Supply Chain Resilience and Risk Management
In the dynamic world of Food and Beverage (F&B) manufacturing, Supply Chain Managers face ever-increasing challenges related to resilience and risk management. Factors such as globalization, climate change and geopolitical tensions have emphasized the need for robust supply chain strategies.
This blog explores the critical role of supply chain resilience and risk management in the F&B industry and how integration between PlanetTogether and leading Enterprise Resource Planning (ERP), Supply Chain Management (SCM), and Manufacturing Execution Systems (MES) can strengthen these vital aspects of your operation.
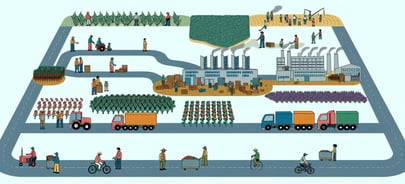
The Importance of Supply Chain Resilience in Food and Beverage Manufacturing
Ensuring Product Availability
One of the primary goals of F&B manufacturers is to maintain a consistent supply of high-quality products to meet consumer demand. Supply chain disruptions, whether due to natural disasters, transportation issues, or other unforeseen events, can lead to product shortages and dissatisfied customers. Supply chain resilience focuses on building adaptive systems that can respond swiftly to such disruptions, minimizing their impact on product availability.
Managing Demand Variability
F&B products often experience seasonal demand fluctuations, promotions, and changing consumer preferences. These variations can pose challenges in production planning and inventory management. A resilient supply chain anticipates and adapts to these changes, ensuring that production remains efficient while meeting market demands.
Mitigating Supply Chain Risks
The F&B industry faces unique risks, including regulatory compliance, food safety, and perishable ingredients. Ensuring the safety and quality of products is paramount. An integrated approach to risk management within the supply chain can help identify and mitigate potential issues before they impact production or reputation.

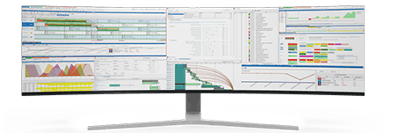
Integration of PlanetTogether with ERP, SCM, and MES Systems
To enhance supply chain resilience and risk management, F&B manufacturers can leverage the power of integration between advanced planning and scheduling software like PlanetTogether and leading ERP, SCM, and MES systems such as SAP, Oracle, Microsoft, Kinaxis, and Aveva. Let's look into the benefits of this integration:
Real-Time Data Exchange
Integration allows for seamless data exchange between PlanetTogether and ERP, SCM, and MES systems. This real-time data flow ensures that all systems have access to the latest information, enabling better decision-making and quicker response to disruptions.
Demand Forecasting and Planning
PlanetTogether's advanced planning and scheduling capabilities can be enriched with demand forecasts and sales data from the ERP system. This integration enables more accurate production planning, ensuring that the right products are produced at the right time to meet customer demands.
Inventory Management
Tight integration between PlanetTogether and the ERP system streamlines inventory management. Manufacturers can optimize inventory levels, reducing carrying costs while ensuring product availability. Alerts can be set up to notify supply chain managers of low inventory levels or potential shortages.
Traceability and Compliance
In the F&B industry, traceability and compliance are crucial. Integration with MES systems ensures that production processes adhere to regulatory standards. Real-time monitoring and data capture help in tracking the production of each batch, ensuring quality and compliance.
Supplier Collaboration
Supply chain resilience extends beyond the manufacturing facility. Integration with SCM systems facilitates collaboration with suppliers. It enables visibility into the supplier network, helping identify potential risks and alternative sourcing options in case of disruptions.
Scenario Planning and Risk Assessment
Integrating PlanetTogether with ERP and SCM systems allows for scenario planning and risk assessment. Manufacturers can simulate various supply chain scenarios and evaluate their impact on production and costs, aiding in risk management strategies.
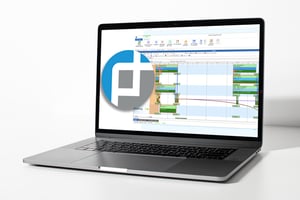
Successful Integration Scenarios
SAP Integration
One of the most popular ERP systems, SAP, can be seamlessly integrated with PlanetTogether. This integration empowers F&B manufacturers with end-to-end visibility, improved demand forecasting, and better production planning.
Oracle Integration
Oracle's robust ERP and SCM solutions can be combined with PlanetTogether to create a resilient supply chain. Manufacturers benefit from enhanced order management, inventory optimization, and compliance tracking.
Microsoft Integration
Microsoft Dynamics ERP and SCM systems can be integrated with PlanetTogether to leverage data analytics for better decision-making. Real-time insights help in managing demand variability and mitigating risks.
Kinaxis Integration
Kinaxis RapidResponse SCM platform, when integrated with PlanetTogether, enables agile supply chain management. Manufacturers can quickly respond to disruptions, ensuring business continuity.
Aveva Integration
Aveva's MES solutions integrate seamlessly with PlanetTogether, providing real-time visibility into production processes. This ensures quality control and compliance with industry regulations.
Supply chain resilience and risk management are critical for the success of Food and Beverage manufacturers. Integration between PlanetTogether and leading ERP, SCM, and MES systems offers a powerful solution to enhance these aspects of your supply chain.
By leveraging real-time data exchange, demand forecasting, inventory optimization, traceability, and scenario planning, F&B manufacturers can build agile and adaptive supply chains that can withstand disruptions and ensure product availability while maintaining compliance and quality standards.
In an era of increasing uncertainty, investing in supply chain resilience through integration is not just a strategic choice; it's a necessity for the survival and growth of F&B manufacturing businesses. Embrace these technologies and approaches to secure a competitive advantage in the ever-evolving landscape of the Food and Beverage industry.
Are you ready to take your manufacturing operations to the next level? Contact us today to learn more about how PlanetTogether can help you achieve your goals and drive success in your industry.