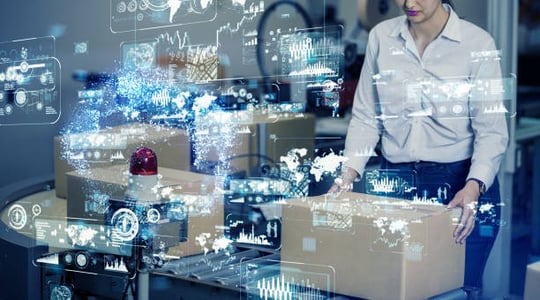
Resilience-First Planning: How APS Responds to Real-Time Disruptions
In today’s fast-evolving packaging and containers manufacturing industry, disruptions are no longer occasional surprises — they’re the new normal. From raw material shortages and supplier delays to shifting customer demand, logistics bottlenecks, and unforeseen workforce issues, supply chain managers are expected to navigate a constant wave of volatility.
For a Supply Chain Manager in this sector, the question is no longer if disruption will hit, but how fast your organization can respond — and whether your systems are designed to bend without breaking. That’s where a resilience-first planning approach becomes critical, and why Advanced Planning and Scheduling (APS) systems like PlanetTogether — especially when integrated with ERP giants such as SAP, Oracle, Microsoft Dynamics, Kinaxis, or Aveva — are transforming the manufacturing landscape.
This blog will explore how resilience-first planning powered by APS helps packaging and containers manufacturers respond to real-time disruptions, maintain production stability, and protect profitability even under stress.
The New Rules of Supply Chain: Resilience Over Efficiency
Historically, supply chain strategies have been dominated by a quest for maximum efficiency — lean inventories, just-in-time delivery, minimal slack in the system. But the pandemic, geopolitical tensions, climate shocks, and supplier instability have taught manufacturers a harsh lesson: efficiency without resilience creates fragility.
For a packaging manufacturer, a disruption upstream (like a resin shortage) or downstream (like a sudden packaging spec change from a major customer) can ripple through the plant floor within hours. Without real-time visibility and adaptive planning tools, production plans become obsolete fast, forcing teams into reactive firefighting.
This is why resilience-first planning is gaining traction. It’s about designing supply chains that can:
Detect disruptions in real time
Re-plan and adjust dynamically
Maintain service levels without incurring massive costs
Provide transparency and decision support to managers
But how can this be achieved practically?
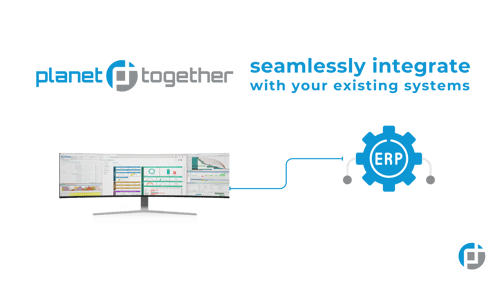
The Role of APS in Real-Time Disruption Management
Advanced Planning and Scheduling (APS) systems like PlanetTogether offer a digital backbone for resilient operations. Unlike traditional Material Requirements Planning (MRP) tools or spreadsheet-based scheduling, APS integrates data across the organization, offering real-time, constraint-based planning.
When integrated with ERP systems like SAP, Oracle, Microsoft Dynamics, Kinaxis, or Aveva, PlanetTogether APS can pull live data — inventory levels, supplier updates, production line status, workforce availability, and customer orders — and translate that into up-to-the-minute production plans.
Here’s how that plays out in a real disruption scenario.
Real-Time Disruption Example: Supplier Delay
Imagine a key packaging material — say, laminated film for flexible pouches — is delayed due to a transportation issue. In a traditional setup, the planner might not discover the delay until the truck fails to arrive. By then, production may already be queued or running on that material, leading to costly downtime or emergency replanning.
With an integrated APS system, however, the moment the supplier updates the shipment status in SAP (or any connected ERP), PlanetTogether automatically detects the disruption and recalculates production priorities. It can:
Reschedule production orders using alternative materials, if available
Re-sequence jobs to prioritize those unaffected by the delay
Alert procurement teams for expedited sourcing
Simulate “what-if” scenarios to assess the cost/benefit of various responses
This transforms the supply chain manager’s role from reactive problem-solver to strategic decision-maker with data-driven options.
Key Benefits of Resilience-First APS Planning
Let’s break down the tangible benefits a Supply Chain Manager gains from embedding resilience-first planning into their operations.
