When dealing with inventory and order fulfillment, it is important to have a distribution center and warehouse. While having a warehouse to store inventory sounds simple enough, there are a substantial amount of cost in holding this inventory and it is important to be able to rid yourself of it as soon as possible.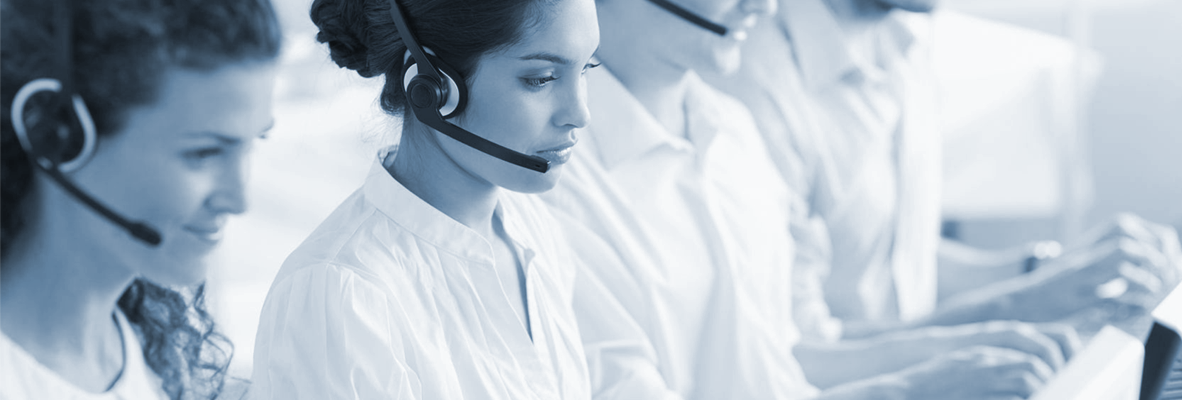
A way that can aid with the flow of product and inventory is planning out your warehouse or distribution center. Successfully planning out your distribution center should aid with moving product rather quickly and ensuring that costs are driven down while profitability is driven up. There are various benefits pertaining to planning your distribution center and in this blog we are going to discuss the four steps to successfully planning a distribution center.
Four Steps to Planning a Distribution Center
The five steps to adequately aid with planning a new distribution center pertain to the following:
- Prioritize Main Objectives - In order to know exactly what you’re looking for in a new facility it is essential to become clear about what any current plan points are. You should start by framing out goals and creating a foundation for the new space in terms of any project future growth. Then, take notes on how many SKUs you will have and flesh out any capacity needs. Once this is completed, you are then able to start singling out key objectives such as cost reduction, productivity increase, and improving customer service.
- Collect Data - Collecting data is essential for any step within any process or planning stage. When you are considering a new space, it is extremely important to understand and document as much as possible. Ensure that physical elements of the space, the layout, internal configurations, material flows, and other components are accounted for and noted. The second critical aspect pertains to internal data. Gather any relevant product information from the amount, size, and weight of SKUs to your order history and activity logs.
- Run Quantitative and Qualitative Analysis - It is also important to ensure that space aligns with stated goals and objectives before pressing forward with a solid plan. Otherwise, you may find yourself wasting valuable time and resources creating modifications that are unnecessary in the design process. In your quantitative analysis, you should focus on aspects such as flows, picking and storage modules, staffing, and other. Qualitatively look at things such as maintenance, automation, required training, and implementation difficulty.
- Finalize Plans - Finally, it is time to finalize your plans. You will need to make a case for as to why moving to a new distribution center is the right move for your warehouse operation. This is the stage of the project when you should have the final layout mockups. Review these aspects carefully before signing off and they will determine how best to coordinate the arrival of essential products. Take your time in ensuring that all design specifications have been implemented according to the plan and the facility is secured.
A software that can aid with planning production and the process pertaining to a distribution center is PlanetTogether’s Advanced Planning and Scheduling (APS) Software. Advanced Planning and Scheduling (APS) Software offers thorough visibility into a manufacturing operation and can aid production tremendously through cutting costs and improving profitability. PlanetTogether’s Advanced Planning and Scheduling (APS) Software is a must for manufacturers that are seeking to enhance their production process and ultimately eliminate waste and achieve continuous improvement. APS also is important for production facilities that are seeking to achieve a competitive advantage and get ahead of others within their particular industry.
Advanced Planning and Scheduling Software
Advanced Planning and Scheduling (APS) software has become a must for modern-day manufacturing operations due to customer demand for increased product mix and fast delivery combined with downward cost pressures. APS can be quickly integrated with a ERP/MRP software to fill gaps where these system lack planning and scheduling flexibility and accuracy. Advanced Planning and Scheduling (APS) helps planners save time while providing greater agility in updating ever-changing priorities, production schedules, and inventory plans.
- Create optimized schedules balancing production efficiency and delivery performance
- Maximize output on bottleneck resources to increase revenue
- Synchronize supply with demand to reduce inventories
- Provide company-wide visibility to capacity
- Enable scenario data-driven decision making
Implementation of Advanced Planning and Scheduling (APS) software will take your manufacturing operations to the next level of production efficiency, taking advantage of the operational data you already have in your ERP.
Related Capacity Planning Video
APS Resources