Constraint-Based Scheduling
Every aspect of the production process must be finely tuned to ensure that life-saving devices and medications reach those in need as quickly and reliably as possible. At the heart of this optimization lies production scheduling—a critical component that orchestrates the flow of resources and tasks to meet demand while minimizing costs and maximizing throughput.
For Production Schedulers in medical manufacturing facilities, the challenges are numerous. Balancing complex production requirements, tight deadlines, and limited resources can often feel like navigating a maze. However, there is a beacon of hope amidst this complexity: constraint-based scheduling approaches.
In this blog, we will look into the intricacies of constraint-based scheduling and explore how integrating advanced scheduling software like PlanetTogether with ERP, SCM, and MES systems such as SAP, Oracle, Microsoft, Kinaxis, Aveva, and others can revolutionize production planning and execution in medical manufacturing facilities.
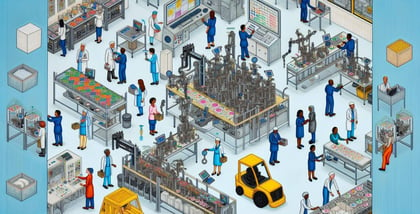
Understanding Constraint-Based Scheduling
At its core, constraint-based scheduling is a methodology that focuses on identifying and managing constraints within the production process to optimize throughput. Unlike traditional scheduling methods that rely on fixed intervals or arbitrary priorities, constraint-based scheduling dynamically adjusts schedules based on the availability of critical resources, such as machines, materials, and manpower.
The key principles of constraint-based scheduling include:
Identifying Constraints: The first step in constraint-based scheduling is identifying the bottlenecks or constraints within the production process. These constraints can vary from machine capacity limitations to material shortages or labor constraints.
Exploiting Constraints: Once identified, constraints must be exploited to their fullest potential. This may involve prioritizing tasks that utilize constrained resources efficiently or adjusting schedules to minimize idle time.
Subordinating Non-Constraints: Tasks that do not directly impact the constraints should be subordinated to ensure that the limited resources are allocated optimally. This may involve rescheduling non-critical tasks or adjusting production sequences to maximize throughput.
Elevating Constraints: In some cases, constraints may be alleviated through investment in additional resources or process improvements. Constraint-based scheduling helps identify opportunities for capacity expansion or process optimization to elevate constraints and increase overall throughput.
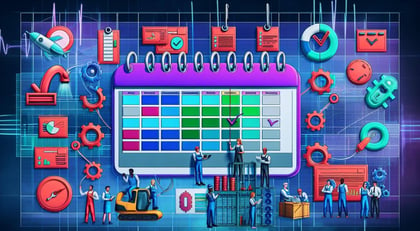
Benefits of Constraint-Based Scheduling
The adoption of constraint-based scheduling offers a myriad of benefits for medical manufacturing facilities:
Increased Throughput: By optimizing resource utilization and minimizing idle time, constraint-based scheduling maximizes throughput, allowing facilities to meet demand more efficiently.
Reduced Lead Times: The dynamic nature of constraint-based scheduling enables facilities to respond quickly to changes in demand or production conditions, resulting in shorter lead times and improved customer satisfaction.
Improved Resource Utilization: By aligning production schedules with resource availability, constraint-based scheduling minimizes waste and inefficiency, leading to better utilization of machines, materials, and manpower.
Enhanced Visibility and Control: Advanced scheduling software like PlanetTogether provides real-time visibility into production schedules, allowing Production Schedulers to monitor progress, identify bottlenecks, and make data-driven decisions to optimize operations.
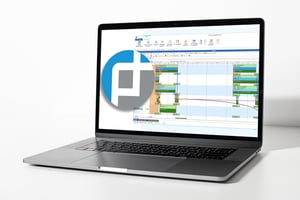
Integrating PlanetTogether with ERP, SCM, and MES Systems
While constraint-based scheduling offers significant advantages on its own, its true potential is realized when integrated with other enterprise systems such as ERP, SCM, and MES. Integration between scheduling software like PlanetTogether and ERP systems like SAP, Oracle, Microsoft Dynamics, or MES systems like Aveva or Kinaxis enables seamless data exchange and synchronization, facilitating a holistic approach to production planning and execution.
Here's how integration between PlanetTogether and ERP, SCM, and MES systems enhances the effectiveness of constraint-based scheduling:
Real-Time Data Exchange: Integration enables real-time exchange of production data between scheduling software and ERP, SCM, and MES systems, ensuring that schedules are always based on the latest information.
Improved Accuracy and Consistency: By eliminating manual data entry and discrepancies between systems, integration enhances the accuracy and consistency of production schedules, reducing errors and improving overall efficiency.
Enhanced Decision-Making: Access to integrated data allows Production Schedulers to make informed decisions based on comprehensive insights into production, inventory, and resource availability, leading to better outcomes and increased agility.
Streamlined Workflows: Integration streamlines workflows by automating processes such as order entry, inventory management, and production scheduling, reducing administrative overhead and freeing up time for more strategic tasks.
Scalability and Flexibility: Integrated systems are scalable and adaptable to evolving business needs, enabling medical manufacturing facilities to grow and innovate without being constrained by outdated or siloed systems.
In the competitive landscape of medical manufacturing, efficiency is key to success. Constraint-based scheduling offers a powerful approach to optimizing production operations, maximizing throughput, and meeting customer demand with minimal waste.
By integrating advanced scheduling software like PlanetTogether with ERP, SCM, and MES systems, medical manufacturing facilities can unlock the full potential of constraint-based scheduling, gaining real-time visibility, improving decision-making, and streamlining workflows for enhanced efficiency and agility.
Embracing constraint-based scheduling and leveraging integration between scheduling software and enterprise systems is essential for medical manufacturing facilities striving to stay ahead in today's dynamic marketplace.
Are you ready to take your manufacturing operations to the next level? Contact us today to learn more about how PlanetTogether can help you achieve your goals and drive success in your industry.