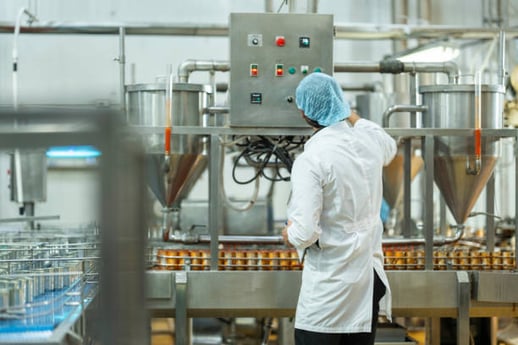
Managing the Supply Chain for Continuous Flow Manufacturing: The Role of APS Integration in Food and Beverage Production
In the dynamic world of food and beverage (F&B) manufacturing, few production models demand the same precision and fluidity as continuous flow manufacturing. Designed to operate with minimal interruptions, continuous flow lines must be tightly synchronized across materials, equipment, labor, and logistics to achieve high efficiency and product consistency. For a production planner in this environment, the challenge lies in aligning the supply chain so that raw materials, packaging, and production capacity are perfectly matched — avoiding costly stoppages or waste.
This is where advanced planning and scheduling (APS) tools, like PlanetTogether APS, play a transformative role. Especially when integrated with enterprise systems such as SAP, Oracle, Microsoft Dynamics, Kinaxis, or Aveva, PlanetTogether empowers production planners to orchestrate supply chain operations with real-time agility, predictive insight, and optimal coordination.
Let’s explore how production planners in F&B manufacturing can leverage APS integration to master the complexities of managing a supply chain for continuous flow operations.
Understanding Continuous Flow Manufacturing in F&B
Continuous flow manufacturing is a production approach where products move through the manufacturing process without significant stops or delays between stages. Common in industries such as beverage bottling, dairy processing, snack food production, and brewing, continuous flow lines prioritize:
High throughput
Consistent product quality
Minimized inventory and storage needs
Reduced changeovers and downtime
While the rewards of this approach are substantial, so are the risks. A single disruption in the supply chain — whether from late raw material deliveries, equipment malfunctions, or labor shortages — can cause cascading production halts. For F&B products, where shelf life and freshness are critical, even minor delays can result in spoilage, customer dissatisfaction, or lost revenue.
To manage these risks, production planners must synchronize supply chain flows with exceptional accuracy.
Challenges of Supply Chain Synchronization in Continuous Flow
The key challenge is that continuous flow lines don’t leave room for error. Production planners must handle several critical factors simultaneously:
Raw Material Availability: Ingredients like milk, grains, sugar, or flavorings must be available just-in-time, neither too early (which risks spoilage) nor too late (which risks halting production).
Packaging Coordination: Materials such as bottles, cartons, or pouches must match the pace of production to avoid bottlenecks.
Equipment and Labor Scheduling: Machines and staff need to be scheduled for seamless operation, with preventive maintenance windows and shift changes carefully planned.
Demand Fluctuations: Sales and distribution forecasts must be aligned with production capacity, especially for promotional runs or seasonal spikes.
Relying solely on spreadsheets or disconnected systems makes it almost impossible to optimize these variables simultaneously. That’s why APS platforms, like PlanetTogether, have become indispensable.
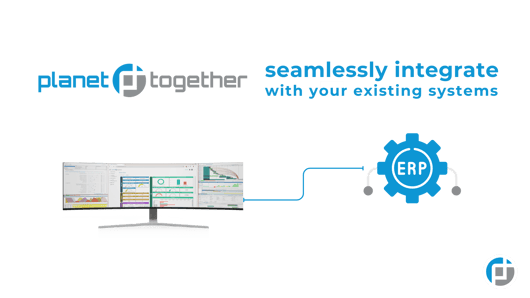
How APS Integration Improves Supply Chain Management
PlanetTogether APS, when integrated with ERP or supply chain management platforms such as SAP, Oracle, Microsoft, Kinaxis, or Aveva, creates a unified digital planning environment. This integration offers several advantages:
Real-Time Data Visibility
Through ERP integration, PlanetTogether APS can pull live data on inventory levels, production orders, supplier statuses, and customer demand. Instead of planning based on outdated or static reports, production planners can work with real-time insights, allowing faster and more accurate decisions.
