Predictive Quality Control Systems
Each batch must meet rigorous standards to guarantee safety, efficacy, and customer satisfaction. Traditionally, quality control has been a reactive process, with inspections and tests conducted after production. However, the landscape is rapidly evolving, with the emergence of predictive quality control systems reshaping the industry.
In this blog, we look into the significance of predictive quality control systems for production planners in chemical manufacturing facilities, exploring how integration with enterprise resource planning (ERP), supply chain management (SCM), and manufacturing execution systems (MES) platforms like PlanetTogether and SAP, Oracle, Microsoft, Kinaxis, Aveva, and others can enhance efficiency and effectiveness.
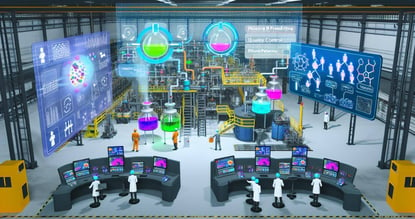
Predictive Quality Control Systems
Predictive quality control systems represent a paradigm shift in the approach to quality assurance. Instead of relying solely on post-production testing, these systems leverage advanced analytics, machine learning, and real-time data to anticipate and prevent defects before they occur. By analyzing historical data, process parameters, environmental conditions, and other variables, predictive quality control systems can identify patterns and anomalies that indicate potential quality issues.
This proactive approach not only minimizes the risk of non-conformities but also optimizes production processes for enhanced efficiency and yield.
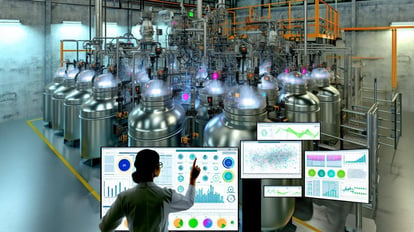
The Role of Production Planners
Production planners play a pivotal role in implementing and optimizing predictive quality control systems within chemical manufacturing facilities. As the orchestrators of production schedules, resource allocation, and inventory management, production planners are uniquely positioned to leverage predictive analytics to drive continuous improvement and operational excellence.
By integrating predictive quality control systems with ERP, SCM, and MES platforms, production planners can streamline workflows, anticipate resource requirements, and mitigate production risks in real-time.
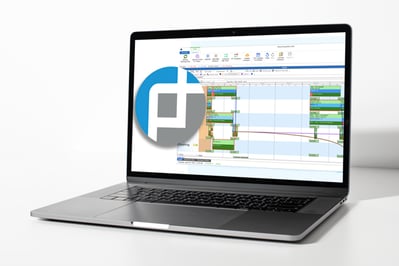
Integration with ERP, SCM, and MES Systems
Integration between predictive quality control systems and ERP, SCM, and MES platforms is essential for maximizing their potential impact. Let's explore how integration with leading platforms such as PlanetTogether, SAP, Oracle, Microsoft, Kinaxis, Aveva, and others can empower production planners:
Seamless Data Exchange: Integration enables seamless data exchange between predictive quality control systems and ERP, SCM, and MES platforms, ensuring a holistic view of production operations. Real-time data synchronization facilitates accurate demand forecasting, inventory management, and resource planning, enabling production planners to make informed decisions based on up-to-date information.
Enhanced Visibility and Traceability: By consolidating data from multiple sources, integration provides enhanced visibility and traceability across the entire supply chain. Production planners can track raw materials, work-in-progress, and finished goods throughout the manufacturing process, enabling proactive identification of quality issues and timely intervention to prevent defects.
Predictive Maintenance: Integration with MES systems enables predictive maintenance strategies, reducing downtime and optimizing equipment performance. By analyzing equipment sensor data and historical maintenance records, predictive quality control systems can anticipate maintenance needs and schedule preventive maintenance activities during planned production downtime, minimizing disruptions to operations.
Dynamic Production Scheduling: Integration with advanced planning and scheduling (APS) tools like PlanetTogether facilitates dynamic production scheduling based on real-time quality data. Production planners can optimize production schedules in response to changing demand, resource constraints, and quality requirements, ensuring on-time delivery without compromising quality standards.
Continuous Improvement: Integration enables closed-loop feedback mechanisms that drive continuous improvement initiatives. By capturing quality data at every stage of the production process, predictive quality control systems provide valuable insights for root cause analysis, process optimization, and corrective action implementation. Production planners can collaborate with cross-functional teams to address underlying issues and drive incremental quality improvements over time.
Predictive quality control systems represent a transformative opportunity for production planners in chemical manufacturing facilities to enhance quality, efficiency, and competitiveness. By leveraging advanced analytics, machine learning, and integration with ERP, SCM, and MES platforms such as PlanetTogether, SAP, Oracle, Microsoft, Kinaxis, Aveva, and others, production planners can proactively manage quality risks, optimize production processes, and drive continuous improvement initiatives.
Embracing predictive quality control systems is not just a technological advancement but a strategic imperative for chemical manufacturers seeking to thrive in an increasingly competitive marketplace.
Are you ready to take your manufacturing operations to the next level? Contact us today to learn more about how PlanetTogether can help you achieve your goals and drive success in your industry.