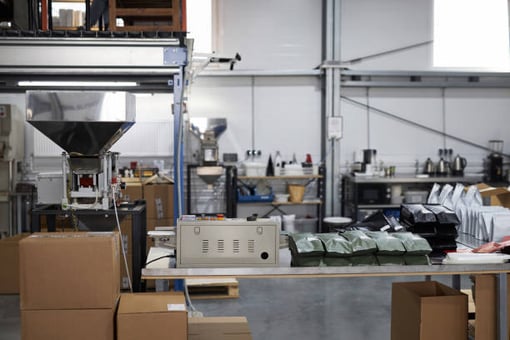
Shorter Lead Times, Higher Accuracy: APS Tools for Just-in-Time Manufacturing
In packaging and containers manufacturing, every minute counts. Customers demand shorter lead times, greater customization, and flawless delivery — all while production teams juggle raw material variability, equipment limitations, and workforce constraints. For production schedulers, meeting these demands without sacrificing accuracy or efficiency is a daily challenge.
This is where Advanced Planning and Scheduling (APS) systems come into play, especially when tightly integrated with ERP platforms like SAP, Oracle, Microsoft Dynamics, Kinaxis, or Aveva. Leveraging a system like PlanetTogether APS helps packaging manufacturers embrace Just-in-Time (JIT) manufacturing principles, achieving the agility and precision needed to thrive in today’s competitive environment.
The High-Stakes Reality of JIT in Packaging
Just-in-Time manufacturing is a philosophy built around minimizing inventory, reducing waste, and producing exactly what is needed — no more, no less — exactly when it’s needed. For packaging and containers manufacturers, this approach offers significant advantages:
Lower inventory carrying costs by reducing excess stock of materials and finished goods.
Faster response to customer demand through highly adaptive production.
Improved cash flow by tying up less capital in unused stock.
Reduced risk of obsolescence especially for customized or seasonal packaging.
However, JIT also introduces high levels of risk. A late material delivery, a production line breakdown, or a scheduling error can bring operations to a halt — cascading into late orders, costly expedited shipping, or lost customers. This makes precise scheduling and flawless coordination essential.
Why Traditional Scheduling Falls Short
Many packaging plants still rely on spreadsheets, manual scheduling boards, or basic ERP modules to manage production plans. While these tools may handle basic needs, they struggle with:
Complex production dependencies, such as multi-step manufacturing, finishing, and packing.
Machine and labor constraints that vary from day to day.
Sudden disruptions from late supplier shipments, last-minute order changes, or equipment downtime.
Detailed capacity optimization across multiple production lines or facilities.
Traditional tools simply can’t provide the speed, flexibility, or optimization required to keep a JIT production system humming.
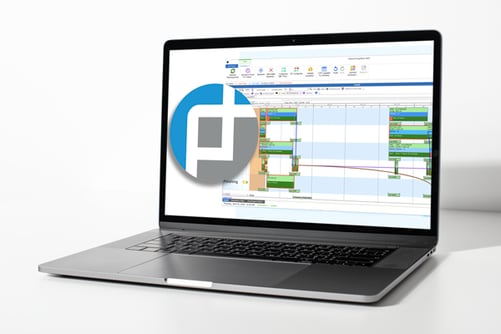
APS to the Rescue: The Role of PlanetTogether
Advanced Planning and Scheduling systems like PlanetTogether APS fill this critical gap by delivering:
Real-time visibility across materials, machines, labor, and orders.
Optimized production sequences that reduce changeover times, maximize throughput, and align with delivery commitments.
Dynamic rescheduling capabilities to instantly respond to disruptions.
Detailed scenario planning to test various what-if situations before making decisions.
Integration with ERP systems (like SAP, Oracle, Microsoft, Kinaxis, or Aveva) to ensure alignment between planning, production, procurement, and finance.
By combining optimization algorithms with real-time data, PlanetTogether APS empowers schedulers to make decisions that balance lead times, cost, and capacity — essential for Just-in-Time operations.
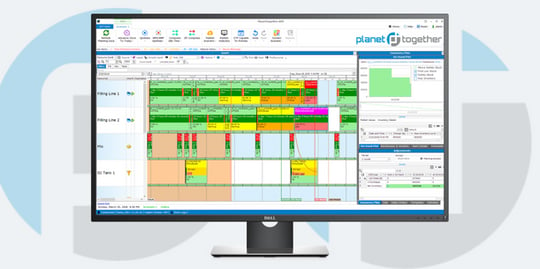
How APS Drives Shorter Lead Times
Shorter lead times don’t come from working harder — they come from working smarter. Here’s how APS tools make that possible:
Optimized Production Sequences
PlanetTogether APS evaluates thousands of possible production sequences to identify the most efficient path, minimizing changeovers and reducing idle time. Instead of batching jobs just by type or customer, the system looks at the bigger picture — including machine capabilities, material availability, labor constraints, and due dates.
