The Power of Predictive Quality Assurance Scheduling
Operations directors are constantly seeking innovative solutions to optimize their processes in chemical manufacturing. One such solution gaining traction is predictive quality assurance scheduling, a sophisticated approach that blends advanced scheduling techniques with predictive analytics.
In this blog, we'll look into the significance of predictive quality assurance scheduling for chemical manufacturing facilities, exploring its benefits, implementation challenges, and the integration potential with leading enterprise resource planning (ERP), supply chain management (SCM), and manufacturing execution systems (MES) such as SAP, Oracle, Microsoft, Kinaxis, and Aveva.
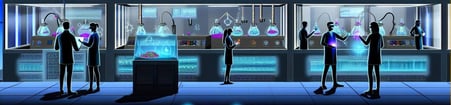
Predictive Quality Assurance Scheduling
Predictive quality assurance scheduling represents a paradigm shift in how chemical manufacturing facilities approach production planning and quality control. Traditionally, scheduling and quality assurance have been treated as separate functions, often leading to inefficiencies, production bottlenecks, and quality issues. However, predictive quality assurance scheduling integrates these two critical aspects, leveraging real-time data, predictive analytics, and advanced algorithms to optimize production schedules while ensuring consistent product quality.
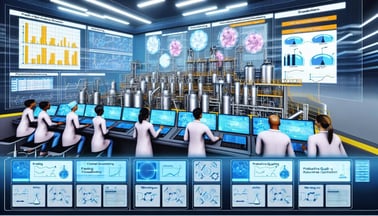
Benefits of Predictive Quality Assurance Scheduling
Enhanced Efficiency: By incorporating predictive analytics into scheduling processes, operations directors can anticipate potential quality issues and adjust production schedules proactively. This foresight minimizes the risk of costly delays and disruptions, allowing for smoother operations and improved resource utilization.
Improved Quality Control: Predictive quality assurance scheduling enables tighter control over production variables, such as raw material quality, environmental conditions, and equipment performance. By identifying potential quality deviations early in the process, manufacturers can take corrective actions swiftly, maintaining product quality standards and reducing waste.
Optimal Resource Allocation: Through advanced scheduling algorithms, predictive quality assurance scheduling optimizes the allocation of resources, including manpower, equipment, and materials. By aligning production schedules with resource availability and demand fluctuations, operations directors can minimize idle time, maximize throughput, and reduce overall production costs.
Regulatory Compliance: In the highly regulated chemical industry, compliance with stringent quality and safety standards is non-negotiable. Predictive quality assurance scheduling facilitates compliance by providing real-time visibility into production processes, enabling timely adjustments to meet regulatory requirements and quality certifications.
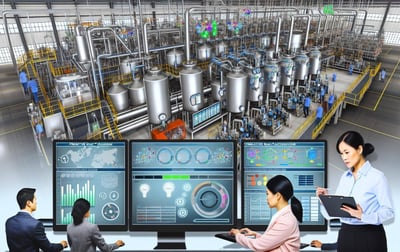
Implementation Challenges
While the benefits of predictive quality assurance scheduling are compelling, implementing this advanced approach comes with its set of challenges:
Data Integration: Integrating disparate data sources from ERP, SCM, MES, and quality management systems is essential for predictive analytics to deliver actionable insights. Operations directors must ensure seamless data integration to enable accurate forecasting and decision-making.
Model Complexity: Developing predictive models that account for various production factors, quality parameters, and external variables can be complex. Operations directors may need to collaborate with data scientists or leverage specialized software solutions to build robust predictive models tailored to their manufacturing processes.
Change Management: Introducing predictive quality assurance scheduling requires a cultural shift within the organization, as employees accustomed to traditional scheduling methods may resist change. Effective change management strategies, including training programs and stakeholder engagement, are crucial for successful implementation.
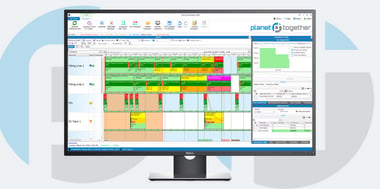
Integration with ERP, SCM, and MES Systems
To fully harness the potential of predictive quality assurance scheduling, integration with leading ERP, SCM, and MES systems is imperative. Platforms such as SAP, Oracle, Microsoft Dynamics, Kinaxis RapidResponse, and Aveva MES offer robust capabilities for data management, production planning, and quality control. By integrating these systems with predictive analytics tools like PlanetTogether, operations directors can unlock synergies that drive operational excellence:
SAP Integration: SAP's comprehensive suite of ERP and SCM solutions provides a solid foundation for predictive quality assurance scheduling. Integration with PlanetTogether allows operations directors to leverage SAP's data-rich environment for predictive analytics, streamlining scheduling processes and enhancing overall efficiency.
Oracle Integration: Oracle's advanced SCM and MES capabilities complement predictive quality assurance scheduling by providing real-time visibility into supply chain operations. By integrating with PlanetTogether, Oracle users can optimize production schedules based on predictive insights, driving continuous improvement and agility.
Microsoft Dynamics Integration: Microsoft Dynamics offers a flexible platform for ERP and SCM, enabling seamless integration with PlanetTogether for predictive quality assurance scheduling. Operations directors can leverage Microsoft's familiar interface and robust analytical tools to enhance scheduling accuracy and responsiveness.
Kinaxis RapidResponse Integration: Kinaxis RapidResponse's cloud-based SCM platform offers agility and scalability for dynamic manufacturing environments. Integration with PlanetTogether empowers operations directors to synchronize production schedules with demand signals, enabling proactive quality assurance and resource optimization.
Aveva MES Integration: Aveva MES provides comprehensive manufacturing execution capabilities, including quality management and production scheduling. By integrating with PlanetTogether, Aveva MES users can leverage predictive analytics to optimize production schedules while maintaining stringent quality standards.
In the competitive landscape of chemical manufacturing, predictive quality assurance scheduling emerges as a game-changer for operations directors striving to balance efficiency, quality, and compliance. By integrating advanced scheduling techniques with predictive analytics and leveraging leading ERP, SCM, and MES systems, operations directors can unlock new levels of efficiency, agility, and resilience in their manufacturing operations.
As the industry continues to evolve, embracing predictive quality assurance scheduling will be essential for staying ahead of the curve and driving sustainable growth. Are you ready to take your manufacturing operations to the next level? Contact us today to learn more about how PlanetTogether can help you achieve your goals and drive success in your industry.