Adaptive Manufacturing for Custom or Low-Volume Production
The need for adaptive manufacturing solutions has never been more critical, especially when it comes to custom or low-volume production. As a Production Scheduler, you're at the forefront of orchestrating operations amidst fluctuating demands, intricate supply chains, and evolving customer preferences.
In this blog, we'll look into the realm of adaptive manufacturing, exploring how integration between advanced planning tools like PlanetTogether and leading ERP, SCM, and MES systems can revolutionize operations, streamline processes, and drive success in the face of complexity.
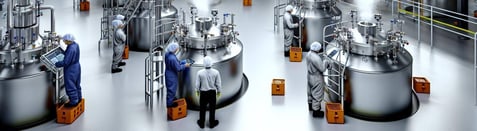
Understanding the Challenges
Custom or low-volume production presents a unique set of challenges. Unlike mass production, where predictability and economies of scale reign supreme, the variability and uncertainty inherent in custom or low-volume orders require a different approach. Production schedulers often find themselves grappling with:
Fluctuating Demand: Demand for custom or low-volume products can vary significantly, making it challenging to forecast accurately.
Complex Supply Chains: Chemical manufacturing involves intricate supply chains with multiple stakeholders, making coordination and synchronization a daunting task.
Limited Margins for Error: With tighter profit margins and higher costs associated with customization, there's little room for inefficiencies or mistakes in production scheduling.
Rapid Changeovers: Frequent changeovers between different product variants can lead to downtime and increased setup costs, impacting productivity and profitability.
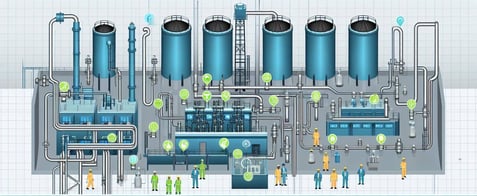
The Role of Adaptive Manufacturing
Adaptive manufacturing is the answer to these challenges. It's about agility, flexibility, and responsiveness, enabling manufacturers to swiftly adapt to changing demands and market conditions. At its core, adaptive manufacturing empowers production schedulers to:
Anticipate Demand: By leveraging advanced forecasting techniques and real-time data analytics, production schedulers can gain deeper insights into demand patterns, allowing for proactive planning and resource allocation.
Optimize Operations: Adaptive manufacturing enables the optimization of production processes, from inventory management and resource utilization to scheduling and sequencing, maximizing efficiency and minimizing waste.
Enhance Collaboration: Seamless integration between planning tools like PlanetTogether and ERP, SCM, and MES systems fosters collaboration across departments and stakeholders, ensuring alignment and coherence in decision-making.
Enable Quick Changeovers: Through effective scheduling and setup reduction techniques, adaptive manufacturing facilitates rapid changeovers between different product configurations, reducing downtime and enhancing productivity.

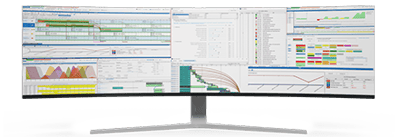
Integration for Seamless Operations
Key to unlocking the full potential of adaptive manufacturing is integration between advanced planning tools and enterprise systems. Among the leading solutions in this domain are SAP, Oracle, Microsoft, Kinaxis, Aveva, and others. By integrating PlanetTogether with these systems, production schedulers can harness the power of:
Real-Time Data Exchange: Integration enables the seamless flow of data between planning, execution, and control systems, providing production schedulers with up-to-date information for informed decision-making.
Unified Planning Environment: A unified planning environment consolidates disparate data sources into a single platform, eliminating silos and enabling holistic visibility across the manufacturing ecosystem.
Automated Workflows: Integration allows for the automation of repetitive tasks and processes, reducing manual effort and minimizing the risk of errors or delays.
Scenario Planning and What-If Analysis: With integrated planning tools, production schedulers can conduct scenario planning and what-if analysis, simulating various production scenarios and evaluating their impact on key metrics such as cost, lead time, and resource utilization.
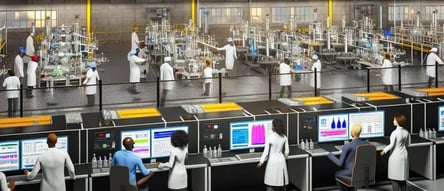
Best Practices for Implementation
To successfully implement adaptive manufacturing in your chemical manufacturing facility, consider the following best practices:
Define Clear Objectives: Clearly define your goals and objectives for adopting adaptive manufacturing, whether it's reducing lead times, optimizing resource utilization, or improving customer satisfaction.
Engage Stakeholders: Involve key stakeholders from across the organization in the planning and implementation process to ensure buy-in and alignment of priorities.
Invest in Training and Education: Provide comprehensive training and education to your team on the use of advanced planning tools and integrated systems to maximize adoption and effectiveness.
Continuous Improvement: Adaptive manufacturing is an ongoing journey. Continuously monitor performance metrics, gather feedback, and iterate on your processes to drive continuous improvement and stay ahead of the curve.
In an era defined by volatility, uncertainty, complexity, and ambiguity (VUCA), adaptive manufacturing emerges as a beacon of resilience and competitiveness for chemical manufacturers engaged in custom or low-volume production. By leveraging advanced planning tools like PlanetTogether and integrating them with leading ERP, SCM, and MES systems, production schedulers can navigate the complexities of modern manufacturing with confidence, agility, and efficiency.
Embrace the paradigm shift towards adaptive manufacturing, and unlock new possibilities for growth, innovation, and success in the ever-evolving landscape of chemical manufacturing. Are you ready to take your manufacturing operations to the next level? Contact us today to learn more about how PlanetTogether can help you achieve your goals and drive success in your industry.