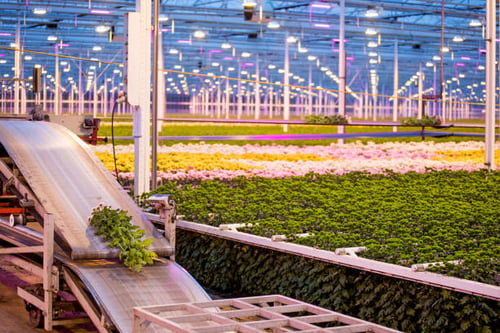
Mastering Multi-Plant Coordination: How APS-Driven Production Planning Optimizes Food & Beverage Networks
The Complexity of Multi-Plant Operations
In food and beverage manufacturing, Operations Directors are constantly balancing product freshness, regulatory compliance, and cost efficiency. Managing production in a single facility is already a challenge—doing so across a multi-plant network introduces another level of complexity. Synchronizing schedules, balancing loads, sharing inventories, and adapting to changing demand in real-time requires more than spreadsheets or standalone tools.
That’s where Advanced Planning and Scheduling (APS) systems, such as PlanetTogether, come into play—especially when integrated with ERP giants like SAP, Oracle, Microsoft Dynamics, Kinaxis, or Aveva. By embedding APS capabilities into a unified data and execution ecosystem, Operations Directors gain real-time insights and control over the entire production network.
This blog explores how APS-driven production planning transforms multi-plant food and beverage manufacturing, enabling better agility, cost savings, and responsiveness in a volatile market.

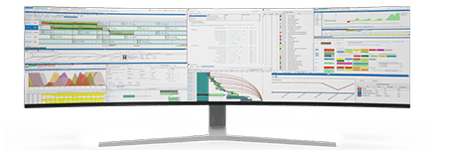
The Need for APS in Multi-Plant Food & Beverage Manufacturing
Short Shelf Lives and High Demand Variability
Food and beverage products often have limited shelf lives, meaning production and distribution must align precisely with demand to avoid waste or shortages. Multi-plant networks compound this challenge, especially when demand surges vary by region, season, or promotion.
APS systems optimize production schedules based on perishability, freshness requirements, and logistical constraints—ensuring the right products are produced at the right plants and shipped on time.
Redundant and Siloed Planning Systems
In many organizations, each facility uses separate planning tools or disconnected spreadsheets. This results in:
Suboptimal resource utilization
High inventory holding costs
Inconsistent performance tracking
With PlanetTogether APS, companies gain a centralized scheduling engine that evaluates constraints and capacities across all facilities. When integrated with systems like Oracle NetSuite or SAP S/4HANA, planners can access real-time data, enabling faster, network-wide decisions.

Key Benefits of APS-Driven Production Planning in a Multi-Plant Environment
Centralized Visibility with Distributed Execution
APS enables centralized planning while allowing local teams to execute autonomously. Through dynamic dashboards, planners can view:
Machine availability across plants
Shift patterns
Inventory levels
Customer demand forecasts
For example, if Plant A is overburdened and Plant B has available capacity, the system can automatically redistribute workloads based on constraints, transit time, or raw material availability.
Scenario Planning and What-If Analysis
Using APS, Operations Directors can simulate scenarios such as:
A plant shutdown due to contamination
Surge in demand due to a marketing campaign
Supplier disruption impacting ingredient delivery
PlanetTogether allows users to run “what-if” simulations and instantly view downstream impacts on production and delivery schedules. This ability, when connected to a Microsoft Dynamics 365 system, empowers rapid decision-making.
Real-Time Data Integration with ERP and MES
To make accurate and actionable decisions, APS needs to be tightly integrated with ERP and MES platforms. For instance:
SAP provides master data, production orders, and BOMs.
Aveva MES offers real-time shop floor execution data.
PlanetTogether APS aligns this information to ensure schedules are based on actual capabilities and constraints.
Such interoperability eliminates planning blind spots and enhances alignment between corporate strategy and plant-level execution.
Core Features of APS in Multi-Plant Networks
Finite Capacity Scheduling
APS considers actual production limits, machine availability, labor shifts, and raw material constraints. This is critical in food & beverage where overbooking equipment can result in hygiene risks, cleaning schedule violations, or production delays.
Inventory Synchronization
With integrated APS-ERP systems, real-time inventory data helps avoid:
Overstocking at one plant while another runs short
Expired goods due to poor FIFO practices
Unnecessary rush orders or inter-facility transfers
PlanetTogether, when connected with Kinaxis RapidResponse, enhances visibility across inbound supply chains, ensuring production plans are grounded in feasible material availability.
Inter-Plant Production Rebalancing
When one plant experiences downtime or bottlenecks, APS can reassign production orders to other facilities in the network. This flexibility:
Increases overall throughput
Reduces overtime and labor costs
Minimizes late deliveries
Best Practices for Implementation
Start with Data Alignment
APS solutions are only as good as the data they consume. Before integration, ensure that:
Master data (items, routings, work centers) is standardized across ERP and MES
Historical demand, lead times, and performance metrics are clean and consistent
Interfaces between systems are robust and scalable
Map Out Inter-Plant Dependencies
Document how plants share:
Raw materials or semi-finished goods
Labor pools or mobile teams
Quality control processes
PlanetTogether can then reflect these interdependencies during optimization, avoiding conflicting schedules or duplicated efforts.
Engage Stakeholders Across the Network
Engage not just central planners, but also site-level managers, procurement leads, and logistics coordinators. Training each stakeholder on how APS informs their part of the operation fosters adoption and consistency in decision-making.
Prioritize Quick Wins
Focus on high-impact areas first—such as seasonal SKUs, perishable items, or bottleneck equipment. Success here builds momentum for wider rollouts.
Driving Agility and Profitability with APS
The food and beverage industry operates in one of the most dynamic and demanding supply chains today. Multi-plant operations must deliver on freshness, efficiency, and responsiveness simultaneously. Traditional planning tools simply can’t keep pace.
By implementing PlanetTogether APS integrated with robust ERP and MES platforms like SAP, Oracle, Microsoft Dynamics, Kinaxis, or Aveva, Operations Directors gain the visibility, control, and agility needed to manage modern production networks.
APS doesn’t just enhance scheduling—it transforms how organizations think about manufacturing agility, unlocking better profitability and resilience across the board.
Looking to modernize your multi-plant production planning strategy?
Explore how PlanetTogether APS can integrate with your current ERP or MES environment to create a synchronized, efficient, and future-ready production network. Contact us today for a tailored demo.