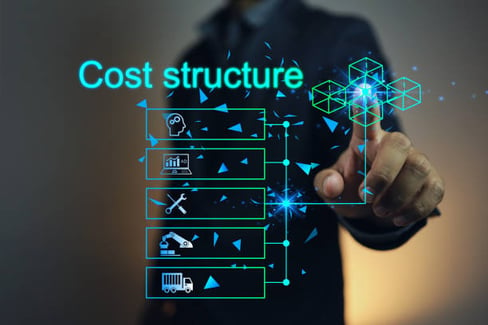
Supplier Cost Structures: Aligning Sourcing and Scheduling for ROI in Chemical Manufacturing
In today’s volatile global economy, chemical manufacturers face intense pressure to maximize return on investment (ROI) while balancing supplier costs, production schedules, and shifting customer demands. For plant managers, understanding the interplay between supplier cost structures and internal operations is critical—not just for cutting costs, but for driving long-term profitability.
At the heart of this challenge lies a simple question: how can plant managers align sourcing strategies with production scheduling to generate the highest possible ROI? The answer increasingly involves leveraging advanced planning and scheduling (APS) systems like PlanetTogether, seamlessly integrated with enterprise platforms such as SAP, Oracle, Microsoft Dynamics, Kinaxis, or Aveva.
Let’s explore how integrating supplier cost insights with scheduling decisions reshapes chemical manufacturing operations for the better.
Understanding Supplier Cost Structures in the Chemical Industry
Supplier cost structures refer to the breakdown of how suppliers price raw materials, components, and services. These can include:
Fixed Costs — Long-term contracts, infrastructure investments, or minimum order quantities (MOQ).
Variable Costs — Price fluctuations tied to raw material inputs, fuel prices, labor rates, or currency exchange.
Logistics Costs — Freight, duties, tariffs, and storage fees.
Risk-Related Costs — Contingencies for supply disruptions, quality rework, or late delivery penalties.
For chemical manufacturers, raw material costs often account for 50–70% of total production expenses. Even minor shifts in supplier cost structures can have a magnified effect on margins. Yet many plant managers struggle to translate supplier cost data into actionable scheduling decisions.
Why? Because traditional planning systems typically operate in silos, with procurement, production, and logistics using separate systems and datasets that rarely synchronize in real time.
This is where APS comes in.
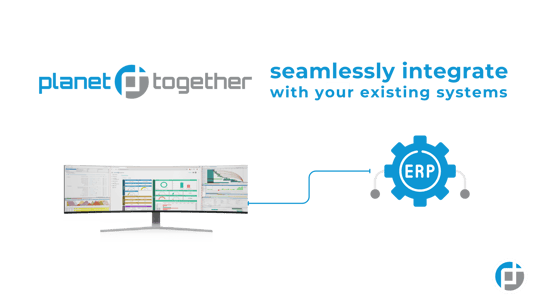
The Role of Advanced Planning and Scheduling (APS)
APS platforms like PlanetTogether are designed to centralize and optimize planning across multiple dimensions: material availability, production capacity, labor, equipment, and delivery deadlines.
When integrated with ERP systems such as SAP, Oracle, Microsoft, Kinaxis, or Aveva, PlanetTogether pulls supplier data—including lead times, MOQ, cost brackets, and discount tiers—directly into the scheduling process. This integration enables:
Cost-aware scheduling — Select suppliers based not only on availability but also on the lowest cost-to-serve.
Dynamic reprioritization — Shift production plans in real time as supplier prices, lead times, or availabilities change.
Scenario analysis — Model “what-if” situations, such as switching suppliers or splitting orders, to evaluate cost and delivery impacts.
The result? Plant managers can align sourcing decisions with the production floor to minimize total landed costs, not just unit prices.
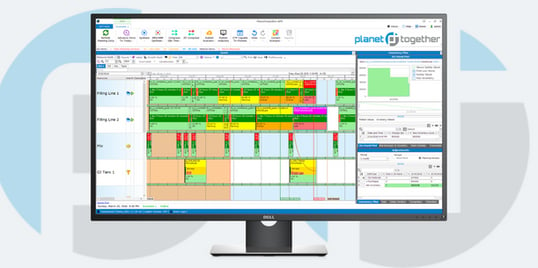
Aligning Sourcing and Scheduling for Maximum ROI
Here’s how an integrated APS-ERP approach improves ROI for chemical manufacturers:
Visibility Across the Entire Supply Chain
With PlanetTogether connected to systems like SAP or Oracle, plant managers gain full visibility into supplier constraints, purchase order status, inbound logistics, and inventory levels.
