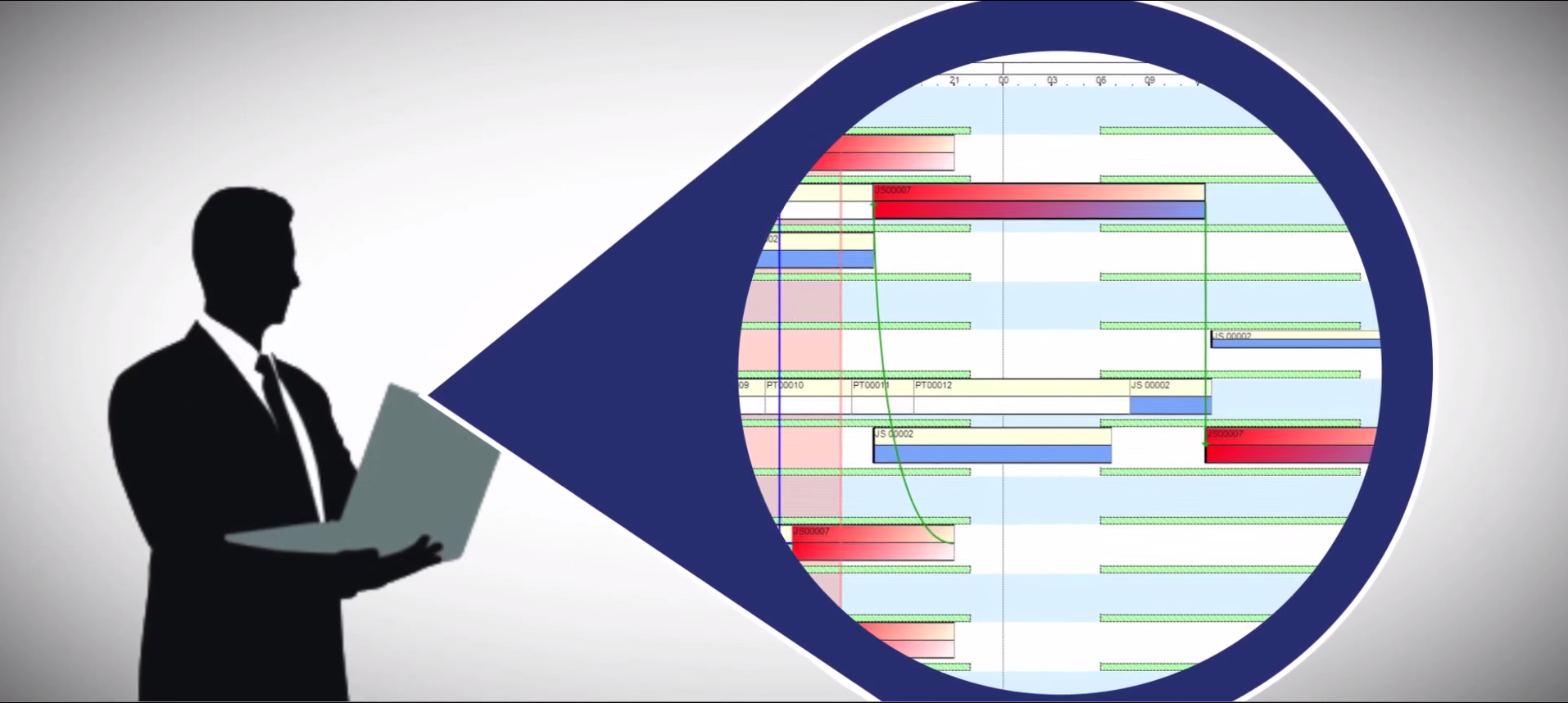
Generally speaking, not all parts for goods produced at a factory are the same in terms of complexity. Manufacturing simple components in lower-cost countries to ship the parts to higher-cost countries makes a lot of sense for businesses.
Subcontracting selected operations to vendors is common in many manufacturing companies. Subcontracting can be a rare occurrence or an integral part of all production processes.
As China's wages increase, companies with international holdings are beginning to look at options outside the former manufacturing giant. In the past, the Indian population of more than a billion people has attracted companies around the world as a location to outsource their technology and customer services, but not for manufacturing. Investors in the industry found that bureaucratic delays, old-fashioned labor rules, and inadequate infrastructure were significant obstacles.
Growing the Superplant
Anticipating the strengthening of India's manufacturing market, GE opened Phase I of a flexible multi-modal factory at Chakan in Pune (South India) in February. The plant covers 67 acres and will produce different products for multiple verticals utilizing shared infrastructure/equipment/people in the same building. One thousand five hundred workers will operate in an area the size of 38 football fields.
GE's investment is $200 million, and the aim is twofold for the new facility: first, to harmonize its various operations, and second, to gain economies of scale and better use of its capital. The facility's CEO looks forward to quickly adjusting production with demand while using the same people and factory floor. Half of the output will remain in India, and half will be exported.
The Pune factory has state-of-the-art digitally interlinked equipment, supply chains, distribution networks, and service groups. It has been described as an “intelligent ecosystem or superplant.” The real-time connected system should allow GE to optimize production and communications for decision-making. The factory includes advanced 3D printing and laser inspection technologies. Products to be fabricated range from aircraft engine parts to locomotive components, wind turbines, and water treatment units.
A superplant like GE's brings users and manufacturing locations together to visualize solutions to manage capacity and material bottlenecks, synchronize the workflow, protect against uncertainty and variability, and optimize alternatives for on-time deliveries with high-profit margins.
Advanced Planning and Scheduling (APS) System
An APS system is a planning and scheduling system by which raw materials and production capacity are optimally allocated to meet demand. It allows for simultaneous planning and scheduling of your production based on available material, labor, machines, constraints, power, and other sequence-dependent setups. The result is a feasible plan optimized for your KPIs of interest created in seconds.
Advanced Planning and Scheduling software have become a must for modern-day manufacturing operations as customer demand for increased product assortment, fast delivery, and downward cost pressures become prevalent. These systems help planners save time while providing greater agility in updating ever-changing priorities, production schedules, and inventory plans. APS Systems can be quickly integrated with an ERP/MRP software to fill the gaps where these systems lack planning and scheduling flexibility, accuracy, and efficiency.
With APS you can:
- Create optimized schedules that balance production efficiency and delivery performance
- Maximize throughput on bottleneck resources to increase revenue
- Synchronize supply with demand to reduce inventories
- Provide company-wide visibility to resource capacity
- Enable scenario data-driven decision making
Implementing Advanced Planning and Scheduling (APS) Software will take your manufacturing operations to the next level of production efficiency by taking advantage of the operational data you already possess in your ERP system. APS is a step in the right direction of efficiency and lean manufacturing production enhancement. Try out a free trial or demo!