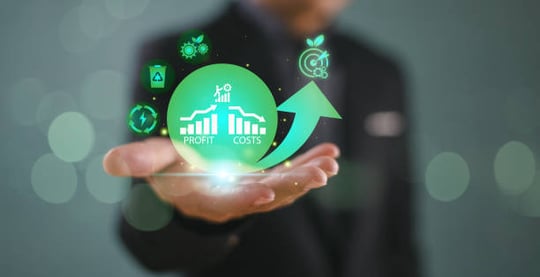
Sustainable Profitability: Balancing Green Goals with Lean Operations Using APS
In chemical manufacturing, Operations Directors face a growing challenge: how to achieve sustainability targets while maintaining — or even improving — profitability. Investors, customers, and regulators increasingly expect chemical producers to reduce emissions, minimize waste, and adopt circular economy principles. Yet at the same time, fierce global competition demands razor-sharp operational efficiency, lean cost structures, and resilient supply chains.
How can chemical manufacturing plants strike the right balance?
Advanced Planning and Scheduling (APS) systems offer a compelling answer. Integrated with powerful enterprise platforms such as SAP, Oracle, Microsoft Dynamics, Kinaxis, or Aveva, APS tools like PlanetTogether allow Operations Directors to align sustainability initiatives directly with lean operational strategies — turning green goals into profitable, competitive advantages.
This blog explores how chemical manufacturers can use APS to achieve sustainable profitability by improving resource efficiency, reducing waste, cutting emissions, and optimizing production schedules — without sacrificing financial performance.
Why Sustainability and Profitability Often Clash
Chemical manufacturing is inherently resource-intensive. It consumes large quantities of raw materials, energy, and water while generating emissions, byproducts, and waste. Historically, sustainability improvements were often seen as added costs:
Installing pollution control systems increases capital and maintenance expenses.
Switching to renewable energy sources raises energy costs.
Redesigning packaging or materials can disrupt well-established production processes.
However, ignoring sustainability risks is no longer an option. Regulatory pressures (such as carbon taxes or emissions caps), reputational risks, and customer demands all push manufacturers to act. But how can Operations Directors ensure that green efforts enhance — rather than erode — the bottom line?
The key lies in integrating sustainability into core production planning and scheduling, where APS plays a transformative role.
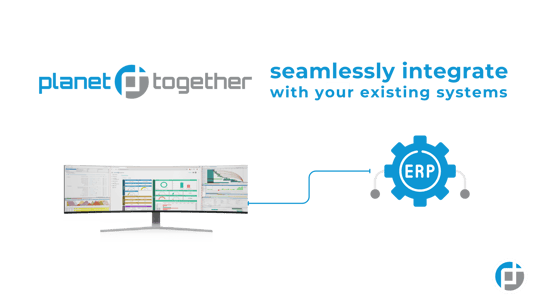
How APS Supports Green and Lean Together
APS systems like PlanetTogether go far beyond basic scheduling. When integrated with ERP, MES, or supply chain systems (like SAP, Oracle, Microsoft Dynamics, Kinaxis, or Aveva), they pull together data from across the plant and enterprise to generate optimized production plans. These plans account for a wide range of constraints and objectives, including:
Machine availability and capacity
Material availability
Labor resources
Energy consumption and peak demand
Emissions limits or caps
Waste generation levels
Delivery deadlines and customer commitments
This enables chemical manufacturers to make sophisticated trade-offs:
Should a plant run longer on lower-emission lines, or faster on less energy-efficient equipment?
Can production be shifted to periods of off-peak renewable energy supply?
Are there opportunities to consolidate batches and reduce cleaning cycles (thereby saving water and chemicals)?
APS integrates sustainability parameters directly into the decision-making process, allowing Operations Directors to balance green and lean goals simultaneously.
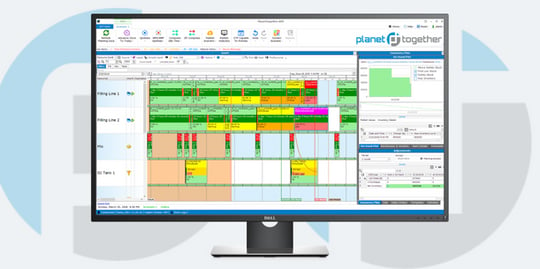
Key Sustainability Benefits Delivered by APS
Here’s where APS systems — particularly when integrated with enterprise tools — deliver tangible sustainability benefits for chemical manufacturers.
Optimized Resource Efficiency
Chemical processes often have variable resource requirements depending on batch size, product mix, and equipment setup. APS helps planners maximize throughput per unit of input — using fewer raw materials, less energy, and less water per ton of finished product.
