Remote Monitoring and Control Systems in Global Food and Beverage Manufacturing
The role of a Production Scheduler is pivotal in food and beverage manufacturing. It's a responsibility that demands precision, agility, and foresight to ensure seamless operations amidst varying demands, resources, and market fluctuations. In this digitally driven era, where global connectivity is the norm, leveraging remote monitoring and control systems has emerged as a game-changer in optimizing manufacturing processes.
In this blog, we look into the significance of integrating such systems with enterprise resource planning (ERP), supply chain management (SCM), and manufacturing execution systems (MES), with a focus on platforms like PlanetTogether, SAP, Oracle, Microsoft, Kinaxis, Aveva, and others.
Remote Monitoring and Control Systems
Remote monitoring and control systems empower manufacturers with real-time visibility and management capabilities across their global operations. These systems utilize IoT sensors, data analytics, and connectivity technologies to gather data from various points in the manufacturing process. This data is then processed and analyzed to provide insights that enable proactive decision-making and optimization of production processes.
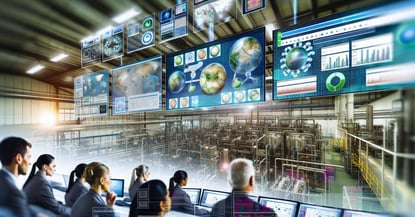
The Role of Production Scheduler in Food and Beverage Manufacturing
The Production Scheduler plays a critical role in orchestrating production activities to meet demand while maximizing resource utilization and minimizing costs. Their responsibilities include creating production schedules, coordinating with various departments, and ensuring smooth operations on the factory floor. With the aid of remote monitoring and control systems, Production Schedulers gain access to real-time data and insights that enable them to make informed decisions promptly.

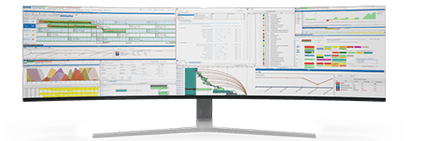
Integration with ERP, SCM, and MES Systems
To unlock the full potential of remote monitoring and control systems, integration with ERP, SCM, and MES systems is imperative. These integrations facilitate seamless data exchange and synchronization across different functions within the organization, enabling a holistic view of operations. Platforms like PlanetTogether offer robust integration capabilities with leading ERP systems such as SAP, Oracle, Microsoft Dynamics, Kinaxis RapidResponse, Aveva, and others.
Benefits of Integration
Enhanced Visibility: By integrating remote monitoring and control systems with ERP, SCM, and MES platforms, Production Schedulers gain comprehensive visibility into the entire supply chain and manufacturing process. This visibility enables them to identify bottlenecks, anticipate disruptions, and optimize production schedules accordingly.
Improved Efficiency: Real-time data from remote monitoring systems allows Production Schedulers to react swiftly to changes in demand, inventory levels, or machine performance. By adjusting production schedules in real-time, manufacturers can optimize resource utilization, minimize downtime, and improve overall efficiency.
Streamlined Communication: Integration between remote monitoring systems and ERP, SCM, and MES platforms facilitates seamless communication and collaboration across different departments and locations. This streamlined communication ensures alignment between production schedules, inventory management, procurement, and logistics activities.
Predictive Maintenance: Remote monitoring systems can also enable predictive maintenance by continuously monitoring equipment performance and detecting potential issues before they escalate. Integration with MES systems allows for automatic work order generation and scheduling of maintenance activities, reducing unplanned downtime and maintenance costs.
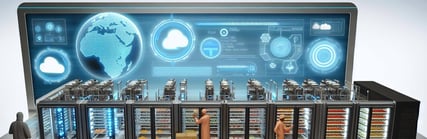
Best Practices for Implementation
Define Clear Objectives: Clearly define the objectives and expected outcomes of integrating remote monitoring and control systems with ERP, SCM, and MES platforms. Whether it's improving production efficiency, reducing costs, or enhancing quality, having clarity on goals is crucial.
Collaborate Cross-Functionally: Collaboration between IT, operations, supply chain, and finance teams is essential for successful implementation. Ensure that all stakeholders are aligned and actively involved throughout the integration process.
Invest in Training and Support: Provide adequate training and support to employees who will be using the integrated systems. This includes both technical training on system usage and operational training on interpreting and acting upon the insights derived from the data.
Monitor and Iterate: Continuously monitor the performance of the integrated systems and iterate as needed to address any challenges or bottlenecks. Regularly review key performance indicators (KPIs) to gauge the effectiveness of the integration and identify areas for improvement.
The utilization of remote monitoring and control systems integrated with ERP, SCM, and MES platforms holds immense potential for enhancing efficiency and competitiveness in global food and beverage manufacturing operations. Platforms like PlanetTogether offer robust integration capabilities with leading ERP, SCM, and MES platforms. Production Schedulers play a pivotal role in leveraging these systems to optimize production schedules, improve resource utilization, and respond effectively to changing market dynamics.
By embracing integration and following best practices for implementation, manufacturers can unlock new levels of agility, visibility, and efficiency across their entire value chain. Are you ready to take your manufacturing operations to the next level? Contact us today to learn more about how PlanetTogether can help you achieve your goals and drive success in your industry.