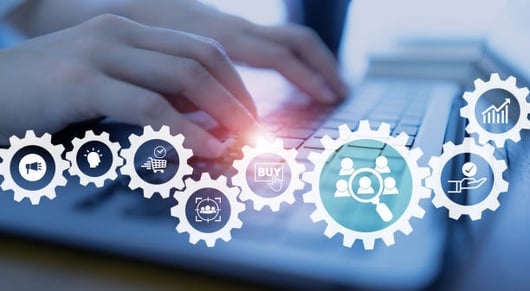
Optimizing the Procurement Cycle in Food and Beverage Manufacturing: How APS and ERP Integration Elevates Purchasing Performance
In the competitive world of food and beverage (F&B) manufacturing, the procurement cycle is not just about placing orders — it’s about orchestrating a seamless flow of raw materials, packaging components, and indirect supplies that align with tight production timelines, quality requirements, and cost targets. For a Purchasing Manager, this cycle can feel like navigating a maze of supplier relationships, fluctuating demand, regulatory considerations, and operational constraints.
Fortunately, advanced tools like PlanetTogether Advanced Planning and Scheduling (APS), when integrated with major ERP systems such as SAP, Oracle, Microsoft Dynamics, Kinaxis, or Aveva, can transform procurement from a reactive process into a proactive, data-driven strategic function.
This blog explores how modern APS-ERP integration reshapes the procurement cycle in F&B manufacturing, enabling Purchasing Managers to make better decisions, streamline workflows, and deliver value across the supply chain.
What Is the Procurement Cycle?
At its core, the procurement cycle in F&B manufacturing covers the end-to-end process of acquiring goods and services necessary for production. This includes:
Identifying needs (raw materials, ingredients, packaging, equipment)
Sourcing suppliers and gathering quotes
Negotiating contracts and securing the best terms
Placing purchase orders (POs) and ensuring supplier confirmations
Coordinating inbound logistics
Receiving and inspecting materials
Processing payments and closing the procurement loop
While the steps seem straightforward, the reality is far more complex. Seasonal demand shifts, volatile commodity prices, tight production windows, food safety regulations, and sustainability goals all converge, demanding agile procurement strategies.
Key Procurement Challenges in F&B Manufacturing
As a Purchasing Manager, you’re likely familiar with the pain points that can disrupt procurement cycles:
Demand variability: Promotions, new product launches, and changing consumer preferences create unpredictable demand patterns.
Perishable inputs: Ingredients and raw materials often have limited shelf life, leaving little room for inventory errors.
Supplier reliability: A single late delivery or quality issue can stall entire production runs.
Compliance and traceability: Food safety standards (e.g., FSMA, HACCP) require rigorous documentation and supplier certifications.
Cost pressures: Volatile input costs demand careful negotiation and cost-saving initiatives.
These factors make it clear: manual tracking, siloed systems, and spreadsheets are no longer sufficient. This is where APS and ERP integration comes into play.
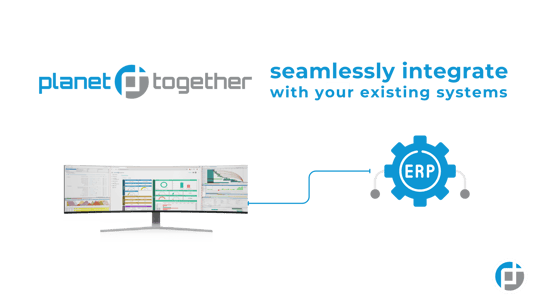
How APS and ERP Integration Transforms Procurement
PlanetTogether APS provides advanced scheduling and optimization capabilities, but when tightly integrated with your ERP system (such as SAP, Oracle, Microsoft, Kinaxis, or Aveva), it unlocks a new level of visibility and control over procurement processes.
Here’s how integration elevates each stage of the procurement cycle:
Accurate Demand Signals
Traditional procurement relies on historical data or static forecasts, often leading to overordering or stockouts. With APS integration, Purchasing Managers gain real-time demand signals from the production floor, including updated production schedules, capacity constraints, and priority orders.
