Scheduling Optimization for Variable Demand Patterns
Operations Directors face a myriad of challenges daily in industrial manufacturing. Among these, scheduling optimization is a critical aspect that directly impacts productivity, resource allocation, and ultimately, the bottom line. With the ever-changing market demands and the need for efficient resource management, integrating advanced scheduling software like PlanetTogether with ERP, SCM, and MES systems from industry giants like SAP, Oracle, Microsoft, Kinaxis, and Aveva has become essential.
In this blog, we will look into the world of scheduling optimization for variable demand patterns and explore how the integration of these systems can revolutionize your industrial manufacturing facility.
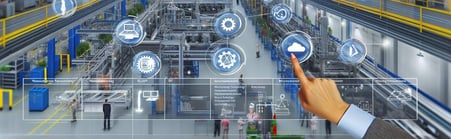
Variable Demand Patterns
Variable demand patterns are a reality in the industrial manufacturing sector. Whether it's seasonal fluctuations, sudden market changes, or unforeseen disruptions, your facility must be prepared to adapt swiftly. Traditional scheduling methods often fall short in such scenarios, leading to inefficiencies, missed deadlines, and increased costs. This is where advanced scheduling optimization solutions come into play.

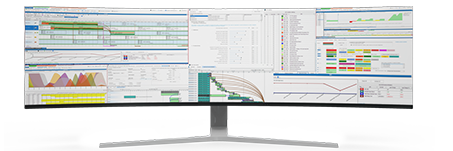
The Role of PlanetTogether
PlanetTogether is a powerful advanced planning and scheduling (APS) software that specializes in optimizing production schedules. Its strength lies in its ability to adapt to variable demand patterns seamlessly. Here's how it works:
Data Integration: PlanetTogether can integrate with various data sources within your industrial manufacturing facility, including ERP, SCM, and MES systems. This means that real-time data on inventory, machine availability, workforce capacity, and market demand are readily accessible for scheduling.
Demand Forecasting: The software employs advanced algorithms to forecast demand patterns accurately. By analyzing historical data, it can predict future demand fluctuations and trends, helping you stay proactive in your scheduling.
Resource Optimization: PlanetTogether optimizes resource allocation based on demand forecasts. It considers machine capabilities, operator skills, and material availability to create an efficient production schedule.
What-If Scenarios: The software allows you to simulate different scenarios. You can assess the impact of increased demand, machine breakdowns, or supply chain disruptions and make informed decisions accordingly.
Real-Time Updates: With integration into your ERP, SCM, and MES systems, PlanetTogether can provide real-time updates on the status of ongoing operations. This ensures that any changes in demand or disruptions are immediately factored into the schedule.
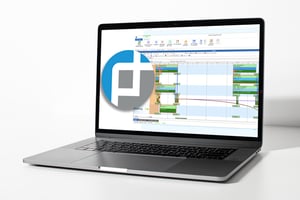
Benefits of Integrating PlanetTogether with ERP, SCM, and MES Systems
Now that we understand how PlanetTogether operates, let's explore the benefits of integrating it with your existing systems:
Streamlined Communication: Integrating PlanetTogether with ERP, SCM, and MES systems enhances communication across your facility. Data flows seamlessly between these systems, eliminating manual data entry and reducing the risk of errors.
End-to-End Visibility: You gain complete visibility into your manufacturing operations. From order placement to production scheduling, inventory management, and delivery, you can track every step in real-time.
Improved Decision-Making: With accurate data and predictive analytics at your fingertips, you can make informed decisions quickly. Whether it's adjusting production schedules, reordering materials, or reallocating resources, you have the insights needed to act decisively.
Cost Reduction: Optimized scheduling minimizes downtime, reduces overproduction, and lowers labor costs. This translates into significant cost savings for your industrial manufacturing facility.
Enhanced Customer Satisfaction: Meeting variable demand patterns efficiently ensures that customer orders are fulfilled on time. This boosts customer satisfaction and helps maintain strong client relationships.
In the highly competitive landscape of industrial manufacturing, the ability to adapt to variable demand patterns is crucial. Integrating advanced scheduling optimization software like PlanetTogether with ERP, SCM, and MES systems from industry leaders such as SAP, Oracle, Microsoft, Kinaxis, and Aveva can be a game-changer for Operations Directors. The benefits include streamlined communication, end-to-end visibility, improved decision-making, cost reduction, and enhanced customer satisfaction.
By harnessing the power of data integration and predictive analytics, you can optimize your production schedules, minimize downtime, and stay ahead of market fluctuations. As an Operations Director, embracing this integration can lead to increased efficiency, reduced costs, and ultimately, a more competitive and successful industrial manufacturing facility.
Are you ready to take your manufacturing operations to the next level? Contact us today to learn more about how PlanetTogether can help you achieve your goals and drive success in your industry.
So, take the step towards scheduling optimization for variable demand patterns today, and watch your facility thrive in the face of uncertainty.