For example, if an incoming shipment of fruit puree is delayed, PlanetTogether can automatically adjust production schedules or suggest alternative runs that don’t rely on the missing material — minimizing line downtime.
Advanced Scheduling and Optimization
APS platforms are designed to run powerful optimization algorithms. For continuous flow manufacturing, this means they can:
Balance line capacities across multiple plants.
Sequence production runs to minimize changeover times.
Prioritize high-margin or urgent orders.
Align raw material delivery schedules with production timing.
With ERP integration, the APS tool doesn’t just operate in a silo — it aligns its optimizations with the broader business context, such as sales priorities, supplier contracts, or logistics constraints.
Predictive Analytics for Risk Mitigation
Predictive features allow production planners to simulate “what-if” scenarios. For example, what happens if supplier lead times increase by three days? Or if a particular machine goes offline for maintenance? Integrated APS systems can model these disruptions and provide actionable recommendations, helping planners proactively mitigate risks.
For F&B manufacturers, where perishable goods create added urgency, these predictive capabilities can mean the difference between meeting delivery commitments and losing a major retail contract.
Enhanced Collaboration Across Teams
By integrating PlanetTogether with platforms like Microsoft Dynamics or SAP, production planning becomes a cross-functional effort. Sales teams, procurement, logistics, and manufacturing can all access the same synchronized plan, reducing miscommunications and improving alignment.
Imagine the benefit when procurement can see precisely when each ingredient is needed, or when logistics can align delivery routes with production schedules. This unified planning ecosystem helps break down silos and improve overall supply chain agility.
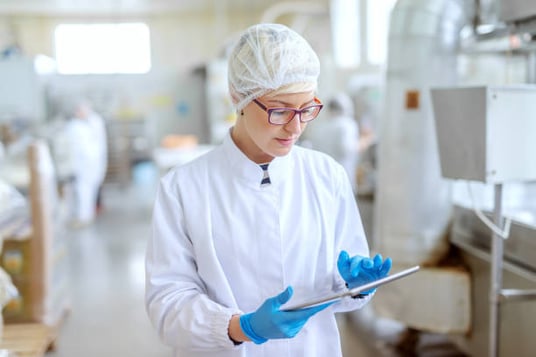
Best Practices for Production Planners
For F&B production planners looking to harness the power of APS integration, here are some best practices:
Invest in Clean Data: Ensure that ERP and supply chain systems are providing accurate, up-to-date data. Poor data quality limits the effectiveness of any APS tool.
Align Cross-Functional Goals: Work closely with procurement, sales, and logistics to define shared priorities and constraints.
Use Predictive Features Actively: Go beyond reactive planning — leverage “what-if” simulations to prepare for supply chain risks proactively.
Focus on Continuous Improvement: Treat the APS implementation as an evolving process. Regularly review system recommendations, actual performance, and optimization opportunities.
Continuous flow manufacturing in the food and beverage sector offers major advantages — but only when supply chains are finely tuned to keep pace. For production planners, managing this complexity requires more than just experience and intuition; it demands digital tools that provide real-time visibility, predictive power, and optimization intelligence.
By integrating PlanetTogether APS with enterprise platforms like SAP, Oracle, Microsoft, Kinaxis, or Aveva, F&B manufacturers can transform their supply chain management approach. The result? Smarter planning, more resilient operations, and a stronger competitive edge in a fast-moving industry.
Are you ready to take your manufacturing operations to the next level? Contact us today to learn more about how PlanetTogether can help you achieve your goals and drive success in your industry.