Hybrid Optimization Algorithms for Job Shop Scheduling
Efficient job shop scheduling is the lifeblood of any manufacturing facility, and chemical manufacturing is no exception. Purchasing Managers in chemical manufacturing facilities understand the critical role scheduling plays in optimizing operations, reducing production costs, and ensuring on-time deliveries. In today's dynamic and competitive industry, where customer demands change frequently, managing resources and schedules effectively is paramount.
In this blog, we will look into the realm of job shop scheduling and explore the integration of advanced scheduling solutions like PlanetTogether with Enterprise Resource Planning (ERP), Supply Chain Management (SCM), and Manufacturing Execution Systems (MES). We will also explore the concept of hybrid optimization algorithms, which can significantly enhance scheduling efficiency, ultimately helping chemical manufacturers meet their production goals and enhance profitability.
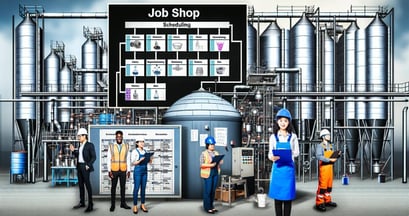
Job Shop Scheduling in Chemical Manufacturing
Chemical manufacturing processes are complex and diverse, with various production lines, equipment, and resources involved. Each production order may require different sets of machines, tools, and materials, making the scheduling process intricate and challenging. Here are some common challenges Purchasing Managers in chemical manufacturing face:
Resource Allocation: Efficiently allocating resources like machines, labor, and materials to multiple production orders can be a daunting task, especially when there are constraints to consider, such as equipment availability and worker shifts.
Changing Priorities: Customer orders and production requirements can change rapidly, necessitating the ability to adapt the schedule on the fly to meet new demands.
Minimizing Downtime: Reducing downtime and idle resources is essential to maximize productivity and profitability.
Meeting Deadlines: Ensuring that production orders are completed on time and delivered to customers according to their specifications is crucial for maintaining customer satisfaction and loyalty.
Resource Optimization: Optimizing the use of resources while minimizing costs and meeting quality standards is a constant challenge.
To address these challenges effectively, chemical manufacturing facilities need sophisticated scheduling tools that can handle complex job shop environments while seamlessly integrating with their existing ERP, SCM, and MES systems.
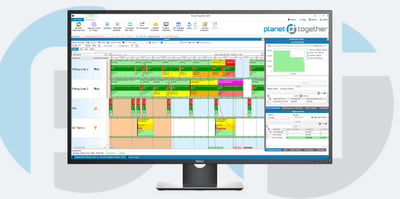
Integration with ERP, SCM, and MES Systems
One of the key strategies for improving job shop scheduling efficiency is integrating advanced scheduling software like PlanetTogether with existing ERP, SCM, and MES systems. Here's how this integration can benefit chemical manufacturing facilities:
Real-Time Data Sync: Integration allows for the seamless exchange of data between scheduling software and other systems, ensuring that the schedule is always based on the most up-to-date information.
Improved Decision-Making: Purchasing Managers can make informed decisions by having access to a comprehensive view of production, inventory, and supply chain data in one place.
Enhanced Communication: Integration fosters better communication between different departments within the organization, leading to improved collaboration and efficiency.
Streamlined Workflows: Scheduling software can automate workflows, reducing manual data entry and errors.
Quick Response to Changes: When customer orders change or equipment breaks down, integrated systems can quickly adjust schedules and resource allocations.
Hybrid Optimization Algorithms: The Future of Job Shop Scheduling
While integration with ERP, SCM, and MES systems is a significant step forward, chemical manufacturers can further improve scheduling efficiency by leveraging advanced optimization algorithms. Hybrid optimization algorithms combine the strengths of different algorithms to find high-quality schedules more effectively than traditional approaches. Here are some key benefits of using hybrid optimization algorithms:
Improved Quality of Solutions: Hybrid algorithms can explore a broader solution space and find better schedules, optimizing both short-term and long-term objectives.
Faster Convergence: They can converge to near-optimal solutions more quickly, reducing the time and computational resources required for scheduling.
Robustness: Hybrid algorithms can handle uncertainties and disruptions better, allowing for more robust schedules that adapt to changing conditions.
Multi-Objective Optimization: They can balance multiple conflicting objectives, such as minimizing production costs and maximizing on-time deliveries.
Customization: Hybrid algorithms can be tailored to meet the specific requirements and constraints of chemical manufacturing facilities.

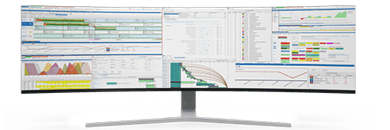
Benefits of Using PlanetTogether with Hybrid Optimization Algorithms
PlanetTogether is a leading advanced scheduling software that offers robust integration capabilities with ERP, SCM, and MES systems. When combined with hybrid optimization algorithms, it becomes a powerful tool for chemical manufacturing facilities. Here's how it can benefit Purchasing Managers and their teams:
Faster Scheduling: PlanetTogether's advanced algorithms and hybrid optimization techniques enable faster and more efficient scheduling, reducing lead times and improving delivery performance.
Resource Optimization: The software optimizes resource utilization, helping to minimize costs and maximize productivity.
What-If Scenarios: Purchasing Managers can explore different scheduling scenarios to make informed decisions and assess the impact of changes before implementing them.
Real-Time Updates: With seamless integration, the schedule is continually updated with real-time data from ERP, SCM, and MES systems, ensuring accuracy and responsiveness.
Enhanced Collaboration: PlanetTogether fosters collaboration between departments by providing a centralized platform for scheduling and communication.
Scalability: The software can scale to accommodate the growth and changing demands of chemical manufacturing facilities.
In the ever-evolving landscape of chemical manufacturing, efficient job shop scheduling is essential for maintaining competitiveness and profitability. Purchasing Managers play a pivotal role in ensuring that resources are optimally allocated, customer demands are met, and costs are minimized. Integrating advanced scheduling software like PlanetTogether with ERP, SCM, and MES systems, along with harnessing the power of hybrid optimization algorithms, can significantly enhance scheduling efficiency.
It's time for chemical manufacturing facilities to embrace these innovations to stay ahead in a highly competitive industry. By doing so, they can streamline operations, improve customer satisfaction, and secure a prosperous future in the world of chemical manufacturing.
Are you ready to take your manufacturing operations to the next level? Contact us today to learn more about how PlanetTogether can help you achieve your goals and drive success in your industry.