PlanetTogether as a Central Hub for Planning Data in Multi-System Environments
In beverage manufacturing industry, maintaining a streamlined production process is critical. Operations Directors face growing challenges from market volatility, increasing demand variability, and the need for sustainable practices. Managing these complexities requires sophisticated planning tools that integrate seamlessly with existing enterprise systems.
PlanetTogether emerges as a game-changing solution, providing a central hub for planning data in multi-system environments while delivering unparalleled value for operations.
The Multi-System Challenge in Beverage Manufacturing
Beverage manufacturers often operate in a highly interconnected ecosystem of enterprise applications, including Enterprise Resource Planning (ERP) systems like SAP or Oracle, Manufacturing Execution Systems (MES), and Supply Chain Management platforms such as Kinaxis or Aveva. While each system excels at its specific role, siloed operations and disconnected data streams can create inefficiencies, bottlenecks, and decision-making blind spots.
For example, an ERP system might manage high-level financials and procurement, while an MES focuses on real-time production monitoring. However, the absence of a central planning hub to bridge these systems can lead to the following issues:
Data Silos: Critical production and scheduling information often remains trapped in separate systems, leading to misalignment across teams.
Manual Reconciliation: Operations teams may spend hours manually reconciling data from disparate platforms, increasing the risk of errors.
Limited Flexibility: Adapting production schedules to sudden demand changes or supply chain disruptions becomes cumbersome without real-time, integrated insights.
PlanetTogether addresses these issues head-on by serving as a unifying platform for production planning and scheduling, seamlessly integrating with leading enterprise systems.
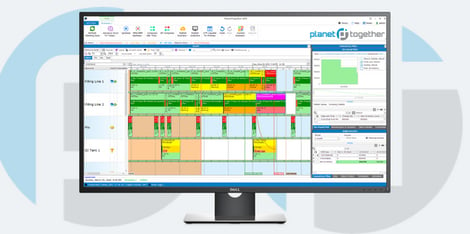
The Role of PlanetTogether as a Central Planning Hub
PlanetTogether’s advanced planning and scheduling (APS) platform is designed to centralize and optimize production planning. By integrating with ERP systems like SAP, Oracle, and Microsoft Dynamics, as well as supply chain platforms like Kinaxis and Aveva, PlanetTogether provides a single source of truth for manufacturing operations.
Key Features of PlanetTogether Integration
Real-Time Data Synchronization
PlanetTogether continuously syncs with ERP, MES, and SCM systems to ensure that planning data remains up-to-date. For instance, real-time inventory levels from SAP or Microsoft Dynamics can inform production schedules, reducing the risk of overproduction or stockouts.
Advanced Scheduling Algorithms
The platform leverages advanced algorithms to create optimal production schedules, taking into account constraints such as machine capacity, workforce availability, and material lead times. These schedules can then be pushed back into systems like Oracle for execution and monitoring.
Scenario Planning and Simulation
PlanetTogether enables Operations Directors to simulate various production scenarios before implementation. By integrating with Kinaxis’ supply chain platform, manufacturers can evaluate the downstream impact of schedule changes on logistics and delivery timelines.
Cross-Functional Visibility
With all planning data centralized in PlanetTogether, stakeholders across procurement, production, and logistics can access the same information. This fosters collaboration and ensures that everyone is aligned on production goals.
Benefits for Beverage Manufacturers
Enhanced Efficiency and Productivity
Beverage manufacturing is highly dynamic, with seasonal spikes and consumer trends driving demand fluctuations. PlanetTogether’s integration with ERP systems like SAP or Oracle allows for automated adjustments to production schedules based on real-time demand signals, ensuring optimal resource utilization. This reduces downtime, eliminates waste, and boosts overall productivity.
Improved Decision-Making
With data from multiple systems consolidated into a single platform, Operations Directors gain access to actionable insights. For example, integrating PlanetTogether with Aveva’s industrial analytics platform enables predictive maintenance scheduling, reducing unplanned equipment downtime.
Agility in Responding to Market Changes
The beverage industry is no stranger to sudden demand shifts due to promotions, weather changes, or global events. PlanetTogether’s scenario planning capabilities, coupled with its integration with supply chain tools like Kinaxis, allow manufacturers to quickly adapt production schedules while minimizing disruptions.
Sustainability Gains
Sustainability is a growing focus in beverage manufacturing. By optimizing production schedules and minimizing resource wastage, PlanetTogether helps manufacturers achieve their sustainability goals. When integrated with SAP’s environmental modules, PlanetTogether can track carbon footprints and identify areas for improvement.
Implementation Best Practices
To maximize the benefits of PlanetTogether as a central hub, consider the following best practices:
Define Clear Objectives: Establish clear goals for the integration, such as reducing production lead times, improving forecast accuracy, or achieving sustainability targets.
Engage Cross-Functional Teams: Involve stakeholders from production, supply chain, IT, and sustainability teams to ensure that the integration addresses the needs of all departments.
Invest in Change Management: Training and onboarding are critical to ensure that teams can fully leverage PlanetTogether’s capabilities.
Monitor and Optimize: Continuously track key performance indicators (KPIs) to measure the success of the integration and identify areas for improvement.
In an era where data drives decision-making, beverage manufacturers cannot afford to operate in silos. PlanetTogether’s role as a central hub for planning data offers a transformative solution for Operations Directors navigating multi-system environments. By integrating seamlessly with ERP systems like SAP and Oracle, as well as supply chain platforms like Kinaxis and Aveva, PlanetTogether empowers manufacturers to optimize production, enhance agility, and achieve sustainability goals.
Are you ready to take your manufacturing operations to the next level? Contact us today to learn more about how PlanetTogether can help you achieve your goals and drive success in your industry.