Example: If a key chemical supplier announces a price increase effective next quarter, APS can immediately adjust scheduling to front-load orders now while prices are lower, avoiding future cost spikes.
Without this integration, procurement teams might negotiate in isolation while production keeps following static plans, missing key cost-saving opportunities.
Optimizing Order Quantities and Batches
Chemical production often involves large-scale batch processes. The challenge is aligning supplier MOQs and price brackets (e.g., discounts at higher order volumes) with batch sizes on the production floor.
APS lets plant managers model various supplier scenarios:
If we increase batch size, can we unlock a better supplier discount?
If we reduce batch size, can we improve flexibility without increasing per-unit costs?
This modeling leads to better synchronized sourcing and production strategies—resulting in lower overall material and operational costs.
Reducing Excess Inventory Costs
Chemical products often have shelf-life constraints or require controlled storage conditions, making over-purchasing costly. By integrating real-time supplier lead times with production schedules, APS systems can:
Avoid stockpiling just to secure bulk discounts.
Schedule deliveries and production runs just in time to meet demand without incurring holding costs.
Quickly shift to backup suppliers if delays or shortages threaten production continuity.
This approach aligns cost savings with operational efficiency, protecting both margins and product quality.
Scenario Planning for Supply Disruptions
Supplier risks—whether geopolitical, environmental, or logistical—can drive sudden cost increases or availability challenges. PlanetTogether’s integration with ERP platforms enables scenario modeling that weighs different supplier and scheduling options.
For example, a plant manager can ask:
What happens to costs and production output if we switch from a low-cost offshore supplier to a higher-cost local supplier with shorter lead times?
How does a transportation strike affect our material flow, and can we reprioritize production to focus on available inputs?
This proactive planning helps chemical manufacturers maintain stable production even when supplier conditions shift, avoiding costly downtime.
Continuous Feedback Loops for Improvement
One of the most valuable aspects of an integrated APS-ERP system is the data feedback loop it creates. Every sourcing and scheduling decision generates data on actual costs, cycle times, yields, and supplier performance.
Over time, this data can be analyzed to:
Identify the most reliable and cost-effective suppliers.
Fine-tune production schedules to match supplier patterns.
Refine forecasts to align with both market demand and supply-side realities.
This continuous improvement approach ensures that every future planning cycle becomes more precise, efficient, and ROI-focused.
Why Integration Matters
Without integration, even the best APS tools operate in a silo. The true power of advanced scheduling comes when it is embedded within the larger enterprise ecosystem, pulling live data from ERP, procurement, logistics, and supplier management systems.
Platforms like SAP, Oracle, Microsoft Dynamics, Kinaxis, and Aveva hold vast amounts of supplier, order, and cost data. When PlanetTogether taps into this, the result is a cohesive, synchronized planning environment where sourcing and scheduling reinforce each other.
This integration is no longer optional; it’s essential for chemical manufacturers seeking to thrive in a market defined by volatility, complexity, and competition.
In chemical manufacturing, plant managers sit at the crossroads of cost, capacity, and customer satisfaction. To navigate this complexity, they need more than spreadsheets or static schedules—they need an integrated, intelligent planning system that bridges the gap between sourcing and production.
By aligning supplier cost structures with advanced scheduling through solutions like PlanetTogether, integrated with ERP platforms such as SAP, Oracle, Microsoft, Kinaxis, or Aveva, chemical manufacturers
For chemical plant managers, the message is simple but urgent: start now.
Aligning supplier cost structures with production scheduling isn’t just a back-office optimization; it’s a frontline strategy for boosting profitability, strengthening resilience, and delivering superior customer outcomes.
By integrating advanced APS tools into your ERP and supply chain systems, you unlock the ability to make smarter, faster, and more profitable decisions—turning supplier cost management into a powerful lever for ROI.
Are you ready to take your manufacturing operations to the next level? Contact us today to learn more about how PlanetTogether can help you achieve your goals and drive success in your industry.