reducing manual oversight and potential misses.
Real-Time Data Capture and Traceability
Integrated APS + ERP systems offer real-time visibility across the entire production floor:
Batch records, material lot numbers, and equipment statuses are captured live.
If an input material is found noncompliant, the system can trigger an immediate rescheduling or quarantine of affected products.
Data logs from equipment (integrated through MES systems like Aveva) ensure that machine performance aligns with validated operating parameters.
This level of traceability is essential for audits, certifications, and regulatory filings—and it allows Plant Managers to sleep better at night.
Enhanced Change Management and Version Control
With changing customer requirements or regulatory updates, the ability to quickly adapt production processes is vital.
Through integration with ERP solutions like Microsoft Dynamics or Kinaxis, any changes in product specs, formulations, or packaging designs can be seamlessly reflected in the APS system.
Scheduling rules and recipes are version-controlled, ensuring that only the most current, compliant procedures are applied on the shop floor.
This reduces the risk of human error and accelerates change implementation without disrupting operations.
Supplier and Raw Material Compliance Management
APS doesn’t just manage in-plant activities—it also strengthens the supply chain compliance process:
Supplier qualifications and material certifications stored in SAP or Oracle can feed into PlanetTogether, so only approved suppliers and materials are scheduled.
If a supplier’s compliance status lapses, the system can automatically reroute procurement plans, avoiding costly disruptions or regulatory exposure.
By extending compliance oversight beyond the four walls of the plant, Plant Managers gain a holistic view of risk.
Proactive Alerts and Reporting
Integrated systems provide:
Automated alerts when deviations are detected, allowing for immediate corrective action.
Customizable compliance dashboards to monitor KPIs like lot traceability, deviation rates, or regulatory audit readiness.
Automated reports for internal teams, customers, or regulatory agencies, reducing the manual burden of paperwork.
These features empower Plant Managers to move from reactive fire-fighting to proactive compliance management.
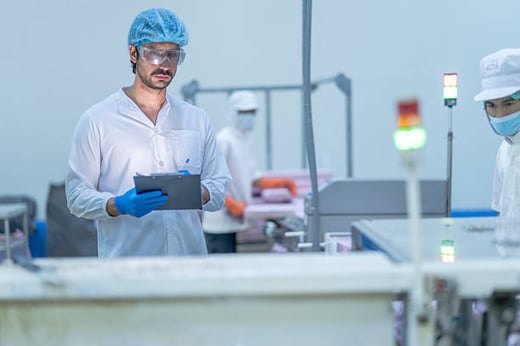
The Business Impact: Beyond Avoiding Penalties
While regulatory compliance is often seen as a “cost of doing business,” integrating APS with ERP systems unlocks broader business benefits:
Increased operational efficiency by reducing manual compliance tasks.
Fewer production disruptions caused by overlooked compliance issues.
Faster time-to-market for new products, thanks to streamlined change management.
Improved customer trust and market reputation, which can open doors to new business.
Data-driven insights for continuous improvement, not just compliance.
In short, compliance becomes a competitive advantage—not a bottleneck.
Building an Integrated Compliance Strategy
For Plant Managers aiming to strengthen their compliance posture, here’s a stepwise approach:
Assess Current Gaps
Map out current compliance workflows and identify where manual steps, data silos, or blind spots exist.
Align Compliance with Production Goals
Ensure that compliance strategies are integrated into production and scheduling, not layered on top as afterthoughts.
Invest in Integrated Technology
Implement or upgrade APS tools like PlanetTogether and ensure they’re fully integrated with your ERP, MES, and quality management systems.
Train Teams for Digital Compliance
Equip teams with the skills to leverage these tools effectively, focusing on data-driven compliance management.
Continuously Monitor and Improve
Use system-generated insights to refine processes, reduce waste, and enhance both compliance and efficiency.
In packaging and containers manufacturing, compliance is non-negotiable—but it doesn’t have to be a drag on operational performance. By integrating advanced planning tools like PlanetTogether APS with major ERP systems such as SAP, Oracle, Microsoft Dynamics, Kinaxis, or Aveva, Plant Managers can embed compliance into the very fabric of their operations.
The result? A manufacturing environment that not only meets regulatory requirements but thrives under them—delivering higher quality, lower risk, and greater agility in an increasingly competitive market.
Are you ready to take your manufacturing operations to the next level? Contact us today to learn more about how PlanetTogether can help you achieve your goals and drive success in your industry.