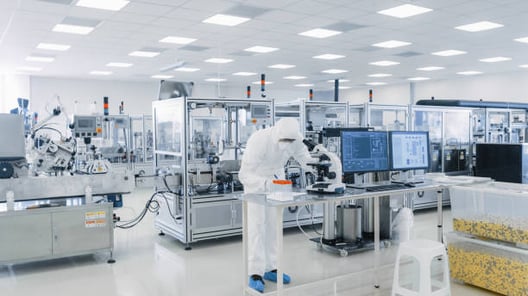
Optimizing Cross-Facility Workloads in Medical Manufacturing: The Power of APS Integration
In medical manufacturing, the pressure on Plant Managers is immense. From maintaining stringent quality standards to managing fluctuating demand for specialized medical devices or pharmaceutical products, every decision impacts efficiency, cost, and compliance. For facilities operating across multiple sites, the challenge grows even larger: how can you balance workloads, synchronize production, and make sure every plant contributes optimally to the overall business goals?
This is where cross-facility workload optimization comes into play — and where advanced planning and scheduling (APS) systems like PlanetTogether, integrated with enterprise solutions such as SAP, Oracle, Microsoft Dynamics, Kinaxis, or Aveva, make a decisive difference.
Let’s explore how these integrated solutions help Plant Managers like you balance resources across facilities, improve production throughput, and elevate operational performance in medical manufacturing.
The Cross-Facility Challenge in Medical Manufacturing
Medical manufacturing is not a “one-plant game.” Companies often operate multiple facilities across regions to meet regulatory requirements, mitigate risks, serve local markets, or specialize in different product lines (for example, one plant for surgical equipment, another for implantable devices, and yet another for diagnostic tools).
However, coordinating these facilities is complex:
Production capacities vary. One site may have surplus capacity, while another struggles with overload.
Different regulations and compliance standards apply depending on location, particularly for export products.
Lead times and inventory requirements differ, especially for customized or made-to-order medical devices.
Unexpected disruptions (machine downtime, raw material shortages, or labor constraints) can affect one plant, impacting the whole network.
Without a centralized, optimized approach, Plant Managers are left juggling spreadsheets, emails, and siloed systems — often leading to inefficiencies, unnecessary overtime, stockouts, or even compliance risks.
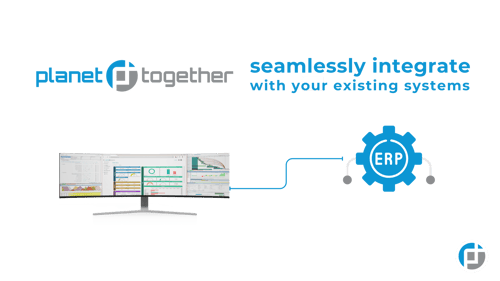
APS + ERP Integration: A Unified View Across Facilities
This is where advanced planning and scheduling (APS) tools, like PlanetTogether, become indispensable.
PlanetTogether APS offers real-time, data-driven planning capabilities that go beyond a single plant. When integrated with ERP systems like SAP, Oracle, Microsoft Dynamics, Kinaxis, or Aveva, it provides a unified platform that connects production, inventory, supply chain, and resource data across all sites.
Key advantages of integrating PlanetTogether APS with your ERP system include:
Centralized visibility: See capacity, workloads, and bottlenecks across all facilities in one dashboard.
Dynamic load balancing: Shift production loads between plants based on real-time data — for example, moving a high-priority order to a less busy site.
Coordinated scheduling: Align multi-site production schedules to maximize throughput and meet customer deadlines.
Shared resource management: Optimize the use of shared materials, tools, or specialized labor across sites.
Better scenario planning: Run “what-if” analyses across your whole network, not just one plant, to prepare for disruptions or sudden demand spikes.
This integration removes the blind spots between sites, transforming multi-facility operations from isolated silos into a synchronized, high-performance network.
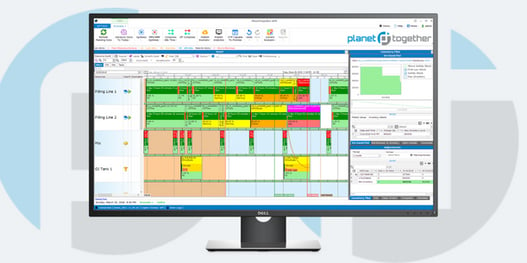
Practical Applications: How Plant Managers Optimize Across Facilities
Let’s break this down into tangible use cases.
Load Shifting to Avoid Bottlenecks
Suppose your primary site for assembling orthopedic implants faces an unexpected machine failure. Without integrated APS, the Plant Manager is stuck — orders back up, customer commitments are jeopardized, and your reputation takes a hit.
With PlanetTogether APS integrated into your ERP, you can immediately see which secondary plant has available capacity. The system can recommend load shifting, ensuring that critical work moves to another site with minimal delay. You maintain delivery commitments, minimize downtime costs, and keep your production network agile.
Synchronizing Production for Complex Supply Chains
In medical manufacturing, some components (like microelectronics or coated materials) are produced at one site and shipped to another for final assembly. Any delay or mismatch in production timing can throw off the entire delivery schedule.
By integrating PlanetTogether APS with systems like Kinaxis or SAP, you gain synchronized planning that accounts for upstream and downstream tasks across facilities. You can ensure that semi-finished goods are ready when needed and avoid idle time or emergency shipments, saving both time and money.
Prioritizing High-Margin or High-Urgency Orders
Not all orders are created equal. When a high-margin, time-sensitive custom device order comes in, you want to prioritize it across the network.
With APS-ERP integration, you can quickly identify which plant can fast-track the order without disrupting other commitments. You can dynamically reallocate resources, reprioritize schedules, and ensure that strategic orders receive the attention they need, no matter where they originate.
Coordinating Shared Resources and Expertise
Some resources — like specialized coating equipment or quality inspection teams — may be shared across sites. Without centralized planning, you risk double-booking or under-utilizing these critical assets.
PlanetTogether APS enables optimized scheduling of shared resources, ensuring the right equipment and expertise are available where and when needed, maximizing utilization and reducing bottlenecks.
The Integration Payoff: Strategic Benefits for Plant Managers
By combining the predictive power of PlanetTogether APS with the transactional strength of SAP, Oracle, Microsoft Dynamics, Kinaxis, or Aveva, Plant Managers unlock strategic benefits that go far beyond operational gains:
Greater agility: Rapidly adapt to shifting demands, regulations, or disruptions across facilities.
Cost efficiency: Reduce overtime, avoid unnecessary capital investments, and minimize waste by balancing workloads intelligently.
Better performance metrics: Improve on-time delivery rates, overall equipment effectiveness (OEE), and customer satisfaction.
Enhanced compliance and traceability: Maintain regulatory compliance across all plants with centralized data tracking and reporting.
Scalable growth: Confidently expand operations, knowing you can orchestrate multi-site workloads effectively.
For Plant Managers in medical manufacturing, the future belongs to those who can orchestrate complex, multi-site operations with precision. With the right APS-ERP integration, you can transform cross-facility workloads from a constant juggling act into a streamlined, data-driven powerhouse.
PlanetTogether, working seamlessly with enterprise systems like SAP, Oracle, Microsoft Dynamics, Kinaxis, or Aveva, empowers you to lead with agility, efficiency, and confidence — ensuring that every plant in your network delivers its best, every day.
Are you ready to take your manufacturing operations to the next level? Contact us today to learn more about how PlanetTogether can help you achieve your goals and drive success in your industry.