Key to Production Flow Optimization
The quest for operational excellence is an ongoing journey, and at the heart of it lies production flow optimization. In Food and Beverage manufacturing, where consumer demands fluctuate, supply chain disruptions are common, and competition is fierce, the role of an Operations Director is pivotal.
In this blog, we look into the strategies, technologies, and integrations that can empower Operations Directors to streamline processes and enhance efficiency, with a special focus on the integration between PlanetTogether and leading ERP, SCM, and MES systems.
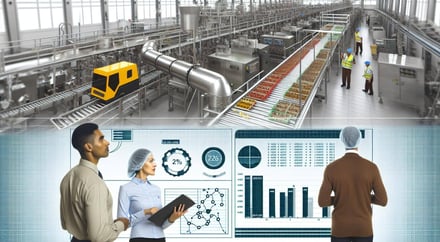
Production Flow Optimization
Production flow optimization is more than just maximizing throughput; it's about orchestrating a seamless journey for raw materials to finished goods while minimizing waste, reducing costs, and meeting quality standards. It involves a holistic approach that encompasses planning, scheduling, execution, and continuous improvement.
Challenges in Food and Beverage Manufacturing
The Food and Beverage industry presents unique challenges, including perishable raw materials, stringent regulatory requirements, seasonality, and volatile consumer preferences. These challenges amplify the complexity of production flow optimization, requiring agile and adaptive strategies.

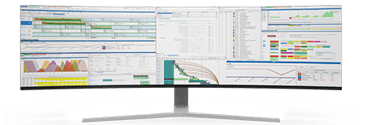
Integration as the Key to Efficiency
Integrating production planning and scheduling tools like PlanetTogether with ERP, SCM, and MES systems is a game-changer for Operations Directors. It enables real-time data exchange, seamless communication, and synchronized operations across different functions, leading to enhanced visibility, accuracy, and decision-making capabilities.
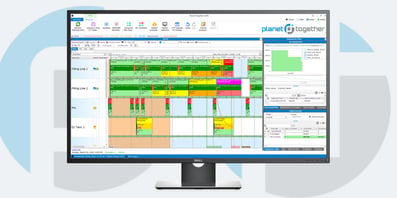
PlanetTogether Integration with Leading Systems
Among the myriad of integration possibilities, integrating PlanetTogether with top-tier ERP, SCM, and MES systems such as SAP, Oracle, Microsoft Dynamics, Kinaxis, and Aveva stands out. Let's explore how these integrations contribute to production flow optimization:
SAP Integration: SAP's robust ERP system combined with PlanetTogether's advanced planning capabilities creates a unified platform for end-to-end production management. The integration facilitates synchronized demand forecasting, inventory optimization, and resource planning, enabling Operations Directors to align production schedules with market demand seamlessly.
Oracle Integration: Oracle's comprehensive suite of SCM solutions integrated with PlanetTogether streamlines supply chain operations, from procurement to distribution. By leveraging real-time data exchange between Oracle and PlanetTogether, Operations Directors gain agility in adapting to changes, optimizing inventory levels, and minimizing lead times, ultimately enhancing production flow efficiency.
Microsoft Dynamics Integration: Microsoft Dynamics ERP, coupled with PlanetTogether's scheduling prowess, empowers Operations Directors with actionable insights for efficient resource allocation, capacity planning, and production scheduling. The integration fosters collaboration across departments, enabling faster decision-making and improved response to customer demands.
Kinaxis Integration: Kinaxis' RapidResponse SCM platform integrated with PlanetTogether facilitates end-to-end visibility and agility in production planning and execution. With synchronized data flows between Kinaxis and PlanetTogether, Operations Directors can dynamically adjust production schedules, mitigate risks, and capitalize on opportunities, driving continuous improvement in production flow.
Aveva Integration: Aveva's MES solutions integrated with PlanetTogether enable seamless coordination between production planning and shop floor execution. The integration ensures real-time tracking of production progress, quality control, and performance monitoring, empowering Operations Directors to optimize resource utilization, minimize downtime, and enhance overall productivity.
Benefits of Integration
The integration between PlanetTogether and leading ERP, SCM, and MES systems offers a plethora of benefits for Operations Directors:
Enhanced Visibility: Real-time data synchronization provides a holistic view of operations, enabling proactive decision-making and rapid response to changes.
Improved Accuracy: Integrated systems eliminate data silos and reduce manual errors, ensuring consistency and reliability in planning and execution.
Streamlined Operations: Seamless communication between systems streamlines workflows, minimizes lead times, and optimizes resource utilization.
Agile Adaptation: Integrated systems enable flexibility to adapt to changing market dynamics, customer demands, and supply chain disruptions.
Continuous Improvement: Data-driven insights and analytics support continuous improvement initiatives, driving efficiency gains and cost savings over time.
Production flow optimization is not a one-time endeavor but a continuous pursuit of excellence. By leveraging the integration between PlanetTogether and leading ERP, SCM, and MES systems, Operations Directors in Food and Beverage manufacturing can unlock new levels of efficiency, agility, and competitiveness.
Embracing technology-enabled solutions and collaborative approaches is the pathway to achieving operational excellence and staying ahead in today's dynamic marketplace.
Are you ready to take your manufacturing operations to the next level? Contact us today to learn more about how PlanetTogether can help you achieve your goals and drive success in your industry.