For example, by sequencing production runs to minimize changeovers, a plant can avoid unnecessary flushing or purging of equipment, saving both materials and cleaning agents. Integrated data from SAP or Oracle systems ensures material availability is aligned with optimal production runs, reducing downtime and waste.
Energy-Aware Scheduling
Energy costs and carbon footprints are increasingly tied to time-of-day pricing and grid emissions intensity. An APS like PlanetTogether, connected with real-time energy data through systems like Aveva, can schedule energy-intensive operations during off-peak hours or when renewable energy supply is highest.
This approach not only cuts electricity bills but also directly lowers the carbon footprint of production, helping Operations Directors meet both financial and environmental goals.
Reduced Waste and Emissions
Chemical manufacturing waste often comes from inefficient production runs, scrap, rework, and off-spec materials. APS enables more precise scheduling to align production batches with exact customer demands, reducing the risk of overproduction.
Furthermore, by tightly integrating with quality management modules within SAP, Microsoft Dynamics, or Kinaxis, APS ensures quality thresholds are met consistently, avoiding the environmental and financial cost of scrapped materials.
Scenario Planning for Sustainability Investments
Should the plant invest in a new low-emission reactor or upgrade its energy recovery systems? APS allows Operations Directors to run simulations, modeling how changes in production equipment, materials, or processes would impact schedules, costs, and emissions.
Integrated data flows between PlanetTogether and ERP systems ensure that decisions are grounded in both operational realities and financial performance. This empowers leadership to make sustainability investments that truly deliver ROI.
Circular Economy and Closed-Loop Production
Many chemical manufacturers are exploring circular economy strategies — such as using recycled feedstocks or recovering byproducts for reuse. APS systems play a vital role here, coordinating material flows, tracking availability, and scheduling production runs that incorporate reclaimed materials without disrupting primary product lines.
Integration with supply chain systems (like Kinaxis or Oracle) ensures that circular material streams are aligned with external supplier and customer requirements, supporting both sustainability goals and supply chain continuity.
Leaner and Greener Through Integration
Consider a midsize specialty chemicals plant facing rising energy costs and new regional emissions targets. By integrating PlanetTogether APS with its SAP ERP system, the operations team gained a unified view of production constraints, material flows, and energy usage patterns.
With APS-driven scheduling, they identified opportunities to:
Shift energy-intensive production runs to nights and weekends, when electricity was cheaper and grid emissions were lower.
Consolidate similar product batches to reduce cleaning cycles and water consumption.
Prioritize the use of recycled raw materials when available, supported by real-time inventory data from SAP.
The result? A 12% reduction in energy costs, a 15% cut in water use, and a 10% drop in Scope 1 and Scope 2 emissions — all while improving on-time delivery performance by 8%.
This example shows how integrating APS with enterprise platforms creates a powerful lever for sustainable profitability.
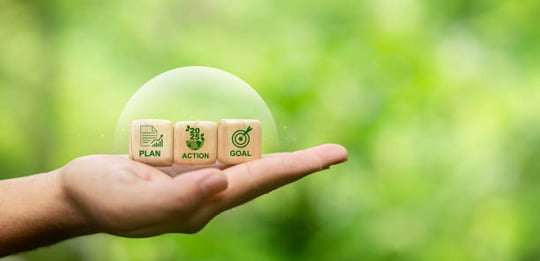
The Operations Director’s Roadmap
For Operations Directors in chemical manufacturing, achieving sustainable profitability with APS starts with three critical steps:
Assess Current Baselines: Understand where the plant’s key resource, energy, and emissions hotspots are. Integrate data from ERP, MES, and energy management systems to create a unified view.
Define Integrated Objectives: Work with sustainability, finance, and supply chain leaders to set combined green and lean goals. Ensure these are incorporated as parameters into the APS.
Leverage APS Optimization: Use PlanetTogether and similar systems to generate optimized production plans that account for both operational efficiency and environmental performance — making data-driven trade-offs visible to leadership.
Chemical manufacturing is at a crossroads. Companies that treat sustainability as a regulatory burden or a cost center will struggle to compete in a rapidly changing marketplace. But those that embrace sustainable profitability — using tools like PlanetTogether APS integrated with enterprise platforms — can unlock significant advantages: lower costs, reduced risks, improved brand reputation, and greater resilience.
For Operations Directors, the message is clear: sustainability and profitability are not opposing forces. With the right technologies and integrated planning, they can become mutually reinforcing drivers of long-term success.
Are you ready to take your manufacturing operations to the next level? Contact us today to learn more about how PlanetTogether can help you achieve your goals and drive success in your industry.