Real-Time Constraint Management
JIT manufacturing depends on knowing what’s possible right now. With APS, schedulers can see real-time capacity constraints and avoid overloading resources. If a key machine is down or a material is delayed, the system automatically recalculates the schedule to reflect the new reality — before it turns into a crisis.
Material Synchronization
PlanetTogether’s integration with ERP platforms like SAP or Oracle ensures that production schedules are synchronized with material availability. No more starting a job only to find a critical component is missing; APS aligns procurement and production to keep JIT promises intact.
Reduced Manual Intervention
Without APS, schedulers often spend hours manually adjusting plans, trying to balance priorities. APS automates this optimization, freeing up schedulers to focus on strategic decisions, not tactical firefighting.
Higher Accuracy: Hitting Delivery Targets
Shorter lead times mean little if delivery promises aren’t met. APS improves schedule accuracy in several key ways:
Integrated Data Streams
By integrating PlanetTogether APS with ERP systems (such as Microsoft Dynamics or Kinaxis), the scheduling process uses the most accurate, up-to-date data on orders, inventory, and capacity. This reduces the risk of errors caused by outdated or disconnected systems.
Predictive Analytics
APS tools don’t just react — they predict. By analyzing historical performance and real-time data, PlanetTogether can flag potential bottlenecks or delays before they impact delivery, allowing schedulers to take corrective action proactively.
Scenario Planning for Confidence
When urgent customer requests or last-minute changes arise, schedulers can use APS to run scenario analyses, testing various options and understanding their impacts. This reduces guesswork and increases confidence that new plans will succeed.
Performance Monitoring
APS systems provide detailed metrics and KPIs, helping teams monitor schedule adherence, identify chronic issues, and drive continuous improvement.
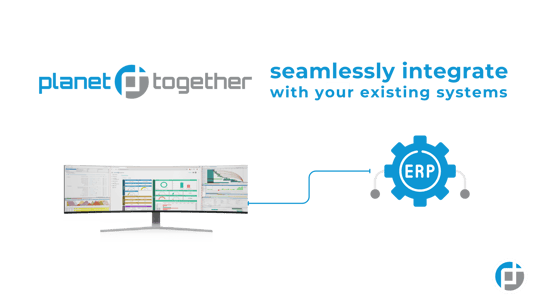
The Power of Integration: APS + ERP
The true magic happens when APS isn’t operating in isolation but is seamlessly integrated with your enterprise systems. Integration between PlanetTogether APS and platforms like SAP, Oracle, Microsoft Dynamics, Kinaxis, or Aveva provides:
End-to-end data visibility, ensuring alignment between planning, purchasing, production, and shipping.
Automated data flows, eliminating manual data entry and reducing errors.
Collaborative decision-making, enabling cross-functional teams to work from a shared, real-time playbook.
Faster reaction times, as information flows instantly between systems, supporting agile responses.
This level of integration is critical in packaging and containers manufacturing, where customer timelines are tight and product complexity is high.
Moving Forward: What Should Production Schedulers Do?
For production schedulers in packaging and containers manufacturing, staying competitive means moving beyond manual tools and embracing intelligent scheduling. Here’s how to start:
Assess your current scheduling processes: Where are the bottlenecks? How often are plans disrupted? How much time is spent manually adjusting schedules?
Evaluate APS solutions: Look for systems like PlanetTogether that offer tight ERP integration, advanced optimization, and real-time rescheduling.
Align stakeholders: Bring together production, procurement, sales, and IT to ensure cross-functional buy-in.
Pilot, then scale: Start with a pilot project in one production area, measure results, and scale up as confidence grows.
Commit to continuous improvement: APS is not a one-time fix — it’s a platform for ongoing optimization and innovation.
In a Just-in-Time manufacturing environment, success hinges on precision, agility, and accuracy. With the help of APS tools like PlanetTogether, integrated tightly with ERP systems such as SAP, Oracle, Microsoft Dynamics, Kinaxis, or Aveva, production schedulers can meet these demands head-on — reducing lead times, improving accuracy, and driving operational excellence.
For packaging and containers manufacturers, the choice is clear: smarter scheduling isn’t just a competitive advantage — it’s essential.
Are you ready to take your manufacturing operations to the next level? Contact us today to learn more about how PlanetTogether can help you achieve your goals and drive success in your industry.