Material Availability and Allocation
In the world of pharmaceutical manufacturing, ensuring material availability and efficient allocation is essential for meeting production demands, maintaining quality standards, and ultimately, delivering life-saving medications to patients worldwide. As an Operations Director, you're well aware of the complexities involved in managing materials across the supply chain while adhering to stringent regulatory requirements.
In this blog, we'll explore the critical importance of material availability and allocation in pharmaceutical manufacturing and delve into how integrating advanced planning systems like PlanetTogether with ERP, SCM, and MES platforms such as SAP, Oracle, Microsoft, Kinaxis, and Aveva can streamline operations, enhance visibility, and drive better decision-making.
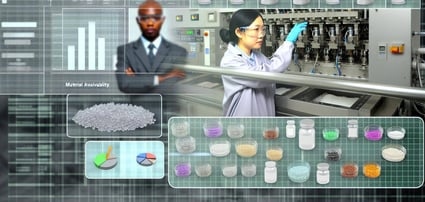
The Significance of Material Availability and Allocation
Material availability and allocation play a pivotal role in the entire pharmaceutical manufacturing process. From raw materials to intermediates and finished products, every component must be sourced, managed, and allocated efficiently to ensure uninterrupted production cycles. Any disruptions or delays in material availability can lead to production bottlenecks, increased costs, and ultimately, impact patient access to vital medications.
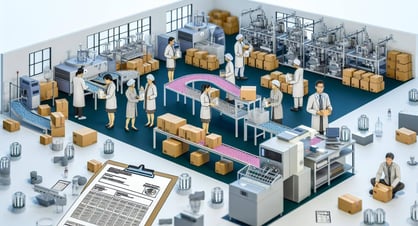
Challenges in Material Management
Pharmaceutical manufacturing faces unique challenges in material management, including:
Regulatory Compliance: Strict regulatory standards govern the sourcing, handling, and storage of pharmaceutical materials. Non-compliance can result in severe consequences, including product recalls and legal penalties.
Supply Chain Complexity: Pharmaceutical supply chains are often global and involve multiple stakeholders, making it challenging to track and manage materials effectively.
Demand Volatility: Fluctuations in demand, driven by factors such as market dynamics and healthcare trends, can impact material requirements and allocation strategies.
Inventory Optimization: Balancing inventory levels to meet demand while minimizing excess stock is a delicate balancing act that requires accurate demand forecasting and inventory planning.
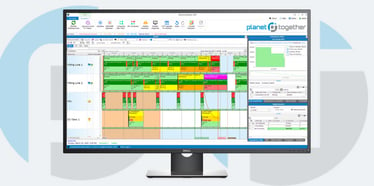
Integrating Planning Systems for Enhanced Material Management
To address these challenges and optimize material availability and allocation, pharmaceutical manufacturers are turning to integrated planning systems that seamlessly connect with ERP, SCM, and MES platforms. One such solution is the integration between PlanetTogether and leading enterprise systems like SAP, Oracle, Microsoft, Kinaxis, and Aveva.
Here's how this integration can revolutionize material management:
Real-Time Visibility: By integrating planning systems with ERP, SCM, and MES platforms, Operations Directors gain real-time visibility into inventory levels, production schedules, and material requirements across the supply chain. This visibility enables proactive decision-making and better allocation of resources.
Demand Forecasting: Advanced planning systems leverage data analytics and machine learning algorithms to forecast demand accurately. By analyzing historical data, market trends, and other variables, these systems can predict future demand patterns and adjust material procurement and allocation accordingly.
Optimized Production Planning: Integration between planning systems and enterprise platforms enables synchronized production planning. Production schedules can be dynamically adjusted based on material availability, equipment capacity, and resource constraints, ensuring optimal use of resources and minimizing production downtime.
Efficient Order Fulfillment: With real-time insights into material availability and production schedules, pharmaceutical manufacturers can prioritize and expedite order fulfillment. By allocating materials based on criticality and demand urgency, companies can enhance customer satisfaction and loyalty.
Compliance Management: Integrated planning systems streamline compliance management by automating documentation, audit trails, and regulatory reporting. By maintaining accurate records and ensuring adherence to regulatory standards, pharmaceutical manufacturers can mitigate compliance risks and maintain product quality and safety.
In the competitive landscape of pharmaceutical manufacturing, material availability and allocation are critical factors that can significantly impact operational efficiency, product quality, and customer satisfaction. By leveraging integrated planning systems like PlanetTogether in conjunction with leading ERP, SCM, and MES platforms, Operations Directors can optimize material management processes, enhance visibility across the supply chain, and drive better decision-making.
As you continue to navigate the complexities of pharmaceutical manufacturing, consider the transformative potential of integrated planning systems in addressing the challenges of material availability and allocation, ultimately enabling your organization to achieve its goals of delivering safe, effective medications to patients worldwide.
Are you ready to take your manufacturing operations to the next level? Contact us today to learn more about how PlanetTogether can help you achieve your goals and drive success in your industry.