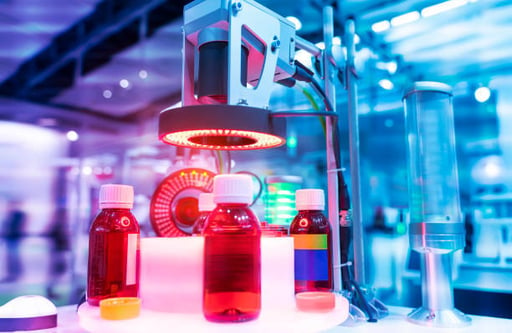
Real-Time Precision: Enabling JIT Inventory with IoT Sensor Data in Chemical Manufacturing
In chemical manufacturing, inventory mismanagement can result in catastrophic losses—from expired hazardous materials to missed production windows. As manufacturers seek leaner operations and more agile supply chains, Just-In-Time (JIT) inventory has emerged as a powerful methodology for reducing waste and improving production efficiency.
However, JIT requires precise timing, real-time visibility, and seamless coordination across procurement, production, and delivery. That's where Internet of Things (IoT) sensor data and Advanced Planning and Scheduling (APS) platforms like PlanetTogether, integrated with enterprise systems such as SAP, Aveva, Microsoft, Oracle, or Kinaxis, come into play.
This blog explores how Manufacturing IT leaders in chemical facilities can enable successful JIT inventory practices by tapping into IoT-powered real-time data and APS-driven optimization.
The Role of IoT in Real-Time Inventory Monitoring
Modern chemical manufacturing involves the use of volatile, perishable, and often highly regulated materials. Traditional inventory management systems often fall short in tracking variables like temperature, pressure, humidity, or chemical shelf life. IoT sensor networks solve this by offering:
Granular visibility into inventory conditions across storage tanks, silos, containers, and pipelines.
Automated alerts for threshold breaches (e.g., a temperature-sensitive solvent exceeding safe levels).
Real-time updates on material consumption, reordering needs, and equipment status.
Predictive insights to estimate degradation or usage patterns based on historical and sensor data.
By embedding sensors throughout the plant, Manufacturing IT teams can generate a continuous stream of data that reflects the real-world state of raw materials and finished goods—down to the minute.
JIT Inventory Strategy: Benefits and Challenges
JIT inventory aims to minimize on-hand stock while ensuring that materials and products arrive exactly when needed. For chemical manufacturing, this means:
Key Benefits
Lower carrying costs: Less warehousing space and capital tied up in inventory.
Reduced waste: Avoid spoilage or degradation of time-sensitive chemicals.
Increased agility: Faster response to customer orders and market changes.
Sustainability: Leaner operations mean lower emissions and less material disposal.
Common Challenges
Unreliable supply chains: Chemical inputs often rely on long lead times and complex logistics.
Volatile demand: Fluctuating customer needs can disrupt carefully planned JIT models.
Limited data integration: Lack of real-time insights across supply chain nodes.
Compliance risks: Regulatory demands for safety and traceability complicate JIT implementations.
To overcome these hurdles, manufacturing IT leaders are turning to digital transformation tools that unify real-time data, planning logic, and operational execution.
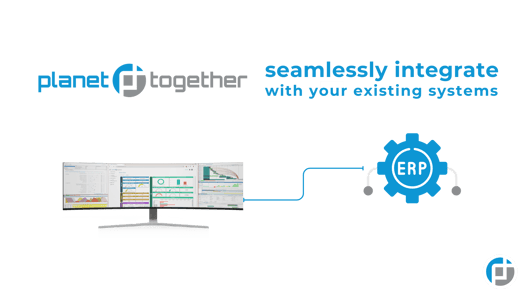
Bridging IoT and JIT with APS Platforms like PlanetTogether
PlanetTogether APS acts as the optimization engine that transforms raw sensor data into actionable planning decisions. When integrated with ERP platforms like SAP or Oracle, MES platforms such as Aveva, or supply chain platforms like Kinaxis or Microsoft Dynamics, the result is a synchronized digital thread across the enterprise.
How It Works: A Connected Workflow
Data Capture (IoT Layer)
Sensors measure tank levels, chemical integrity, room temperature, batch progress, and equipment conditions.
Data is transmitted via gateways to cloud or on-premise systems.
Integration Layer (ERP/MES)
Platforms like SAP or Aveva contextualize this data within business workflows.
Material master data, batch records, and compliance documentation are linked.
Planning Layer (APS – PlanetTogether)
PlanetTogether receives live inputs on raw material status and machine availability.
It adjusts production schedules in real-time to avoid delays or inventory overages.
Execution & Feedback Loop
Optimized schedules are sent back to MES for dispatching.
Results and deviations feed back into the APS system for continuous learning.
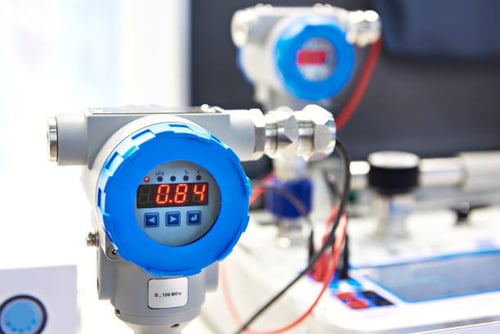
Practical Use Case: JIT in a Specialty Chemical Facility
Imagine a specialty chemical plant producing custom polymer blends. These blends require precise temperature-controlled ingredients that have a shelf life of 72 hours once opened.
IoT sensors installed on ingredient storage tanks track fluid levels and temperatures.
PlanetTogether APS, integrated with Aveva MES and SAP ERP, receives real-time data.
Based on this, PlanetTogether automatically reschedules production when a temperature deviation puts an ingredient at risk of spoilage.
A new order is sent through SAP’s procurement module, while MES adapts the shop floor sequence.
This prevents loss, ensures quality, and supports JIT delivery commitments to customers.
The result: minimal inventory, zero waste, and uninterrupted production flow.
Advantages of Integration for Manufacturing IT Teams
For Manufacturing IT leaders, enabling this level of connectivity and orchestration delivers substantial advantages:
Real-Time Planning Precision
Live sensor inputs feed directly into planning engines, enabling true-to-the-second schedule adaptation.
System Interoperability
PlanetTogether’s flexibility in integrating with SAP, Oracle, Microsoft, Kinaxis, and Aveva allows IT teams to work within existing infrastructures without disruptive overhauls.
Predictive Maintenance and Inventory Sync
Sensor alerts on asset wear or leaks can be used to adjust both maintenance schedules and production timelines, reducing downtime while aligning with JIT goals.
Enhanced Compliance and Traceability
IoT integration ensures that environmental conditions, timestamps, and operator interactions are recorded automatically—critical for audits in the chemical industry.
The Digital Backbone of JIT Excellence
In an industry where safety, precision, and agility are non-negotiable, implementing JIT inventory is no small feat. But with the power of IoT sensor data and the intelligence of APS platforms like PlanetTogether—integrated with trusted systems like SAP, Microsoft, Oracle, Kinaxis, or Aveva—chemical manufacturers can unlock new levels of performance and resilience.
For Manufacturing IT leaders, the mandate is clear: build the digital backbone that synchronizes data, systems, and people—delivering not just products on time, but also insight on demand.
Are you ready to take your manufacturing operations to the next level? Contact us today to learn more about how PlanetTogether can help you achieve your goals and drive success in your industry.