Advanced Manufacturing Technologies for Personalized and Customized Products
The demand for personalized and customized products is ever-growing in the food and beverage industry. Consumers are seeking unique experiences tailored to their preferences, leading to a paradigm shift in manufacturing practices. Production planners in the food and beverage industry are tasked with meeting these demands while ensuring operational efficiency and cost-effectiveness.
Fortunately, the integration of advanced manufacturing technologies, coupled with robust planning systems like PlanetTogether and ERP solutions such as SAP, Oracle, Microsoft, Kinaxis, Aveva, and others, presents a promising solution.
In this blog, we will explore the challenges faced by production planners in implementing advanced manufacturing technologies for personalized and customized products. We will also delve into the integration between PlanetTogether and leading ERP, SCM, and MES systems, highlighting the benefits and best practices for seamless collaboration. Let's embark on this journey towards maximizing production efficiency and meeting the evolving needs of consumers.
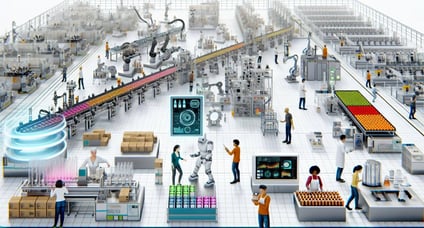
Implementing Advanced Manufacturing Technologies
Complexity in Product Variability: Personalized and customized products introduce complexity into the manufacturing process. Each variant requires specific ingredients, packaging, and production parameters, making scheduling and planning more intricate.
Demand Volatility: Fluctuating consumer preferences and market trends contribute to demand volatility. Production planners must adapt quickly to these changes while minimizing disruptions to the supply chain.
Efficient Resource Utilization: Optimizing resource utilization, including raw materials, equipment, and labor, is crucial for maintaining profitability. However, traditional manufacturing approaches may not suffice in accommodating the diverse requirements of personalized products.
Quality Control and Compliance: Maintaining consistent quality standards and regulatory compliance is paramount in the food and beverage industry. Ensuring traceability and adherence to safety protocols becomes more challenging with increased product customization.
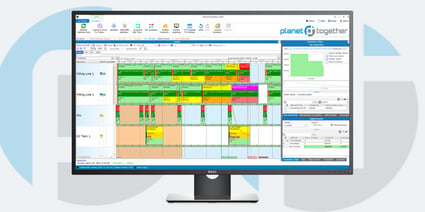
Integration between PlanetTogether and ERP/SCM/MES Systems
Integration between advanced planning tools like PlanetTogether and ERP, SCM, and MES systems is essential for streamlining operations and achieving end-to-end visibility. Here's how the integration can benefit production planners:
Real-time Data Exchange: Seamless integration facilitates real-time data exchange between planning and execution systems. This enables production planners to access up-to-date information on inventory levels, production schedules, and order status, allowing for better decision-making.
Improved Accuracy and Efficiency: By eliminating manual data entry and synchronizing information across systems, integration enhances accuracy and efficiency in planning processes. Production planners can create optimized schedules that account for resource availability, lead times, and customer demand.
Enhanced Collaboration: Integrated systems foster collaboration among cross-functional teams, including production, procurement, and logistics. Shared visibility into production plans and inventory levels enables stakeholders to align their activities and respond effectively to changes in demand or supply.
Scalability and Flexibility: As businesses scale and diversify their product offerings, integrated systems provide the scalability and flexibility needed to adapt to evolving requirements. Whether launching new products or expanding into new markets, production planners can leverage the combined capabilities of planning and ERP/SCM/MES systems.
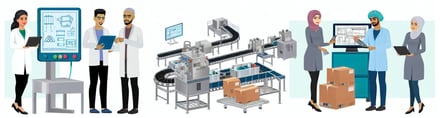
Best Practices for Seamless Collaboration
To maximize the benefits of integration between PlanetTogether and ERP/SCM/MES systems, production planners should consider the following best practices:
Define Clear Integration Objectives: Clearly define the objectives and expected outcomes of the integration initiative, aligning them with the organization's strategic goals. Identify key performance indicators (KPIs) to measure success, such as on-time delivery, inventory turnover, and production efficiency.
Standardize Data Formats and Processes: Establish standardized data formats and processes to facilitate smooth data exchange between systems. Ensure compatibility between the data structures used by PlanetTogether and the integrated ERP/SCM/MES systems, minimizing the need for custom mappings or transformations.
Implement Robust Change Management: Engage stakeholders from across the organization early in the integration process and communicate the benefits of collaboration. Provide training and support to users to ensure they are proficient in utilizing the integrated systems effectively.
Monitor Performance and Continuously Improve: Regularly monitor the performance of the integrated systems and identify areas for improvement. Collect feedback from users and stakeholders to identify pain points and implement enhancements iteratively.
The implementation of advanced manufacturing technologies for personalized and customized products presents both challenges and opportunities for production planners in the food and beverage industry. By integrating tools like PlanetTogether with leading ERP, SCM, and MES systems, organizations can overcome these challenges and unlock new levels of efficiency and agility.
Seamless collaboration between planning and execution systems enables production planners to optimize resource utilization, improve responsiveness to changing demand, and ensure compliance with quality and regulatory standards. By adhering to best practices for integration and collaboration, businesses can stay ahead of the curve and deliver exceptional value to customers in an increasingly competitive marketplace.
As the landscape of manufacturing continues to evolve, embracing advanced technologies and fostering synergies between planning and execution processes will be crucial for success. Production planners who embrace this paradigm shift will not only meet the demands of personalized and customized products but also drive innovation and growth within their organizations.
Are you ready to take your manufacturing operations to the next level? Contact us today to learn more about how PlanetTogether can help you achieve your goals and drive success in your industry.