Adaptive Quality Inspection Prioritization
Efficiency is not just a buzzword but a crucial factor that can make or break success in packaging manufacturing. One of the pivotal areas where efficiency plays a significant role is in quality inspection processes. Traditionally, quality inspections have followed a rigid pattern, often resulting in bottlenecks and inefficiencies.
However, with the advent of advanced manufacturing IT solutions and integration capabilities, a new approach to quality inspection prioritization has emerged – one that is adaptive and tailored to the ever-changing demands of the industry.
In this blog, we'll look into the concept of adaptive quality inspection prioritization and explore how integration between PlanetTogether and leading ERP, SCM, and MES systems such as SAP, Oracle, Microsoft, Kinaxis, and Aveva can revolutionize quality management in packaging manufacturing facilities.
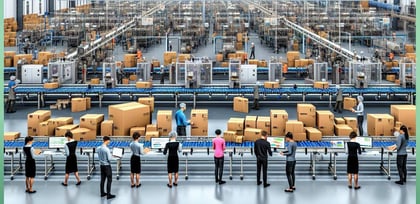
Understanding Adaptive Quality Inspection Prioritization
Quality inspection is a critical step in the manufacturing process, ensuring that products meet stringent standards before they reach the market. Traditionally, quality inspection prioritization followed a predefined schedule or hierarchy, often based on factors such as production volume, product type, or regulatory requirements. While this approach served its purpose, it lacked the agility needed to respond to real-time changes in demand, supply chain disruptions, or evolving customer preferences.
Adaptive quality inspection prioritization, on the other hand, embraces flexibility and responsiveness. It leverages data-driven insights, real-time analytics, and advanced algorithms to dynamically adjust inspection priorities based on a multitude of factors. These factors can include production schedules, material availability, equipment status, historical quality data, and even external influences such as market trends or regulatory updates.
Key Benefits of Adaptive Quality Inspection Prioritization:
Enhanced Flexibility: By dynamically adjusting inspection priorities, manufacturers can adapt to changing production schedules, minimize downtime, and optimize resource utilization. This flexibility allows for a more agile response to market fluctuations and customer demands.
Improved Quality Control: By focusing inspection efforts on high-priority areas or critical stages of the production process, manufacturers can ensure that quality standards are consistently met. Real-time monitoring and analytics enable early detection of defects or deviations, reducing the risk of product recalls or customer dissatisfaction.
Efficient Resource Allocation: Adaptive prioritization helps optimize the allocation of resources, including manpower, equipment, and materials. By directing resources where they are most needed, manufacturers can streamline operations and minimize waste, leading to cost savings and improved profitability.
Seamless Integration: Integration between advanced manufacturing IT solutions such as PlanetTogether and ERP, SCM, and MES systems facilitates seamless data exchange and collaboration across different functional areas. This integration enables a holistic view of the manufacturing process, from production planning to quality management, ensuring alignment and coherence across the entire value chain.
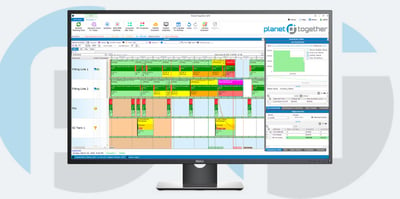
Integration with Leading ERP, SCM, and MES Systems
The integration between PlanetTogether and leading ERP, SCM, and MES systems represents a game-changer for packaging manufacturers seeking to implement adaptive quality inspection prioritization. Let's explore how this integration enhances efficiency and effectiveness:
SAP Integration: SAP's comprehensive suite of enterprise solutions, combined with PlanetTogether's advanced planning capabilities, enables real-time synchronization of production schedules, inventory levels, and quality data. This integration ensures that quality inspection priorities are aligned with production objectives and business goals.
Oracle Integration: Oracle's robust SCM and MES offerings complement PlanetTogether's planning and scheduling capabilities, providing end-to-end visibility and control over the manufacturing process. Seamless integration allows for proactive quality management, with timely interventions to address potential issues before they escalate.
Microsoft Integration: Microsoft's ecosystem of productivity tools, combined with PlanetTogether's optimization algorithms, enables data-driven decision-making and continuous improvement. Integration with Microsoft Dynamics and other ERP systems streamlines communication and collaboration, fostering a culture of agility and innovation.
Kinaxis Integration: Kinaxis' cloud-based SCM platform, RapidResponse, integrates seamlessly with PlanetTogether, enabling real-time scenario analysis and predictive modeling. This integration empowers manufacturers to anticipate quality-related risks and proactively mitigate them, ensuring consistent product quality and customer satisfaction.
Aveva Integration: Aveva's MES solutions, coupled with PlanetTogether's production planning capabilities, provide a unified approach to quality management and process optimization. Integration with Aveva's Wonderware and other industrial software platforms enables manufacturers to achieve operational excellence and regulatory compliance.
In the competitive landscape of packaging manufacturing, adaptive quality inspection prioritization is no longer a luxury but a necessity. By embracing flexibility, leveraging advanced technologies such as PlanetTogether, and integrating with leading ERP, SCM, and MES systems, manufacturers can enhance efficiency, improve quality control, and stay ahead of the curve.
As we look towards the future, the convergence of manufacturing IT solutions and digital transformation initiatives will continue to drive innovation and unlock new opportunities for growth. By harnessing the power of adaptive quality inspection prioritization, packaging manufacturers can navigate challenges with confidence and deliver superior products that meet the highest standards of quality and reliability.
Are you ready to take your manufacturing operations to the next level? Contact us today to learn more about how PlanetTogether can help you achieve your goals and drive success in your industry.