Resource Utilization in Industrial Manufacturing with Deep Reinforcement Learning
Operations directors face a myriad of challenges in optimizing resource utilization while maintaining sustainability in industrial manufacturing. Traditional approaches often fall short in adapting to the complexities of modern manufacturing environments. However, emerging technologies like deep reinforcement learning (DRL) offer a promising solution to this dilemma.
In this blog, we look into the realm of deep reinforcement learning and its application in industrial manufacturing, particularly focusing on how it integrates with existing Enterprise Resource Planning (ERP), Supply Chain Management (SCM), and Manufacturing Execution Systems (MES) such as SAP, Oracle, Microsoft, Kinaxis, Aveva, and others. We'll explore how DRL empowers operations directors to achieve sustainable and efficient resource utilization.
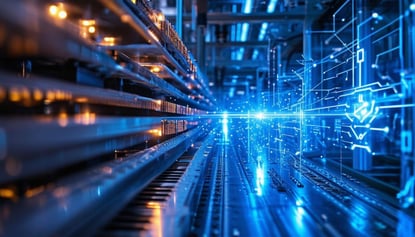
Deep Reinforcement Learning
Deep reinforcement learning represents a subset of machine learning where an agent learns to interact with an environment to achieve a specific goal by maximizing cumulative rewards. Unlike traditional machine learning algorithms, DRL enables autonomous decision-making through trial and error, mimicking human-like learning processes.
In the context of industrial manufacturing, DRL enables machines to make real-time decisions regarding resource allocation, production scheduling, and energy consumption. By continuously learning from feedback, DRL algorithms optimize operations for efficiency and sustainability.
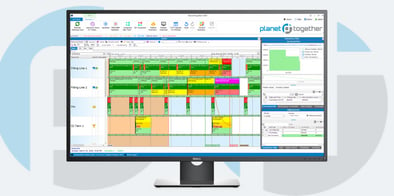
Integration with ERP, SCM, and MES Systems
The seamless integration of DRL with ERP, SCM, and MES systems is paramount for unlocking its full potential in industrial manufacturing. Platforms like PlanetTogether serve as the bridge between DRL algorithms and existing operational frameworks, facilitating data exchange and decision-making.
SAP Integration: SAP's comprehensive suite of ERP solutions plays a vital role in managing manufacturing processes. By integrating DRL algorithms with SAP, operations directors gain insights into real-time production data, enabling dynamic decision-making for resource utilization and scheduling.
Oracle Integration: Oracle's SCM solutions provide visibility and control across the supply chain. Through integration with DRL, operations directors can optimize inventory levels, streamline logistics, and enhance production planning to minimize waste and maximize resource utilization.
Microsoft Integration: Microsoft's MES systems offer advanced functionalities for shop floor management. By integrating DRL with Microsoft platforms, operations directors can optimize production workflows, reduce downtime, and improve resource allocation to achieve sustainable operations.
Kinaxis Integration: Kinaxis specializes in cloud-based SCM and S&OP solutions. Integration with DRL empowers operations directors to leverage predictive analytics and scenario planning for optimal resource utilization, ensuring alignment between supply and demand.
Aveva Integration: Aveva's MES solutions enable real-time monitoring and control of manufacturing processes. By integrating DRL with Aveva platforms, operations directors can optimize equipment utilization, minimize energy consumption, and reduce environmental impact.
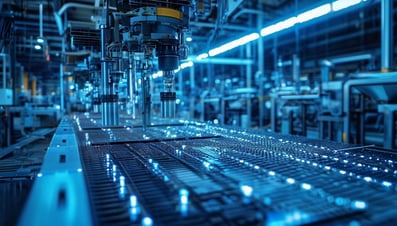
The Benefits of Deep Reinforcement Learning for Sustainable Resource Utilization
Now, let's explore the tangible benefits that DRL brings to industrial manufacturing operations:
Optimized Production Scheduling: DRL algorithms continuously learn and adapt to changing production dynamics, enabling operations directors to optimize production schedules for maximum efficiency and minimal resource waste.
Dynamic Resource Allocation: By integrating with ERP, SCM, and MES systems, DRL empowers operations directors to dynamically allocate resources such as raw materials, labor, and equipment based on real-time demand and supply fluctuations.
Energy Efficiency: DRL algorithms can optimize energy consumption by identifying patterns and inefficiencies in manufacturing processes. By minimizing energy usage, operations directors can reduce costs and environmental impact simultaneously.
Waste Reduction: Through proactive decision-making, DRL helps minimize waste generation across the production lifecycle. By optimizing inventory levels, production workflows, and logistics, operations directors can achieve significant reductions in material waste.
Continuous Improvement: One of the key strengths of DRL is its ability to learn from experience and adapt over time. By continuously optimizing operations based on feedback and performance data, operations directors can drive ongoing improvements in resource utilization and sustainability.
Deep reinforcement learning represents a transformative technology for achieving sustainable resource utilization in industrial manufacturing. By seamlessly integrating PlanetTogether serve as the bridge between DRL algorithms and existing operational frameworks, facilitating data exchange and decision-making with ERP, SCM, and MES systems, DRL empowers operations directors to optimize production processes, minimize waste, and reduce environmental impact.
As the manufacturing landscape continues to evolve, embracing DRL offers a competitive advantage in driving operational excellence and sustainability. By harnessing the power of artificial intelligence and data-driven decision-making, operations directors can lead their organizations towards a more efficient, resilient, and environmentally conscious future.
Are you ready to take your manufacturing operations to the next level? Contact us today to learn more about how PlanetTogether can help you achieve your goals and drive success in your industry.