Continuous Improvement in Manufacturing Scheduling
As an Operations Director, you bear the responsibility of overseeing every aspect of your facility's operations, with manufacturing scheduling playing a pivotal role.
In this blog, we'll explore the importance of continuous improvement in manufacturing scheduling and how integrating PlanetTogether with ERP, SCM, and MES systems like SAP, Oracle, Microsoft, Kinaxis, Aveva, and others can be the key to achieving operational excellence in your packaging manufacturing facility.
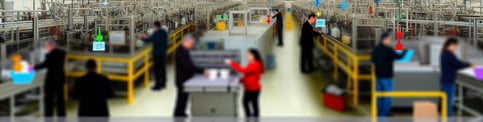
The Challenge of Manufacturing Scheduling
Efficient manufacturing scheduling is a multifaceted challenge, particularly in the packaging industry. Operations Directors often encounter various hurdles, including:
Complexity of Production Lines: Packaging facilities typically have a wide range of product types and production lines, each with its own unique requirements and constraints.
Resource Optimization: Maximizing the use of resources such as equipment, labor, and materials is essential to reducing costs and improving profitability.
Inventory Management: Balancing inventory levels to meet customer demand while avoiding overstocking or stockouts can be a delicate balancing act.
Changing Market Dynamics: Consumer preferences and market demands are constantly evolving, requiring flexibility in production scheduling.
Compliance and Quality: Packaging must meet regulatory standards and quality requirements. Ensuring that schedules align with compliance standards is critical.
Customer Expectations: Meeting delivery deadlines is crucial for customer satisfaction and maintaining long-term partnerships.
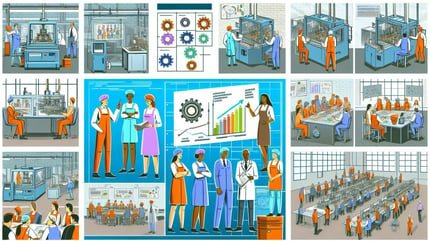
Why Continuous Improvement Matters
Continuous improvement in manufacturing scheduling is not just a goal; it's a necessity. Here's why Operations Directors should prioritize it:
Cost Reduction: Improved scheduling reduces downtime, minimizes resource wastage, and optimizes inventory levels, resulting in significant cost savings.
Enhanced Efficiency: Efficient schedules ensure that production lines operate at their maximum capacity, increasing output without increasing resource consumption.
Better Resource Utilization: Continuous improvement identifies opportunities to optimize resource allocation, leading to more efficient use of equipment, labor, and materials.
Adaptability: The ability to quickly adjust schedules in response to market changes or unforeseen events is crucial to maintaining competitiveness.
Quality Assurance: Effective scheduling helps ensure that quality standards and compliance requirements are consistently met.
Improved Customer Satisfaction: Meeting delivery timelines and responding to customer demand fluctuations lead to higher customer satisfaction levels.

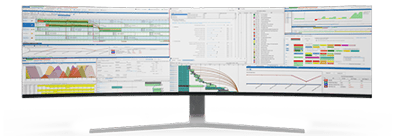
Integration with Leading ERP, SCM, and MES Systems
Now, let's explore how integrating PlanetTogether with some of the leading ERP, SCM, and MES systems can elevate your packaging manufacturing facility's continuous improvement journey:
Integration with SAP: SAP offers robust ERP solutions. By integrating with PlanetTogether, you can synchronize manufacturing schedules with SAP's resource planning capabilities, leading to efficient resource allocation and better order fulfillment.
Integration with Oracle: Oracle's SCM solutions are renowned for supply chain optimization. Integration with PlanetTogether allows you to align manufacturing schedules with Oracle's supply chain data, optimizing inventory levels and reducing lead times.
Integration with Microsoft Dynamics: Microsoft Dynamics ERP and CRM systems can be seamlessly integrated with PlanetTogether to provide a comprehensive view of your operations. This integration enhances data accuracy and simplifies decision-making.
Integration with Kinaxis RapidResponse: Kinaxis RapidResponse is a supply chain management platform. Integrating it with PlanetTogether ensures that your manufacturing schedules are always aligned with supply chain dynamics, minimizing disruptions.
Integration with Aveva MES: Aveva MES is a leading manufacturing execution system. By integrating it with PlanetTogether, you can achieve real-time visibility into shop floor operations and synchronize manufacturing schedules with actual production progress.
Integration with Other ERP, SCM, and MES Systems: Depending on your specific needs and existing systems, PlanetTogether can be integrated with a wide range of ERP, SCM, and MES systems to facilitate continuous improvement in manufacturing scheduling.
Continuous improvement in manufacturing scheduling is the cornerstone of operational excellence in packaging manufacturing facilities. As an Operations Director, integrating advanced manufacturing scheduling software like PlanetTogether with your existing ERP, SCM, and MES systems is a strategic move that can significantly enhance your facility's efficiency.
By optimizing resource allocation, reducing costs, enhancing efficiency, and ensuring compliance and quality, integration empowers you to overcome the unique challenges of packaging manufacturing. Whether you choose to integrate with SAP, Oracle, Microsoft, Kinaxis, Aveva, or other systems, the result will be a well-orchestrated manufacturing schedule that drives cost-effectiveness, meets customer expectations, and fosters continuous improvement in your packaging manufacturing facility.
Are you ready to take your manufacturing operations to the next level? Contact us today to learn more about how PlanetTogether can help you achieve your goals and drive success in your industry.
Embrace the future of manufacturing scheduling, and watch your facility thrive in a dynamic and competitive landscape.