Increased Visibility Across the Supply Chain
When PlanetTogether integrates with systems like SAP or Kinaxis, it becomes the “single pane of glass” showing all moving parts. You can track inventory, production, labor, and demand in one place, meaning disruptions are spotted faster.
Faster, Automated Re-Planning
Manual replanning on spreadsheets can take hours or days. APS automates much of the re-optimization, delivering new, feasible production schedules within minutes — and without overlooking key constraints like machine capacity or shift availability.
Enhanced Collaboration Between Teams
By connecting procurement, production, logistics, and sales through a common planning platform, APS fosters cross-functional collaboration. When a disruption hits, teams can coordinate responses using the same live data, avoiding finger-pointing or siloed reactions.
Cost Control Under Stress
Reactive scrambling usually drives up costs — rush orders, overtime pay, scrapped materials. With APS, manufacturers can simulate scenarios and choose the most cost-effective path forward, preserving margin even under pressure.
Improved Customer Reliability
In the packaging and containers world, customers often have strict delivery windows tied to their own product launches or promotions. Resilience-first APS planning helps maintain on-time delivery commitments, even when internal chaos strikes.
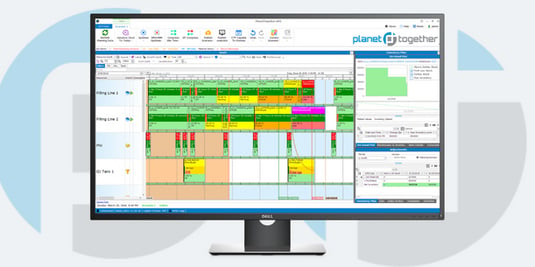
PlanetTogether APS + ERP Integration: The Resilience Multiplier
PlanetTogether’s integration capabilities are a force multiplier for resilience.
When combined with an ERP like SAP or Oracle, APS can:
Pull live supplier updates and inventory levels
Sync with sales forecasts and order changes
Adjust production schedules instantly when an upstream or downstream change occurs
Share updated production plans back into the ERP for financial and operational alignment
This tight integration eliminates data silos, reduces latency, and ensures that everyone from planners to plant floor teams is operating on the same, real-time plan.
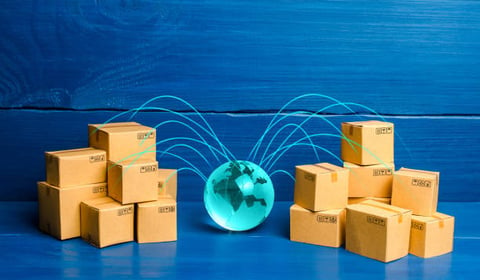
Steps for Supply Chain Managers to Implement Resilience-First APS
Transitioning to a resilience-first planning model doesn’t happen overnight. Here’s a practical roadmap for Supply Chain Managers ready to elevate their operations:
Assess Current Vulnerabilities
Map out your most common or damaging disruption types (e.g., raw material delays, labor shortages, equipment breakdowns). Identify where manual processes or slow data flows are preventing timely responses.
Evaluate APS Solutions
Review APS systems like PlanetTogether that are purpose-built for manufacturing environments, ensuring they can integrate smoothly with your existing ERP (SAP, Oracle, Microsoft, Kinaxis, Aveva).
Pilot Real-Time Integration
Start with a focused integration project — perhaps linking APS with supplier data streams or inventory tracking — to prove the value of real-time adjustments.
Train Teams on Scenario Planning
Resilience isn’t just about systems; it’s about mindset. Equip your teams to run “what-if” scenarios using APS tools, so they’re ready to make informed choices when disruptions hit.
Establish Continuous Improvement Loops
Use APS reports and analytics to understand how well your organization responds to disruptions. Feed those insights back into process improvements, supplier negotiations, or workforce planning.
From Reactive to Proactive Supply Chains
In a world of constant uncertainty, packaging and containers manufacturers cannot afford to treat disruptions as one-off events. Resilience-first planning powered by APS helps organizations shift from reactive firefighting to proactive, data-driven agility.
By leveraging advanced tools like PlanetTogether, especially when tightly integrated with ERP systems, Supply Chain Managers gain the visibility, speed, and confidence to not just survive disruptions — but to use them as a competitive edge.
Are you ready to take your manufacturing operations to the next level? Contact us today to learn more about how PlanetTogether can help you achieve your goals and drive success in your industry.