For example, if PlanetTogether APS dynamically reschedules a production line due to an equipment issue or rush order, that change immediately flows back into the ERP system, adjusting material requirements and triggering timely purchase orders. This synchronization ensures procurement stays aligned with actual production needs, not outdated forecasts.
Smarter Supplier Collaboration
APS-ERP integration enables better collaboration with suppliers through data-driven purchase planning. Instead of batch ordering at fixed intervals, you can generate purchase orders aligned with optimized production plans, reducing inventory carrying costs while ensuring timely delivery.
Some systems even allow suppliers to view portions of the production plan, improving coordination and reducing lead times. For example, if Microsoft Dynamics integrates with PlanetTogether APS, suppliers can anticipate when orders will spike due to seasonal promotions or new product introductions.
Enhanced Inventory Management
Overstocking perishable goods can lead to waste, while understocking causes costly production halts. APS-driven scheduling gives you real-time inventory projections that consider both current stock levels and future production needs.
Through SAP integration, for example, APS can highlight when safety stocks are at risk, when to expedite orders, or when to adjust purchase quantities to avoid spoilage. This balance improves service levels while reducing waste and excess.
Improved Cost and Risk Management
With APS-ERP integration, Purchasing Managers gain better visibility into cost drivers and supply risks. You can simulate different scenarios — such as changing suppliers, adjusting order frequencies, or shifting production schedules — to understand their impact on procurement costs and timelines.
For instance, by using Kinaxis RapidResponse alongside PlanetTogether APS, you can model how a raw material price increase or supplier disruption will ripple through the production plan and adjust procurement strategies proactively.
Streamlined Approvals and Workflows
Integrated APS and ERP systems streamline approval workflows by reducing manual interventions. For example, purchase requisitions generated from APS-optimized plans can automatically flow through ERP approval hierarchies, ensuring faster PO creation and less bottlenecking.
This automation is particularly valuable for high-volume or repetitive purchases, freeing up Purchasing Managers to focus on strategic sourcing and supplier development.
Data-Driven Sustainability and Compliance
Sustainability is no longer a “nice to have” — it’s a business imperative. APS-ERP integration provides transparent tracking of supplier certifications, sourcing practices, and environmental impact.
With Aveva integration, for example, manufacturers can ensure procurement decisions align with ESG (Environmental, Social, Governance) goals, such as selecting local suppliers to reduce carbon footprint or sourcing ethically certified ingredients.
Best Practices for Purchasing Managers
To fully leverage the power of APS-ERP integration, consider these best practices:
Collaborate with Production and Planning Teams: Stay closely aligned with planners and schedulers to understand shifting production priorities.
Prioritize Supplier Relationships: Use APS insights to engage in strategic, not just transactional, supplier interactions.
Invest in System Integration: Ensure PlanetTogether APS is fully integrated with your ERP, avoiding data silos and manual reconciliations.
Leverage Scenario Planning: Use APS to run “what-if” analyses to improve procurement agility and resilience.
Focus on Continuous Improvement: Regularly review procurement KPIs and use system data to identify process improvements.
For Purchasing Managers in the food and beverage manufacturing sector, the procurement cycle is a critical lever for operational success, cost control, and sustainability. By integrating PlanetTogether APS with robust ERP systems like SAP, Oracle, Microsoft, Kinaxis, or Aveva, companies can elevate procurement from a reactive function to a strategic powerhouse.
The result? Smarter buying decisions, leaner inventories, stronger supplier relationships, and the agility to respond to today’s fast-changing market demands.
If your facility is still managing procurement with disconnected systems and manual processes, now is the time to explore how APS-ERP integration can transform your operations — and your role as a Purchasing Manager.
Are you ready to take your manufacturing operations to the next level? Contact us today to learn more about how PlanetTogether can help you achieve your goals and drive success in your industry.