Overall Equipment Effectiveness (OEE) is by far one of the most beneficial metrics when it pertains to understanding downtime, efficiency, and ultimately how much you could save in the long term based off of potential new investments. Overall Equipment Effectiveness (OEE) is a must for any manufacturing operation that is seeking to understand what areas that they are lacking in – and how to come up with a solution for them.
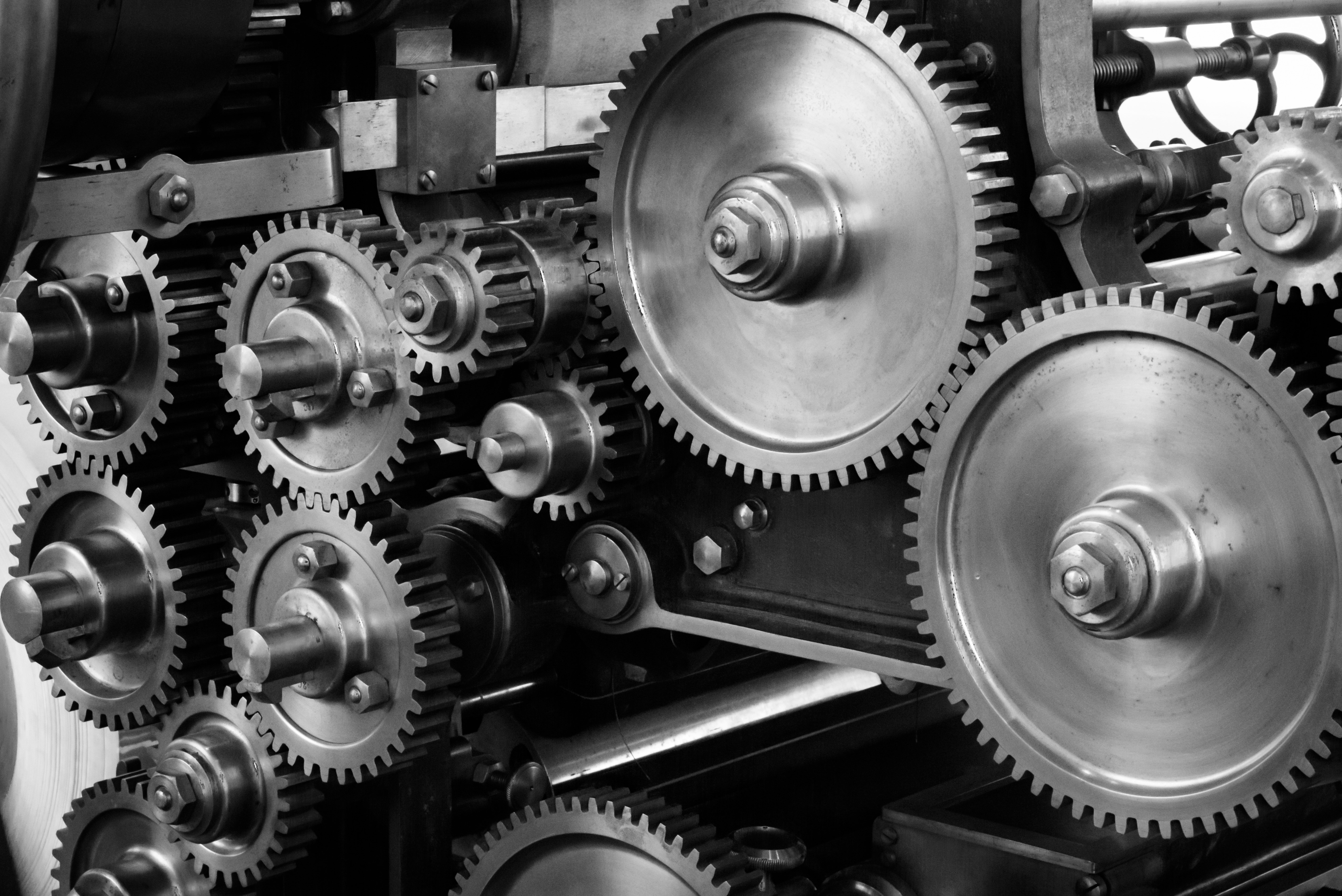
You can use OEE as a financial key performance indicator (KPI), which will ultimately enable you to understand other metrics such as ROI, profit savings, and more. These savings and earnings are a must to locate when attempting to maximize efficiency within your operation and ensure that everything is on track. With OEE, what are some of the areas that are able to measured and enhanced?
OEE Measurements and Increasing the Percentage
OEE measurements include availability, performance, and quality. Quality is by far one of the most important metrics to oversee, considering that quality issues can lead to issues in the other areas such as availability and performance. For example, if you are producing non-quality products and creating issues on the assembly line with broken parts or any other error pertaining to the product, and your workers are taking a decent amount of time to deal with the issue – this can lead to a large percentage of your downtime. Every second, minute, or hour that equipment or product is waiting on the line due to errors or mishaps is downtime, which is costing you money in the long run. Increasing your OEE percentage will only be possible through taking a look at the root issues on the line and what exactly is causing so much downtime. Once this is conducted and dealt with, you should see a substantial increase in your OEE percentage.
Inventory Level Reduction
Inventory levels are costly, no matter what business you may be a part of. Any excess inventory is costing you money – but it is necessary for some. Inventory allows you to quickly deliver product the second that a customer presses the “buy” button and gets it to their front door in no time. This can be seen with any warehouse based business, such as Amazon. While inventory is essential at times, there are ways to get it down and more precise. OEE can emphasize areas that are not being utilized and allow you to develop a better understanding of how much inventory is costing you. If you are not consistently producing product and having a continuous flow in and out, then maybe consider producing less and holding less inventory within a given timeframe. Utilizing adequate forecasting and having concise information pertaining to inventory is also a must.
A software that can aid with understanding how effective your equipment and operation is would be PlanetTogether’s Advanced Planning and Scheduling (APS) Software. Advanced Planning and Scheduling (APS) Software is a must for manufacturing operations that are seeking to enhance their efficiency and improve overall operations. Advanced Planning and Scheduling Software will enable manufacturers to develop a competitive edge and stay ahead of the game.
Advanced Planning and Scheduling Software
Advanced Planning and Scheduling (APS) software has become a must for modern-day manufacturing operations due to customer demand for increased product mix and fast delivery combined with downward cost pressures. APS can be quickly integrated with a ERP/MRP software to fill gaps where these system lack planning and scheduling flexibility and accuracy. Advanced Planning and Scheduling (APS) helps planners save time while providing greater agility in updating ever-changing priorities, production schedules, and inventory plans.
- Create optimized schedules balancing production efficiency and delivery performance
- Maximize output on bottleneck resources to increase revenue
- Synchronize supply with demand to reduce inventories
- Provide company-wide visibility to capacity
- Enable scenario data-driven decision making
Implementation of Advanced Planning and Scheduling (APS) software will take your manufacturing operations to the next level of production efficiency, taking advantage of the operational data you already have in your ERP.
Related Capacity Planning Video
APS Resources