Automated Replenishment Scheduling
Every step in the production process, from raw material procurement to final product delivery, must be meticulously planned and executed to meet customer demands while optimizing resources in chemical manufacturing. One critical aspect of this process is replenishment scheduling, where the right materials are replenished at the right time to keep operations running smoothly.
Traditionally, replenishment scheduling has been a manual and time-consuming task, prone to errors and inefficiencies. However, with advancements in technology and the integration of innovative software solutions like PlanetTogether with leading ERP, SCM, and MES systems such as SAP, Oracle, Microsoft, Kinaxis, and Aveva, chemical manufacturers now have the opportunity to automate and optimize their replenishment scheduling processes like never before.
In this blog post, we will explore the significance of automated replenishment scheduling in chemical manufacturing and how integration between PlanetTogether and various enterprise systems can revolutionize operations, leading to increased productivity, reduced costs, and enhanced competitiveness.
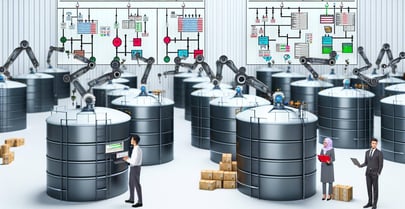
The Importance of Automated Replenishment Scheduling
Effective replenishment scheduling is critical for chemical manufacturers for several reasons:
Just-in-Time Production: Chemical manufacturing often operates on a just-in-time basis, where materials need to be available precisely when they are required in the production process. Automated replenishment scheduling ensures that materials are replenished at the right time to avoid disruptions and delays in production.
Inventory Optimization: Maintaining optimal inventory levels is essential to avoid overstocking or stockouts, both of which can have significant financial implications. Automated replenishment scheduling helps in balancing inventory levels by accurately forecasting demand and replenishing materials accordingly.
Resource Utilization: By automating replenishment scheduling, manufacturers can optimize the utilization of resources such as raw materials, equipment, and manpower. This ensures that resources are utilized efficiently, minimizing waste and maximizing profitability.
Enhanced Flexibility: In today's fast-paced market environment, manufacturers need to be agile and responsive to changing customer demands and market conditions. Automated replenishment scheduling allows for greater flexibility in adapting to these changes quickly and effectively.
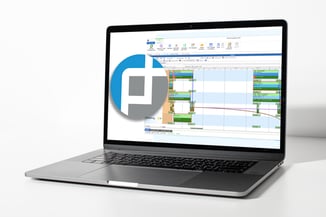
Integration Between PlanetTogether and ERP, SCM, and MES Systems
PlanetTogether is a leading production planning and scheduling software that offers powerful capabilities for optimizing manufacturing operations. When integrated with ERP, SCM, and MES systems such as SAP, Oracle, Microsoft, Kinaxis, and Aveva, it becomes even more potent, enabling seamless data exchange and synchronization across the entire manufacturing ecosystem.
Here's how integration between PlanetTogether and these enterprise systems enhances automated replenishment scheduling in chemical manufacturing:
Real-Time Data Exchange: Integration allows for real-time exchange of data between PlanetTogether and ERP, SCM, and MES systems, ensuring that planners have access to the most up-to-date information on inventory levels, production schedules, and customer orders. This enables more accurate forecasting and replenishment planning.
Improved Visibility: With integration, stakeholders across the organization have better visibility into the replenishment scheduling process, from procurement and production to distribution and delivery. This transparency facilitates collaboration and decision-making, leading to improved overall efficiency.
Enhanced Predictive Analytics: By leveraging data from ERP, SCM, and MES systems, PlanetTogether can perform advanced predictive analytics to forecast demand, identify trends, and anticipate supply chain disruptions. This enables proactive replenishment scheduling, minimizing the impact of unforeseen events on production.
Automated Workflows: Integration enables the automation of replenishment scheduling workflows, eliminating manual interventions and streamlining processes. This not only saves time and reduces errors but also frees up resources to focus on more strategic tasks.
Automated replenishment scheduling is a game-changer for chemical manufacturers looking to optimize their operations and stay competitive in today's market. By leveraging advanced software solutions like PlanetTogether and integrating them with leading ERP, SCM, and MES systems, manufacturers can streamline their replenishment scheduling processes, improve efficiency, and achieve better business outcomes.
As chemical manufacturing continues to evolve, embracing automation and integration will be key to unlocking new levels of productivity, agility, and profitability. With the right technology and strategic approach, manufacturers can navigate the complexities of the industry with confidence, driving growth and success.
Are you ready to take your manufacturing operations to the next level? Contact us today to learn more about how PlanetTogether can help you achieve your goals and drive success in your industry in the years to come.